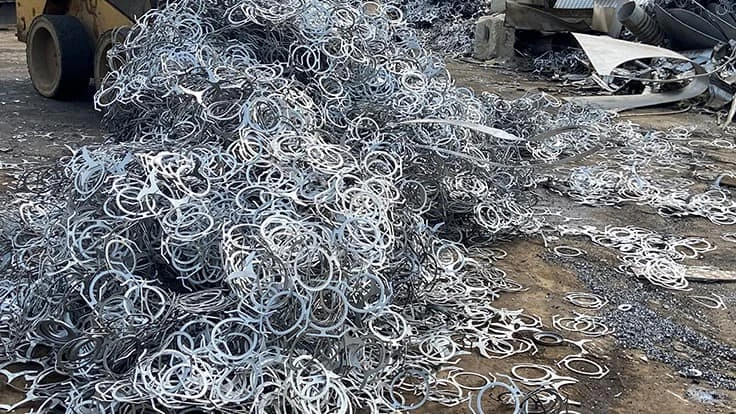
Photo by Brian Taylor.
Analyzing the chemistry of inbound material has long been beneficial for buyers of scrap metal, with different aluminum, stainless and red metal alloys yielding different prices on the market.
Methods of identification and analysis have evolved over the course of several decades, but one of the bigger leaps came about in the 1990s when hand-held portable analyzer “guns” started becoming more widely available (and affordable) to scrap recyclers
For an overview of how this type of equipment has evolved and where it currently stands, Recycling Today has interviewed industry veteran Don Sackett, the co-founder and CEO of United States-based SciAps Inc.
Recycling Today (RT): Why were the first metals analyzing “guns” created back in the mid- and late 1990s, and what equipment or processes could they replace?
Don Sackett (DS): There were two semiportable “guns” available in the mid -1980s through the late 1990s. One was made by Texas Nuclear (TN) and the other by Metorex (a Finnish company). Prior to these “guns” scrap processors used a number of techniques to sort material at a very basic level. The simplest was the grinding wheel. Stainless steel, nickel alloys and titanium alloys, for example, all emit different color light and shape of sparks when hit with a grinding wheel.
Some recyclers used magnets, knowing that some alloys like a Monel (nickel-copper alloy) slightly pull on a magnet, or stainless, which doesn’t in comparison to a ferrous material. Also, there was a device called the “foos,” where you turned a handle rapidly, looked through an optic, and by viewing the different color spectral lines, could determine the likely alloy type. All of these techniques required either a very knowledgeable operator, or they only sorted crudely by alloy type (e.g., a titanium alloy versus a copper alloy, etc.).
When the first spectrometers came out, like the TN and Metorex analyzers, operators could then sort by grade as opposed to just alloy type. For example, they could determine if the alloy was a titanium 6-4 or 6-6-2 or 6-2-4-2 instead of just a titanium grade. The same goes for the wide variety of nickel and nickel/copper superalloys. Thus, this generation of “guns” allowed recyclers to sort alloys much more specifically, faster, allowing them to sell the sorted product at higher prices. Also, unlike the older techniques, many more operators could become proficient at using these analyzers faster, eliminating the purely “tribal knowledge” approach to metal sorting.
I have not yet mentioned the mobile arc/spark spectrometers. These devices also were available in the early ‘90s, perhaps earlier. They were not hand-held and required a high degree of operator knowledge to get good sorting results, but these OES (optical emission spectroscopy) devices were also highly selective alloy sorters. Also, unlike the XRF (X-ray fluorescence) units (TN and Metorex) the spark units were much better on aluminum alloys, and the lighter elements (magnesium, silicon, aluminum, phosphorus, sulfur) in general. And, they did not use a radioactive isotope as their excitation, also an advantage.
RT: Which metals were targeted initially for portable analysis? What upgrades to hand-held analyzers have been the focus of R&D subsequently?
DS: XRF portable analysis excels at measuring transition and heavy metals, including titanium, chromium, manganese, nickel, cobalt, niobium, tungsten, etc. These metals and related alloys also tend to be the higher priced material for resale after sorting. Thus, the hand-held XRF units in the 1990s and 2000s initially targeted stainless and high-temp alloys and some red metals. They did this because the technique is ideal for these types of elements/alloys (still is) and because these alloys commanded higher prices than aluminum or ferrous.
There were three major upgrades to the handhelds during the past 20 years. The first upgrade occurred around 2002, when two companies (InnovX and Niton, now Olympus and Thermo Fisher respectively) replaced the radioactive isotope with a miniature X-ray tube. The X-ray tube had two significant advantages over the radioactive source. First, it wasn’t radioactive, so the regulatory requirements were far less stringent both in costs and paperwork headaches, especially post 9/11 when everyone feared dirty bombs. The second was that the X-ray tube could excite a wider range of elements. In the old isotope XRF units, you needed three different radioactive sources to see the full range of elements from titanium to bismuth. The X-ray tube could output X-rays that could excite all these elements.
