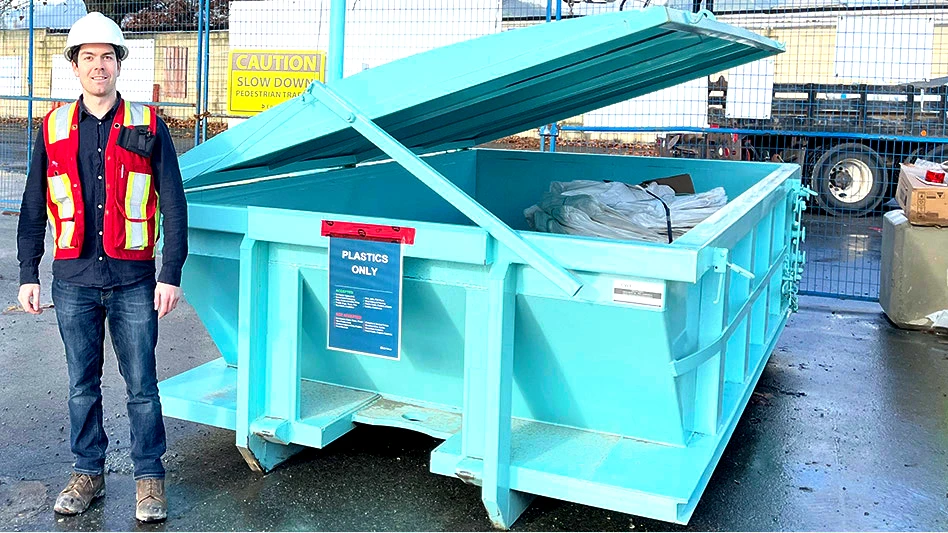
Photo courtesy of Light House Sustainability Society
The Light House Sustainability Society, Vancouver, British Columbia, says it has launched an initiative aimed at diverting and recycling plastic scrap generated at up to 10 Vancouver area construction sites.
The pilot program, known as the Construction Plastics Initiative, is running from late 2024 through February 2026, with Light House saying it “is actively seeking projects to bring on board.”
Light House refers to itself as an organization focused on advancing regenerative and circular practices in the built environment. The organization says the objective of the initiative is to demonstrate the feasibility and financial viability of a circular economic model for discarded plastic materials generated at construction sites.
At job sites, Light House will help collect, separate, measure and process plastics from the selected sites to measure the amount and types of plastic scrap being generated in British Columbia’s construction sector.
Additionally, the group says it intends to “demonstrate circular economic solutions to divert and repurpose the plastic into new products.”
Light House says project participants will be able to showcase their leadership by pioneering plastic diversion and using resulting locally manufactured building products in their projects.
“Currently, there is a lack of comprehensive studies in North America quantifying the volume of construction plastic [material] directed to landfills,” says Gil Yaron, managing director of circular innovation at Light House.
“Studies from Europe suggest approximately 80 percent of plastic [scrap] from onsite construction activities consists of clean packaging materials, which are readily divertible from landfills,” Yaron adds.
“This pilot project aims to provide valuable insights into the extent of construction plastic pollution in North America and to identify opportunities for circular innovation in managing construction plastics,” he continues.
“In Canada right now, virtually all of the plastic generated on these construction sites is ending up in landfill or being buried on site,” Yaron says. “There’s a better solution, and we’re testing it out right now through our Construction Plastics Initiative.
“We’re bringing partners together through the construction plastic value chain, developing a management framework to collect, monitor and track the flow of materials and we’re exploring the business case and sale of derivative building products back into the construction sector,” he adds.
Josephine Kwan, a vice president at participating Vancouver-based contractor Fusion Projects, says, “We believe in creating environments that support the positive aspirations of all people, and sustainability is at the core of everything we do.”
Kwan continues, “By participating in the Construction Plastics Initiative, we are taking meaningful action to reduce our environmental impact while driving innovation within the construction sector. This initiative aligns with our commitment to excellence by providing an opportunity to reduce construction waste, minimize embodied carbon and repurpose plastics into valuable building materials.”
According to Light House, collected plastics from all projects will be sorted by Ocean Park Recycling in Vancouver before being reprocessed into marketable plastic pellets that Light House says “will be integrated into the manufacturing of a range of new building products.”
“The pilot program will help developers and general contractors reduce material use and the embodied carbon associated with their projects,” according to the organization. “Through this initiative, Light House is not only reducing the environmental impact of construction but also preparing the industry for the federal government’s upcoming plastics registry reporting requirements in 2026,” adds Light House.
Sponsored Content
Redefining Wire Processing Standards
In nonferrous wire and cable processing, SWEED balances proven performance with ongoing innovation. From standard systems to tailored solutions, we focus on efficient recovery and practical design. By continually refining our equipment and introducing new technology, we quietly shape the industry—one advancement at a time.
At the Vancouver area project sites, a site monitor will be provided to work with the general contractor and site supervisor to identify the types of plastics to be collected, schedule collections based on the construction timeline, provide size-appropriate collection bins, train work crews on proper source separation practices, monitor bins for contamination and assist with the delivery and removal of collection bins, according to Light House.
“By establishing a comprehensive network between developers, contractors, recyclers and manufacturers, and focusing on upcycling, Light House's innovative project will help address one of our most pressing priorities: reducing waste from the construction and demolition sector,” says Sarah Kirby-Yung, boar chair of Metro Vancouver’s Zero Waste Committee.
“As leaders in waste reduction with one of North America’s best recycling programs, Metro Vancouver recognizes the importance of supporting such initiatives to reduce construction plastic waste,” she adds.
A manufacturer poised to use collected material is Infina Technologies of Delta, British Columbia, Canada. That firm makes InfinaNet, which Light House describes as a voided concrete material designed for floor and wall slabs. Using recycled-content plastic components can allow Infina to use less concrete, reducing CO2 emissions tied to concrete production.
“This innovative design makes installation faster and cheaper, eliminating the need for additional steel cages and individual installation,” says Manveer Pattar, president of Infina Technologies.
Get curated news on YOUR industry.
Enter your email to receive our newsletters.
Latest from Recycling Today
- Enfinite forms Hazardous & Specialty Waste Management Council
- Combined DRS, EPR legislation introduced in Rhode Island
- Eureka Recycling starts up newly upgraded MRF
- Reconomy Close the Gap campaign highlights need for circularity
- Nickel carbonate added to Aqua Metals’ portfolio
- EuRIC, FEAD say End-Of-Life Vehicle Regulation presents opportunity for recyclers
- Recyclers likely to feel effects of US-China trade war
- BCMRC 2025 session preview: Navigating battery recycling legislation and regulations