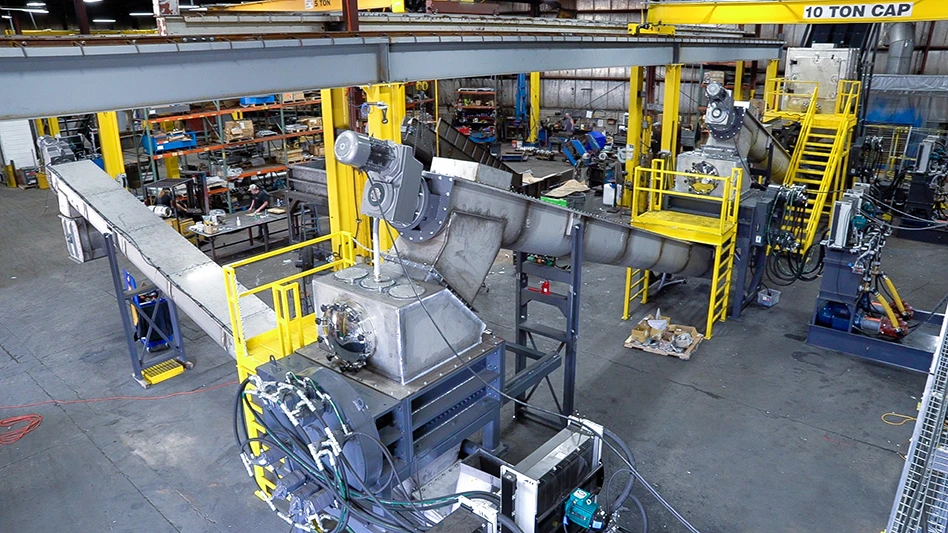
Photo courtesy of LithiBatt
LithiBatt, a Milwaukee-based division of recycling equipment producer BCA Industries founded in 2023, says it now provides an end-of-life electric vehicle (EV) battery pack processing system capable of handling large battery packs without requiring disassembly or discharge.
The company says the systems are designed “to seamlessly integrate as the ‘front end’ of existing recycling processes,” and they already have been put to use by large EV manufacturers in Germany, the United Kingdom and the United States.
“Battery recyclers require a comprehensive, turnkey solution designed to safely and efficiently shred the largest commercial EV battery packs on the market, without having to discharge the battery first,” says John Neuens, industrial consultant for LithiBatt.
The BCA Industries business unit describes itself as a producer of closed-loop recycling systems for lithium-ion, lithium-iron phosphate (LiFePO4), nickel-metal hydride, zinc-bromine and other types of batteries.
The large battery pack systems offered by LithiBatt “enable EV manufacturers and major recyclers to efficiently and safely recover valuable ferrous metals and battery-grade black mass,” says the firm. The company describes black mass as “a complex mix of metals such as lithium, cobalt, nickel and manganese that can be refined into precursor cathode active material (pCAM) through hydrometallurgical processes by the recycler themselves or third-party buyers of black mass.”
The firm says shredding of large battery packs comes with considerable safety and processing challenges. However, “Through extensive research, design, and production testing, LithiBatt engineered a fully sealed system incorporating a water-nitrogen blanket, lift-and-dump mechanism, three-part progressive shredding [and an] air and water treatment system along with other unique design features.”
Neuens says, “The hydro-nitrogen ‘large pack’ battery recycling systems can safely process anything from multiple smaller packs and modules to whole battery packs used in electric trucks and SUVs.”
He says the system can shred battery packs that measure 70 inches by 118 inches by 15 inches and weigh more than 1,700 pounds.
The system’s inert nitrogen environment stops fire-starting thermal runaway by "substantially reducing the available oxygen concentration, which is crucial for combustion and the propagation of a fire within a battery experiencing thermal runaway,” according to the company.
LithiBatt’s “lift and dump” loading system means whole, charged packs battery packs up to six feet wide and 3,000 pounds in weight can be fed into the submerged primary shredder. “The lift is designed to seal against the surface of the first chamber, open a tailgate and slide the battery pack into the primary shredder,” says the firm, adding that “the lift and dump mechanism is nonconductive since moving an EV battery over metal rollers can cause an electrical-thermal reaction.”
The LithiBatt system uses a three-step shredding process that first reduces individual battery cells to 5/8-inch discharged material “while safely dispersing the stored energy into the system without an effluent,” the company says, adding that the gradual shredding method ensures “that all of the battery cells are fully and effectively cut.”
Following the initial shredding process, EV battery materials are transferred to secondary and tertiary shredders equipped with airlocks and specially designed water-filled augers, BCA Industries says.
In a further secondary stage available, BCA’s Triplus knives are used to achieve a specified final material output and separation of metals, plastics and remnant black mass.
“This patented knife technology is specifically designed for wet battery recycling, ensuring materials are reduced to a consistent and uniform size in a single pass without the need for screening, eliminating concerns about clogging,” the company says of Triplus.
Neuens says the same system also can be used to recycle smaller packs or modules.
The 5/8-inch inert material produced by LithiBatt’s large pack system converts entire EV packs to what BCA calls shippable, manageable, separating out black mass and ferrous materials as well as nonferrous metals such as copper and aluminum.
According to Neuens, the large battery pack reduction system can recover approximately 60 percent of the contained black mass. With additional secondary equipment, that total can be incorporated to achieve a black mass separation rate of up to 95 percent, he says.
Neuens says the closed wet battery recycling system can capture black mass more effectively and with improved purity if properly designed. “All the other particles besides the black mass are very large, so it is relatively easy to filter and press out, dewater and dry. The result is very clean, sellable black mass.”
Get curated news on YOUR industry.
Enter your email to receive our newsletters.
Latest from Recycling Today
- AF&PA report shows decrease in packaging paper shipments
- GreenMantra names new CEO
- Agilyx says Styrenyx technology reduces carbon footprint in styrene production
- SABIC’s Trucircle PE used for greenhouse roofing
- Hydro to add wire rod casthouse in Norway
- Hindalco to invest in copper, aluminum business in India
- Recycled steel price crosses $500 per ton threshold
- Smithers report looks at PCR plastic’s near-term prospects