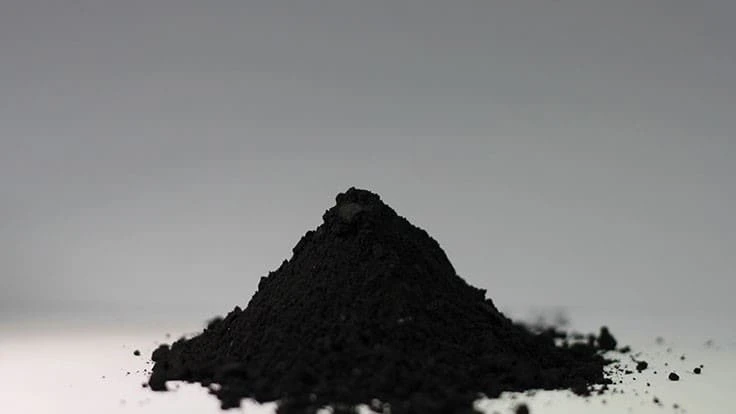
Photo courtesy of Li-Cycle
Lithium-ion battery recycler Li-Cycle, headquartered in Toronto, says it will build its fourth commercial lithium-ion battery recycling facility, selecting Tuscaloosa, Alabama. The site will join the company’s Kingston, Ontario, and Rochester, New York, spokes, which are operational, and its Gilbert, Arizona, spoke, which Li-Cycle says is in “advanced execution stages.”
Li-Cycle says it decided to construct its fourth spoke because the deployment of new battery mega-factories is far exceeding its initial expectations. Supporters of the project include Univar Solutions and their existing automotive customer base; the Alabama Automotive Manufacturers Association (AAMA); the state of Alabama, including the Alabama Department of Commerce; and the Tuscaloosa County Economic Development Authority.
"Our new facility in Alabama positions us well to meet the growing demand for lithium-ion battery recycling,” says Tim Johnston, co-founder and executive chairman of Li-Cycle. “Originally, we had planned on rolling out three commercial Spoke facilities in North America over the next five years, with a total recycling capacity of 20,000 [metric tons] per year. However, demand for lithium-ion battery recycling has continued to outperform our forecasts and we are now forecasting total recycling capacity of 30,000 [metric tons] per year. This facility is essential in filling a recycling gap in the southeastern United States. Like our Arizona Spoke, we expect the new facility to have the capability to process entire vehicle battery packs, without dismantling.”
The company adds that the southeastern United States is becoming a critical region for the lithium-ion battery supply chain as battery manufacturers and automotive original equipment manufacturers establish operations in the region. These facilities will generate significant quantities of battery manufacturing scrap and end-of-life batteries available for recycling, Li-Cycle says. Univar Solutions Inc., headquartered in Downers Grove, Illinois, will be an anchor battery feed supply customer for the Alabama spoke, following Li-Cycle’s previously announced on-site partnership with Univar Solutions to provide waste management solutions for electric vehicle and lithium-ion battery manufacturing.
When completed, Li-Cycle’s Spoke 4 facility will have the capacity to recycle 5,000 metric tons of battery manufacturing scrap and end-of-life batteries annually, bringing its total North American recycling capacity to 25,000 metric tons annually. The company says it is developing the Tuscaloosa site, which is projected to begin operations by mid-2022 and to create roughly 30 new jobs, to accommodate a second 5,000 metric ton processing line in the future. The black mass produced at the company's spokes will be further processed at its first commercial hub in Rochester, where it will use a hydrometallurgical process to recycle the material.
“We have a responsibility to not only manufacture vehicles and batteries but to be good corporate citizens in the choices we make to protect our environment and the community around us,” says Michael Goebel, president and CEO, Mercedes-Benz US International Inc. (MBUSI), which is working together with Univar Solutions on end-of-life solutions for lithium-ion batteries. “We welcome the partnership between Univar Solutions and Li-Cycle and the strong commitment of our partners here in Tuscaloosa, Alabama, to push a sustainable future for mobility.”
"At Univar Solutions, we’re committed to bringing more sustainable solutions for a better world, leveraging our expertise to help our customers and suppliers make progress toward their sustainability goals,” Stephen Molica, vice president of services for Univar Solutions, says. “We are thrilled to work together with industry leaders like Li-Cycle and MBUSI to make a difference in lithium-ion battery recycling. We look forward to further assisting MBUSI with best-in-class sustainability solutions through our OnSite Services team, including supporting the addition of Li-Cycle’s new facility in Alabama."
Ron Davis, president of the AAMA, says, “Li-Cycle’s decision to locate in Alabama helps position our state on the leading edge as our industry enters the era of electric vehicle production. With its innovative technology and process, Li-Cycle is bringing a capability that will offer the auto industry a solution to what will become an issue of critical importance. I am very excited to see Li-Cycle's ground-breaking contributions to our growing Alabama automotive industry."
“With the popularity of electric vehicles accelerating, it’s critical that old batteries are recycled—and Li-Cycle’s technologies make that possible,” Alabama Gov. Kay Ivey says. “Li-Cycle’s selection of Tuscaloosa for its network of recycling facilities means not only jobs in Alabama, but also a positive for the environment.”
Greg Canfield, secretary of the Alabama Department of Commerce, adds, “With EV production set to start in Alabama in 2022, Li-Cycle’s Tuscaloosa recycling facility will ensure that Alabama plays another important role in the lifecycle of the batteries powering electric vehicles. This project addresses the battery repurposing proposition that must also be a part of the sustainability solution that EVs offer.”
“With a strategic focus on mobility and power, west Alabama is a prime location for Li-Cycle’s spoke facility,” Danielle Winningham, executive director for Tuscaloosa County Economic Development Authority, says. “We welcome Li-Cycle’s sustainable and environmentally friendly end-of-life solution for lithium-ion batteries, which assists [in] meeting the demand for electric vehicle battery materials.”
Latest from Recycling Today
- EPA releases ‘National Strategy to Prevent Plastic Pollution’
- South Carolina launches recycling app
- Resource Recycling Systems transitions to employee ownership model, refreshes branding
- APR upgrades PCR certification program
- WM completes $40M automation project at Philadelphia MRF
- Speira commissions new furnace in Germany
- ABB report portrays paper sector circularity, emissions reduction
- RMDAS and Davis Index numbers portray stalled ferrous market