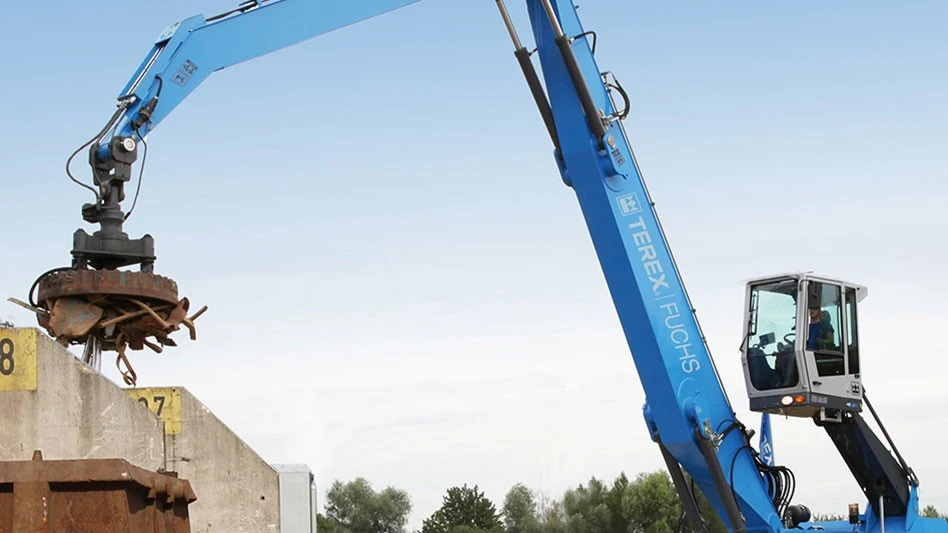
Photo from Recycling Today's archives
Demand for magnetic scrap handling attachments has increased by 30 percent since the start of the COVID-19 pandemic for some equipment dealers such as Nasco-Op based in New Philadelphia, Ohio.
Despite the increase in demand, Mike Morrison, assistant manager of Nasco-Op, says the attachments are hard to come by because of a shortage of parts needed to make them. This delay means magnets are taking three to five months to assemble and ship. As a result, it has become increasingly important to maintain existing equipment and to know when it’s time to replace an attachment.
“How long your magnet lasts is based on the preventative maintenance, how you take care of your magnet [and] having an experienced operator running your material handler,” Morrison says. “When it comes down to the magnet, it could last two years or it could last 20 years, all depending on how well it's maintained and how well your operator uses it.”
Three parts on a magnet wear down most quickly:
- the chain that holds the magnet, which gets worn because it lifts the magnet, swings it into position and lowers it, placing continuous strain on the chain;
- the magnetic leads that attach the material handler to the coil of the magnet; and
- the magnet's face.
Morrison says some operators use the magnet face to pick up material and distribute it into trucks. The jagged edges of the material will chip away at the face slowly, weakening how effective the magnet will be in the long run.
“As with any electrical piece of equipment, there are going to be components that wear out, especially if there's an issue in your magnet control system somewhere,” Morrison says. “You’ll need to maintain your magnet, the magnet controller, the generator and all the cables that connect everything in between. If everything isn’t working in sync, you can burn up components of the control system pretty quickly.”
Morrison suggests operators check these three parts monthly to avoid lasting damage to the attachment. Operators should look for cracks, broken links in the chain and excessive wear. Operators also should keep chains clean and free of grease, and operators should not rest the material handler’s boom on the chain.
Other ways an operator can ensure the effectiveness of a magnetic attachment include storing it in a dry place that’s not too hot or too cold, depending on the business' location. Operators also should avoid using it for anything other than picking materials up, such as flattening material or sweeping it across the ground to pick up small metal scrap.
While maintaining a magnetic attachment is important, there comes a time when it makes more sense to replace the attachment. Repairing a magnet could cost 60 percent to 75 percent of the cost to buy a new magnet entirely.
“You're shipping something that's very heavy back to a manufacturer. They have to do double the labor now because they have to a inspect the magnet, tear it down and see what's wrong with it. They have to go through the coil, they have to go through all the components, see what's working what's not,” Morrison says. “Then they have to also put it back together. So really, you're doubling the labor that you would have for a new build because labor is the most expensive part of the repair.”
Morrison says, typically, a repaired magnet is going to be rebuilt using recycled parts. This means it might not last as long as a magnet using new parts.
The primary sign it’s time to replace a magnet that operators should look for is the wear depth of the pole. If the magnet’s bottom plate is flat with the outer pole, the magnet is at end of its life. If the magnet is used past this point, an operator might see warping and welding breaks that eventually will lead to the magnet failing or the bottom plate possibly falling out of the attachment.
Other signs the magnet should be replaced is if the operator is experiencing electrical issues while using the attachment. If an operator sees spikes or power shorts in the system, it could mean the system needs to be inspected.
If a magnet continues to be used after it should be replaced, the operator will experience ongoing issues during use.
“You're going to have issues with your magnet controller, you're going to have issues with your generator, you're going to have issues with the other components of a magnet system that don't necessarily tie right into the magnet itself,” Morrison says. “When that magnet is beat up and broken down, you're going to have electrical issues one way or another. Whether it be a moisture issue, short in the coil or your magnet control system.”
Latest from Recycling Today
- Reconomy brands receive platinum ratings from EcoVadis
- Sortera Technologies ‘owning and operating’ aluminum sorting solutions
- IDTechEx sees electric-powered construction equipment growth
- Global steel output recedes in November
- Fitch Ratings sees reasons for steel optimism in 2025
- P+PB adds new board members
- BlueScope, BHP & Rio Tinto select site for electric smelting furnace pilot plant
- Magnomer joins Canada Plastics Pact