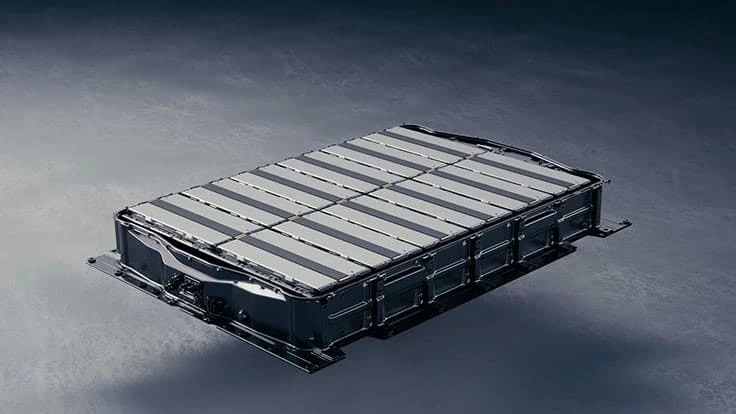
Photo courtesy of Ultium Cells LLC
Ultium Cells LLC, a joint venture between Detroit-based General Motors and LG Energy Solution, headquartered in South Korea, has announced an agreement with Toronto-based Li-Cycle to recycle up to 100 percent of the scrap generated from battery cell manufacturing.
The new recycling process will allow Ultium Cells to recycle battery materials, including cobalt, nickel, lithium, graphite, copper, manganese and aluminum. Ninety-five percent of these materials can be used in the production of new batteries or for adjacent industries, according to a news release issued by GM.
"Our combined efforts with Ultium Cells will be instrumental in redirecting battery manufacturing scrap from landfills and returning a substantial amount of valuable battery-grade materials back into the battery supply chain," says Ajay Kochhar, Li-Cycle president, CEO and co-founder. "This partnership is a critical step forward in advancing our proven lithium-ion resource recovery technology as a more sustainable alternative to mining."
Li-Cycle takes a hub-and-spoke approach to lithium-ion battery recycling, with existing spokes in Rochester, New York, and Kingston, Ontario. The company is developing its hub in Rochester, where it will use a hydrometallurgical process to recycle the black mass produced at its spokes. Li-Cycle says its technology produces 30 percent less greenhouse gases than traditional processes, helping to minimize environmental impact. It plans to construct 20 spoke facilities globally over the next five years and recently announced the construction of its third spoke in Gilbert, Arizona, within the Phoenix Metro area. It will be able to process up to 10,000 metric tons of end-of-life batteries and battery manufacturing scrap annually, bringing Li-Cycle’s total recycling capacity to 20,000 metric tons per year, the company says.
"GM's zero-waste initiative aims to divert more than 90 percent of its manufacturing waste from landfills and incineration globally by 2025," says Ken Morris, vice president of electric and autonomous vehicles at GM. "Now, we're going to work closely with Ultium Cells and Li-Cycle to help the industry get even better use out of the materials."
Since 2013, GM says it has recycled or reused 100 percent of the battery packs received from customers, including any packs replaced through warranty service. Most current GM electric vehicles (EVs) are repaired with refurbished packs.
Ultium says its batteries will feature a modular design, making them easy to reuse or recycle.
"We strive to make more with less waste and energy expended," says Thomas Gallagher, chief operating officer of Ultium Cells LLC, Lordstown, Ohio. "This is a crucial step in improving the sustainability of our components and manufacturing processes."
Ultium Cells LLC and Li-Cycle say they will begin the new scrap recycling process later this year.
GM and LG Energy Solution also have announced that they will invest more than $2.3 billion to build a second battery cell manufacturing plant that will be in Spring Hill, Tennessee. The 2.8-million-square-foot facility is being built on land Ultium is leasing from GM. It is scheduled to open in late 2023. Once operational, the facility will supply battery cells to GM’s Spring Hill assembly plant.
Ultium Cells' plant in Lordstown equals the size of 30 football fields and will have an annual capacity of more than 30 gigawatt-hours with room to expand once operational.
Latest from Recycling Today
- Lautenbach Recycling names business development manager
- Sebright Products partners with German waste management equipment company
- WasteExpo transitions to biennial format for enhanced experiences
- Study highlights progress, challenges in meeting PCR goals for packaging
- Washington legislature passes EPR bill
- PureCycle makes progress on use of PureFive resin in film trials
- New copper alloy achieves unprecedented high-temperature performance
- Gränges boosts profits and sales volume in Q1 2025