The second major upgrade occurred in the 2009 to 2010 time frame, when a new detector technology called silicon drift detectors (SDDs) became available in handhelds. Again, InnovX and Niton (now Thermo) introduced these innovations. These SDD detectors replaced the prior detector technology called PiN diode detectors. The SDD’s offered three substantial advantages: a) They could count X-rays about 10 times faster than the PiN, meaning that a given measurement achieved higher precision, three times faster in time; b) the SDDs could measure all the way down to milligrams, which then meant that hand-held XRF guns could do a good job measuring aluminum and magnesium alloys, and also measure phosphorus and sulfur in steels and coppers. Until SDDs became available, hand-held XRF units really could only sort aluminum alloys crudely, by major series like 2024 type or 3003 type, since they could not measure silicon or magnesium and, thus, could not distinguish, for example, a 2024 from a 2014, etc.
The third major upgrade came in the form of an alternative technology to hand-held XRF guns. In 2015 or thereabouts, SciAps, Hitachi and TSI all introduced hand-held devices using a laser, rather than X-ray, to excite the material. These devices were called LIBS (laser-induced breakdown spectroscopy). The early devices offered better performance on the “light elements” (silicon, magnesium and aluminum) and thus were largely used for aluminum alloy sorting. They also offered the advantage of completely eliminating X-ray radiation, and thus the registration requirements that ionizing radiation like X-rays required from some – not all – state agencies. In the early days, many believed that the LIBS devices would completely replace XRF units. However, over time it became clear that XRF remained a superior technology on stainless, high temps and often red metals, which relegated LIBS to aluminum alloys (where it’s very good) and niche applications like measuring lithium in aluminum, beryllium in copper alloys, boron in aluminum, stainless steels and nickel alloys – basically elements that XRF couldn’t measure. In some cases, recyclers have switched to LIBS for all their operations because they wanted to eliminate radiation-based units (X-ray tubes) entirely, regardless of the fact that XRF provides superior results on stainless and high temps.
RT: How can the SciAps X-550 help aluminum recyclers be more profitable? What are the ideal applications for this model? (At the scale house; elsewhere in the field?)
DS: At SciAps, we were always bothered that XRF technology was viewed so poorly for aluminum alloys. There’s good reason for this. To sort aluminum alloys effectively and fast, you need to measure magnesium fast, and silicon also. Now, the X-rays emitted by magnesium are very low in energy—they are easily blocked by air and other materials—so it is very difficult to measure magnesium by a hand-held XRF. At SciAps, when we started designing the X-550, we knew we could measure stainless and high temps fast and precisely – just as most other hand-held XRF brands can do. So, we decided to focus our design effort on fast measurements of magnesium and silicon. Do that and you can do a great job on aluminums because the other elements in aluminum alloys (like chromium, manganese, copper, zinc, zirconium and nickel) are a natural for XRF. So, we created a really fast XRF for aluminum alloys – as fast as it is on high temps or stainless. This creation inevitably leads to more profitability on aluminum. Aluminum is light weight, so you have to sort a lot of it quickly to make money. The X-550 was designed for just that --- be fast and precise on aluminum alloys as well as everything else. The key was our design that yielded fast magnesium and silicon measurements.
In terms of ideal applications – scale house, aluminum and red metals station, or turnings. Because the X-550 is fast and precise on both aluminum and other metals, you can use it anywhere.
RT: What might be the next frontier or new applications for hand-held analyzers?
DS: I’d say the next frontier is to make limits of detection lower and lower. For example, in oil and gas, they are requiring the steel to have low residuals for many applications. This means the sum of chromium plus copper plus nickel at less than 0.15 percent and also niobium and vanadium at less than 0.02 percent, with niobium plus vanadium at less than 0.03 percent. The consumers are pushing these limits onto the foundries. The foundries use a lot of recycled steel, so they want material that meets these requirements from the recyclers. In turn, the recyclers can charge a premium if they can guarantee residual metals meet the various upper limits. We’re hearing this for certain elements in nickel and copper alloys too. Therefore, is believe that the next generation hand-held units need to drive limits of detection lower and lower.
Latest from Recycling Today
- Green Cubes unveils forklift battery line
- Rebar association points to trade turmoil
- LumiCup offers single-use plastic alternative
- European project yields recycled-content ABS
- ICM to host colocated events in Shanghai
- Astera runs into NIMBY concerns in Colorado
- ReMA opposes European efforts seeking export restrictions for recyclables
- Fresh Perspective: Raj Bagaria