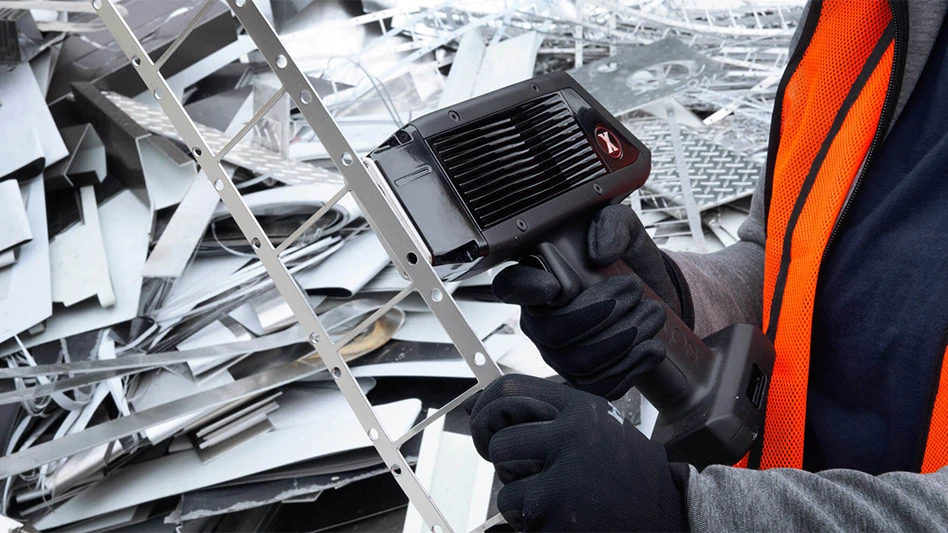
Photo courtesy of SciAps
In terms of time savings, the most efficient way to purchase scrap might involve a quick visual inspection at the scale house or an industrial account buyer assuming the bins being picked up at a factory are uniform and as described by the generating company.
Veteran scrap recyclers, however, are well aware that the additional effort and investment of analyzing the inbound metal—particularly nonferrous alloys—can provide ongoing benefits to their bottom lines.
Processors operating in the 2020s are fortunate to benefit not only from the current competitive landscape among metals analyzer manufacturers but also from decades of previous competition that have spurred advances and improvements.
Fast forward
In the middle decades of the 20th century, benchtop spectrometers offered one of the few options available to scrap processors. These devices were helpful in distinguishing alloys from one another, but the investment involved often appeared only to recyclers who specialized in such alloys, likely for geographic (nearby scrap generator) reasons.
That started changing in the 1980s and 1990s, when portable “gun” analyzers were introduced to the market. In a 2021 interview with Recycling Today, Don Sackett of United States-based SciAps Inc. described the first such units as “semiportable” and made by U.S.-based Texas Nuclear and Finland-based Metorex.
Most of the first generation of gun analyzers featured X-ray fluorescence (XRF) technology. According to Sackett, such analyzers are capable of measuring transition and heavy metals, including titanium, chromium, manganese, nickel, cobalt, niobium and tungsten. “These metals and related alloys also tend to be the higher priced material for resale after sorting,” he noted.
Modifications and improvements in XRF technology have followed, and XRF also has been joined by new methods of measuring the chemistry of a metal object or sample.
Laser-induced breakdown spectroscopy (LIBS) devices were designed to analyze the light elements, including aluminum, magnesium and silicon. They have found a popular niche in aluminum alloy sorting.
Also pointed out by Sackett, LIBS devices eliminated the regulatory and safe handling measures involved with using an X-ray radiation device found in XRF models.
For the most part, when a scrap processor in the 2020s decides its time to invest in an analyzer, the research involves not finding a suitable model, but likely choosing between several.
Making their case
The Niton brand, now owned by the global Thermo Fisher Scientific company, makes its case to recyclers by stating, “With today’s volatile commodity prices, the need for sorting recycled metals quickly and with accuracy is critical.”
The company offers several models of XRF gun analyzers, with some of its most popular models also using its geometrically optimized large area drift detector (GOLDD) technology.
Of interest to both recyclers and melt shop scrap buyers, Niton says its XL3t GOLDD+ Series guns offer the “best detection limits for tramp/trace elements.” The company says that series of guns also offers lab-quality performance for sorting aluminum, titanium, bronze, zinc, high-temp alloys and specialty steels.
Sackett’s company SciAps offers both XRF and LIBS analyzer guns. Among several ways the company tries to differentiate itself, SciAps says it offers tube or detector replacements at less than half the price of some of its competitors. “At SciAps, we view service as a loyalty program, not a profit center,” the firm says.
Bruker, which has roots in Germany but like SciAps, Niton and Thermo Scientific is based in Massachusetts, continues to offer an older style spark emission spectrometer while also designing and making XRF hand-held analyzers.
In a September 2022 writeup promoting its presence in the scrap recycling sector, Bruker refers to XRF as “the most accepted technology” for the task of properly identifying both ore samples and inbound scrap.
Bruker points to its S1 Titan hand-held XRF model when saying that scrap yard operators “can quickly sort mixed scrap, separating materials through the instrument’s comprehensive grade library.”
Using the hand-held XRF, Bruker says, recycled material can be accurately quantified through elemental analysis, “ensuring the correct quality of scrap metal goes forward” to the melt shop destination. There, says Bruker, “even small percentages of tramp elements, which may degrade the final alloy, can be determined before further processing.”
The wider presence of metals analysis in scrap yards around the world seems to be a testament to good R&D efforts performed to serve a growing industry sector.
Get curated news on YOUR industry.
Enter your email to receive our newsletters.Latest from Recycling Today
- ICM to host co-located events in Shanghai
- Astera runs into NIMBY concerns in Colorado
- ReMA opposes European efforts seeking export restrictions for recyclables
- Fresh Perspective: Raj Bagaria
- Saica announces plans for second US site
- Update: Novelis produces first aluminum coil made fully from recycled end-of-life automotive scrap
- Aimplas doubles online course offerings
- Radius to be acquired by Toyota subsidiary