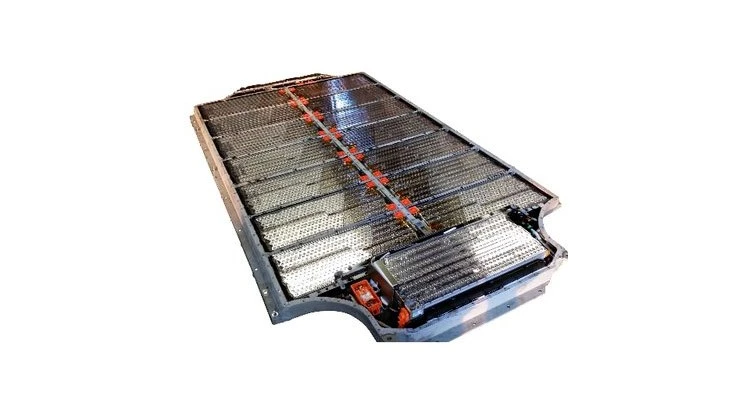
Automotive and electric power industry leaders facing flat sales envision a more prosperous future with massive new investments in an electrified vehicle-to-grid infrastructure.
These leaders say they are confident people will want to travel in “clean” vehicles seamlessly integrated with the electric power grid and connected to all forms of communication. This modernized grid will function with clean energy from wind and solar facilities rather than pollution-emitting fossil fuels.
This would seem like a can’t miss proposition, but there are hurdles. One is avoiding new hazardous pollution risks from the use of rare earth and specialty materials to achieve the goal of clean energy.
From established to emerging
Advocates of this transportation and electric power convergence must confront the consequences of moving away from highly recyclable materials like copper and lead and replacing them with materials that are very difficult to recycle.
Specialty metals like lithium used in batteries and rare earth materials like samarium and neodymium used in magnets for electrified drive trains are among the least recycled materials in the world. Automotive and electric power industry executives could find themselves at odds with another worldwide environmental movement, the circular economy, which calls for discarded materials to be recycled and reused in new products rather than simply dumped in landfills.
The challenge for the automotive and electric utility industries is fairly simple to define, but very difficult to resolve. For nearly two hundred years, electric utilities have produced electricity with turbines (powered primarily either by hydro dams or fossil fuels) that maintained inertia for a stable flow of power through transmission lines. With the auto industry, inertia has been provided by the internal combustion engine powered with gasoline and diesel fuel. Both industries depend on insulated copper wires for electric power flow. Lead batteries are essential for automotive ignition and provide vital backup power for electric utilities.
For many years, hydro power, particularly pumped hydro storage plants, have supplied instantaneous bursts of power to ensure the stable flow of electricity from unanticipated power outages and a modest introduction of windmills and solar panels. But, because hydro power isn’t available everywhere, batteries have become an option. Some electric utilities are turning to powerful lithium-ion batteries of the type already used in appliances.
Lithium-ion batteries have become commonplace in cellular phones, handheld tools and appliances. They also are becoming a serious hazardous waste problem as consumers throw used appliances with lithium-ion batteries into the trash rather than take them to recycling centers. Explosions and fires are taking place in material recovery facilities (MRFs). In some cases, MRFs have been forced into shutdown for expensive repairs because of lithium battery explosions and fires.
This hazardous waste problem is becoming an important issue for automakers and electric utilities. A typical lithium-ion “18650” cell widely used in a small electric appliance is only slightly larger than a standard AA alkaline battery. These 18650 cells are used in electric vehicles as well. A Tesla battery pack is comprised of some 7,000 lithium-ion 18650 cells carefully arranged with a sophisticated cooling system to keep their temperature low to avoid a phenomenon called “thermal runaway” in which one over-heated cell can start a chain reaction among others in a battery pack.
Using 18650 cells in an electric power system puts this challenge on an even larger scale. A 30-megawatt lithium-ion battery system recently commissioned in California uses some 400,000 of these cells. Keeping the cells operating safely at low temperatures is a major engineering challenge. But, what happens when the cells no longer work?
Presently, federal law does not mandate the recycling of spent lithium-ion cells, primarily because no economically viable recycling program exists. End-of-life battery owners either toss them into landfills or pay extra to have them reduced into lower grade uses such as road slag. (Federal officials have only issued strict regulations on how they can be transported.)
The situation is considerably different with copper wires and lead batteries. Recycling these materials is a highly profitable business because recycled copper and lead are literally the same quality as “virgin” metals mined from the ground. Recycled copper and lead are traded on open commodities markets alongside their virgin counterparts.
Research, development and commitment
What is the solution to hazards created by the use of lithium-ion batteries and rare earth magnets? A ban on their use until a recycling industry is established? Impossible. The wireless communications industry, for example, would collapse. New government regulations mandating the recycling of spent lithium-ion batteries? At least five states already have such mandates, but their impact has been negligible. Consumers still are throwing lithium batteries into the trash.
Automakers and utilities are working feverishly to come up not only with management systems to keep these batteries running safely, but also to devise an economic process to recycle them and keep them out of MRFs and landfills.
This research requires a major commitment by industry and government. Automakers are working with the U.S. Department of Energy’s Vehicle Technologies Program, which is supporting work by a consortium of national laboratories and the U.S. Advanced Battery Consortium. Utilities are working with the Electric Power Research Institute and DOE.
Recently, these DOE programs survived cuts proposed by the Trump Administration to save money on research. Congress not only rebuffed these proposed cuts, lawmakers actually increased research budgets. This was because U.S. national laboratories have some of the world’s most powerful research equipment to study the behavior of materials to make them perform more efficiently and sustainably. No single industry, for example, could possibly afford equipment like the Advanced Photon Source at Argonne National Laboratory or the Spallation Neutron Source at Oak Ridge National Laboratory.
In the case of the auto industry, the DOE Vehicle Technologies (VT) program, with an annual budget of $337 million, is spending about half that amount on battery research, mostly lithium-ion batteries, not just to make them more powerful, but safe and recyclable. The DOE Basic Energy Science office is supporting work at Argonne to develop better alternatives to the lithium-ion battery.
But, what if all this research still does not result in major cost reductions required to make lithium batteries recyclable, electric vehicles more attractive to consumers and renewable power more cost effective for utilities?
There is a fallback. DOE’s VT program also is allocating more than $65 million to improve the performance of internal combustion engines. DOE’s fossil energy programs have more than $700 million. The lead battery industry is working with Argonne on a program to analyze the crystallization of lead plates. The copper industry is working with Oak Ridge on an ultra-conductivity program to increase copper wire performance. Both programs can help improve the competitive position of these highly recyclable metals.
The vehicle-to-grid revolution to green technologies may not happen all at once, but rather incrementally. The automotive and electric power industries, therefore, will have to assure consumers and investors they’re making the right choices on the way to a clean future.
(The author is a principal of Redland Energy Group, a Washington-based firm that focuses on marketing and policy consulting services to the energy sector.)
Latest from Recycling Today
- BlueScope, BHP & Rio Tinto select site for electric smelting furnace pilot plant
- Magnomer joins Canada Plastics Pact
- Out of touch with reality
- Electra names new CFO
- WM of Pennsylvania awarded RNG vehicle funding
- Nucor receives West Virginia funding assist
- Ferrous market ends 2024 in familiar rut
- Aqua Metals secures $1.5M loan, reports operational strides