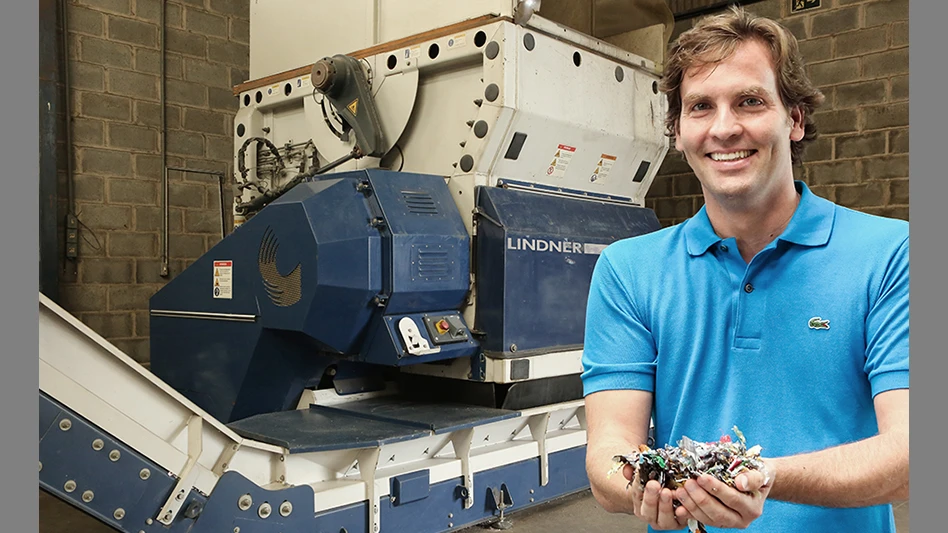
Photo courtesy of Lindner-Recyclingtech GmbH
Brazilian recycling company Grupo Ecological is using two Micromat shredders made by Austria-based Lindner-Recyclingtech GmbH to process polypropylene (PP) plastic scrap for use in the consumer goods packaging sector.
Grupo Ecological, based in Limeira near São Paulo, has two plastic recycling lines dedicated to processing postconsumer and postindustrial bulk bag biaxially oriented polypropylene (BOPP) and postconsumer materials made from BOPP and oriented polypropylene raffia (Rafi-PP) into "high-quality" regranulate.
Two Lindner Micromat shredders and one Lindner Washtech washing line have been deployed to equip a joint project between Grupo Ecological and Unilever.
According to Lindner, the two companies created the first shampoo bottle caps made from 100 percent recycled postconsumer plastics, which has helped global consumer products company Unilever reach its 2025 global sustainability objective ahead of schedule.
Founded in 2012, Grupo Ecological has knowledge and experience acquired from operations of a predecessor company, which had been involved with processing plastics since the 1970s.
“Sustainability has played a prominent role at Grupo Ecological ever since its foundation,” Grupo Ecological founder Fábio Kühl says. “From the outset, our goal was to provide our customers with sustainable and cost-efficient solutions in the area of recycled raw materials, waste management and consultation on matters of sustainability. We are aware of our socioecological responsibility and more than happy to step up to this role.”
The company started a closed-loop program designed to convert postconsumer plastics into marketable secondary resins that can serve companies such as Unilever.
In August 2022, after two years of joint research, Unilever launched the first caps in Brazil made from 100 percent recycled postconsumer material for its Silk and Tresemmé hair care product brands.
The Unilever Rexona, Seda and Comfort hygiene product brands were soon furnished with the same recycled-content caps, keeping 700 metric tons of plastic material in the recycling loop annually.
The effort contributed to Unilever being able to reach its 2025 global objective to use at least 25 percent recycled plastic in its packaging three years earlier than planned.
“Producing recyclate to be used in the cosmetics industry means it requires a high degree of purity, consistent quality as well as it needing to be odorless and virtually neutral in color,” Kühl says.
Kühl and fellow staff members encountered Lindner’s technology at a plastics trade show in Brazil. They then visited facilities and operating lines that used Lindner shredders and washing lines. Subsequent material tests performed using Lindner machinery ultimately resulted in purchasing the first and then second Micromat model 1500 along with the washing components from Lindner Washtech.
By using two Micromat series shredders, the company can process the BOPP and Rafi-PP scrap with a low proportion of fine material, high throughput and few contaminants, according to Lindner, adding that when dealing with heavily contaminated postconsumer plastics, the downstream washing and drying processes are crucial to the quality of the flakes.
“The Micromat series of Lindner shredders represent the key component of our lines and they are pivotal to our production capacity,” Kühl says. “They are extremely reliable, even when handling tough materials, and offer an impressively high, consistent throughput with a screen size that ensures 90 percent of the output is shredded to less than 25 millimeters (1 inch).
“We process up to 800 metric tons of plastic a month, so reliability is of paramount importance. Throughout the years Lindner has been, and continues to be, a reliable partner on our path to success.”
According to Lindner, the collaborative project has meant Unilever could increase the proportion of postconsumer plastics in its packaging in Brazil from 27 percent to 37 percent annually.
“Fabio Kühl and his team have shown with this project that, given the right technology, it is entirely possible to produce high-quality recyclate from postconsumer plastics and for this recyclate to fulfil the strict criteria of the cosmetics and food industry,” Lindner Latin America CEO Frederico Hartmann says.
The caps, having largely been used in Unilever’s Personal Care business group now also are used in the company’s Nutrition division for ketchup bottles.
“We have collaborated with Fabio Kühl for many years and so it is particularly pleasing to see such a positive outcome of this project and that our shredding and washing expertise is used efficiently in connection with the circular economy,” Hartmann says.
Get curated news on YOUR industry.
Enter your email to receive our newsletters.Latest from Recycling Today
- Republic Services, Blue Polymers open Indianapolis recycling complex
- Altilium produces EV battery cells using recycled materials
- Brightmark enters subsidiaries of Indiana recycling facility into Chapter 11
- Freepoint Eco-Systems receives $50M loan for plastics recycling facility
- PET thermoform recycling the focus of new NAPCOR white paper
- Steel Dynamics cites favorable conditions in Q1
- Hydro starts up construction in Spain
- Green Cubes unveils forklift battery line