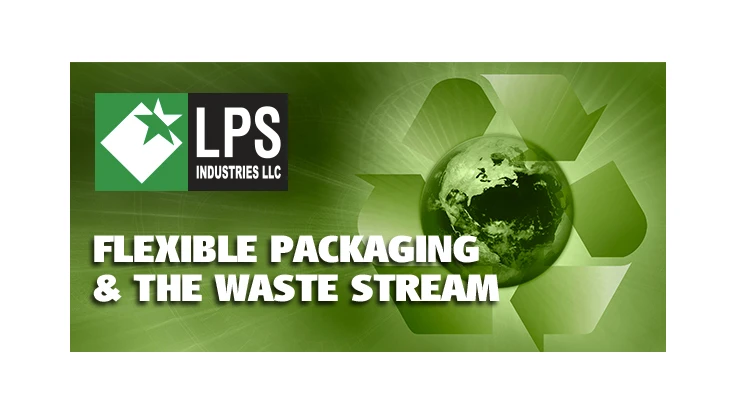
Packaging and label maker LPS Industries, Moonachie, New Jersey, says the numerous types of flexible packaging required to protect and market food, beverages and other products likely will require several different diversion options to keep the material out of the landfill.
An increased focus on the back end of the product life cycle has companies recognizing that there never was a “silver bullet” solution, the company says in an essay sent to media outlets. “Adopting a strategy of incremental change, in a series of practical and societally acceptable steps, is the best strategy to address a long term solution,” says LPS.
The company writes, “In the flexible packaging industry, it seems that as the complexity of the construction increases, so do the downstream recycling and waste management challenges. An example familiar to all starts with the polyethylene (PE) bag, used in most grocery stores. It can be relatively easily recycled due to its single layer composition. However, the same grocery stores contain shelves full of multilayer packaging options used for moisture barrier protection of the contents. These cannot be recycled because materials in addition to polyethylene are used to generate the moisture protection the barrier film is designed to deliver.”
While recycling some packages back to their component resins or elements may be difficult, LPS says, “Many of the more complex flexible packaging structures are candidates for waste-to-energy conversion technologies such as gasification. Whether it’s recycling, waste-to-energy conversion, composting or landfill disposal, the opportunities for responsibly handling flexible packaging in the waste stream are becoming as diverse as the materials themselves.”
According to Charles Ardman, the vice president of marketing at LPS Industries, the company was an early adopter of environmentally friendly practices from both a product and process standpoint. On the product front, LPS has built out its packaging and shipping supplies portfolio over the last 10 years with products that contain recycled material or are biodegradable while continually evaluating new barrier materials for their brand owner customers, he says.
Examples of such measures include installing a rooftop solar energy system in 2010 that offsets annual CO2 emissions by more than 500 tons and converting to a solvent-free lamination process that eliminates the production of volatile organic compounds (VOCs) and their requisite disposal while providing a safer environment for the LPS workforce.
States Ardman, “While there is no ‘silver bullet’ for this complex challenge, LPS Industries will continue to work closely with our suppliers and customers and actively participate through our trade association to influence evolving regulations. Our goal is to continually identify and implement smart, eco-friendly improvements in support of decreasing the impact of flexible packaging on the waste stream.”
LPS Industries was founded in 1959 by John M. Robinson primarily as a converter of military-specification barrier materials. Today, under the direction of its CEO Madeleine D. Robinson, the company describes itself as a diversified manufacturer that provides packaging solutions for a diverse range of markets, including the medical, food, transportation, electronics and agricultural sectors.
Latest from Recycling Today
- ReMA board to consider changes to residential dual-, single-stream MRF specifications
- Trump’s ‘liberation day’ results in retaliatory tariffs
- Commentary: Waste, CPG industries must lean into data to make sustainable packaging a reality
- DPI acquires Concept Plastics Co.
- Stadler develops second Republic Services Polymer Center
- Japanese scrap can feed its EAF sector, study finds
- IRG cancels plans for Pennsylvania PRF
- WIH Resource Group celebrates 20th anniversary