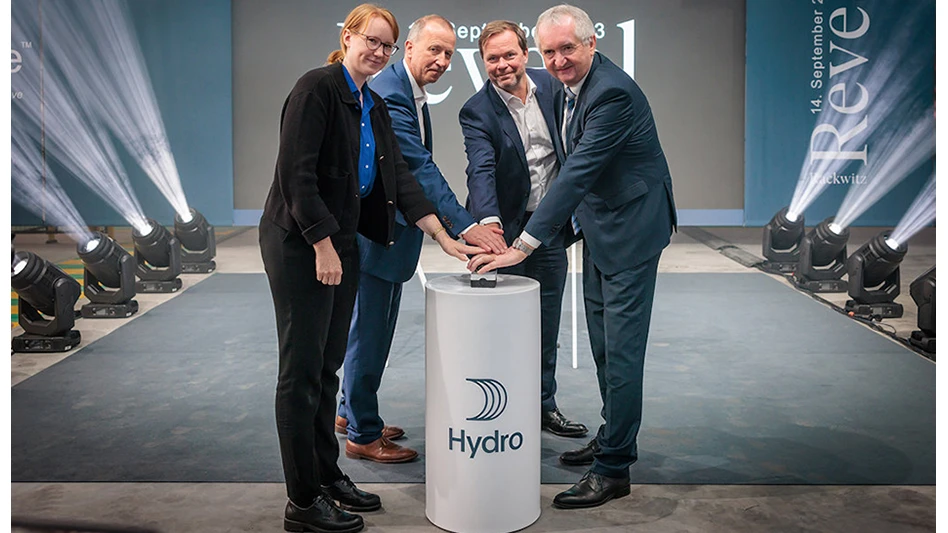
Photo by Marco Prosch and courtesy of Norsk Hydro
Norway-based aluminum producer Norsk Hydro says it has started operating a new HyForge casting line at its recycled-content aluminum casting plant in Rackwitz, Germany. The company says its $42.5 million investment will help address “the automotive industry’s drive to decarbonize, significantly increasing the use of recycled, postconsumer aluminum scrap” in the aluminum it uses.
A mid-September opening ceremony “marked the end of a 14 month construction process and the introduction of Hydro’s innovative HyForge forge stock segment at the Rackwitz plant,” says Hydro.
The company says the HyForge technology serves customers by providing smaller diameter cast aluminum forge stock billets “with a superior surface quality that can be forged directly into high-quality automotive components and other products, skipping further process steps such as extrusion or homogenization.”
“With HyForge, Hydro is literally forging the future of automotive, responding to the industry’s increasing demand for low-carbon, lightweight aluminum components,” says Eivind Kallevik, an executive vice president with Hydro Aluminium Metal.
“The expansion enables us to further develop our strategic partnership with automotive customers, while meeting both their high quality standards and increasing focus on sustainability,” adds Kallevik.
The Rackwitz expansion also represents a step toward Hydro’s goal of doubling its use of postconsumer aluminum scrap by 2025. “It is also delivering on the ambition to recycle more locally sourced scrap to ensure market leading sustainability performance,” adds the company.
“Our plant in Rackwitz is ideally located to serve the region’s automotive industry hub as more customers pursue their aim to decarbonize,” says Thomas Stürzebecher, managing director at the Rackwitz plant. “It also provides easy access to sources of postconsumer aluminum scrap, giving significant customer value, and contributing to the circular economy and Germany’s green transition.”
According to Hydro, Germany alone accounts for one-third of the total European aluminum consumption. “It is a large market for Hydro, consisting of customers with ambitious climate targets that are clearly reflected in their expectations from suppliers like Hydro,” states the Norwegian firm.
Hydro says it has been working to decarbonize its operations since the 1990s, and that the recycling of postconsumer scrap such as used beverage cans (UBCs), window frames, car parts and other discarded “is one of the pathways in Hydro’s roadmap to cut emissions and the fastest way to deliver zero-carbon aluminum.”
The new HyForge line has a capacity of 25,000 metric tons per year, which has been added to the facility’s current annual production of 95,000 metric tons of extrusion ingot.
The new production line, known as Hydro Aluminium Gießerei Rackwitz, is located next to Hydro Extrusions Rackwitz. The two plants share a common cast house that provides much of the recycled-content raw material for the extruded and cast products made there.
Latest from Recycling Today
- ArcelorMittal puts French EAF conversions on hold
- Associations ask for effective EPR to drive textile circularity in Europe
- GESA report claims 72 countries recycled EPS in 2023
- Report: Saica exploring recycled paper mill project in Dayton, Ohio
- Hydro’s Alumetal to meet 15 percent of its energy demands through solar
- CSA Group publishes standard defining plastics recycling in Canada
- Second Cyclyx Circularity Center to be located near Fort Worth, Texas
- Sennebogen machinery keeps material moving at German recycling plant