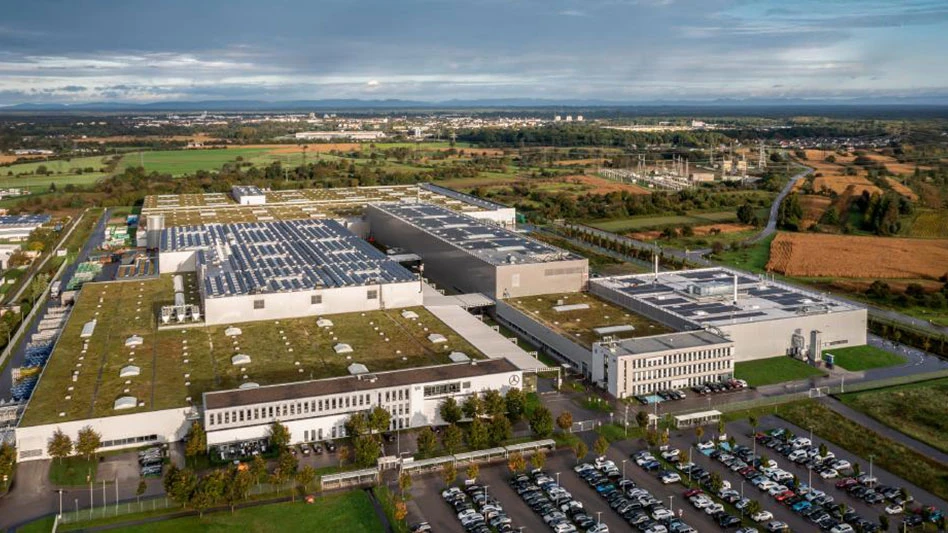
Photo courtesy of Mercedes-Benz Group
Mercedes-Benz Group AG has opened a battery recycling plant with an integrated mechanical hydrometallurgical process in Kuppenheim, Germany.
According to Mercedes-Benz, based in Germany, the expected recovery rate of the recycling plant is more than 96 percent. The plant will recover lithium, nickel and cobalt, which it says can be used in new batteries for future Mercedes-Benz electric vehicles (EVs). The company has invested tens of millions of euros in the construction of the new battery recycling plant.
Federal Chancellor Olaf Scholz and Thekla Walker, environment minister of Baden-Württemberg, Germany, visited the plant for the opening ceremony.
“The future of the automobile is electric, and batteries are an essential component of this,” Scholz says. “To produce batteries in a resource-conserving and sustainable way, recycling is also key. The circular economy is a growth engine and, at the same time, an essential building block for achieving our climate targets. I congratulate Mercedes-Benz for its courage and foresight shown by this investment in Kuppenheim. Germany remains a cutting-edge market for new and innovative technologies.”
“Mercedes-Benz has set itself the goal of building the most desirable cars in a sustainable way,” says Ola Källenius, chairman of the board of management at Mercedes-Benz. “As a pioneer in automotive engineering, Europe’s first integrated mechanical hydrometallurgical battery recycling factory marks a key milestone towards enhancing raw materials sustainability. Together, with our partners from industry and science, we are sending a strong signal of innovative strength for sustainable electric mobility and value creation in Germany and Europe.”
Mercedes-Benz says the plant’s mechanical process sorts and separates plastic, copper, aluminum and iron in a multistage process, with the downstream hydrometallurgical process dedicated to black mass. Cobalt, nickel and lithium are extracted individually in a multistage chemical process.
The company says the hydrometallurgical process is less intensive than pyrometallurgy, which has already been established in Europe. According to Mercedes-Benz, the process’ temperatures of up to 176 degrees Fahrenheit consume less energy than other processes. Additionally, the new plant operates at net carbon-neutral and is supplied with 100 percent green electricity, the company says. The roof of the building has been equipped with a photovoltaic system with a peak output of more than 350 kilowatts.
The plant has an annual capacity of 2,500 metric tons (approximately 2,755 tons), and the company says the recovered materials will contribute to the production of more than 50,000 battery modules for future Mercedes-Benz EVs.
“We are systematically deepening our expertise in the battery value chain,” says Jörg Burzer, member of the board of management at Mercedes-Benz Group, responsible for production, quality and supply chain management. “Following the opening of the Mercedes-Benz eCampus for development of new battery cell chemistries in Stuttgart-Untertürkheim, we are now sustainably closing the raw materials loop in Kuppenheim. The innovative technology enables us to recover valuable raw materials from the battery with the highest possible degree of purity. This turns today’s batteries into tomorrow’s sustainable mine for raw materials. The new battery recycling plant strengthens the role of the Mercedes-Benz production network with vehicle and drivetrain plants in Europe.”
Mercedes-Benz says it considers three core topics when approaching the circularity of battery systems: circular design, value retention and closing the material loop. The company also offers reconditioned batteries as spare parts for its electric vehicles, and its Mercedes-Benz Energy subsidiary has established a business model with large-scale stationary storage applications.
Hilchenbach, Germany-based Primobius, a joint venture between plant and mechanical engineering company SMS group and process technology developer Neometals, is Mercedes-Benz’ technology partner for the battery recycling plant. The German Federal Ministry for Economic Affairs and Climate Action has provided funding to the plant as part of a scientific research project with three German universities examining the recycling value chain.
Latest from Recycling Today
- BASF collaborates to study mechanical plastic recycling
- Commentary: navigating shipping regulations for end-of-life and damaged batteries
- Haber raises $44M to expand to North America
- Canada Plastics Pact releases 2023-24 Impact Report
- Reconomy brands receive platinum ratings from EcoVadis
- Sortera Technologies ‘owning and operating’ aluminum sorting solutions
- IDTechEx sees electric-powered construction equipment growth
- Global steel output recedes in November