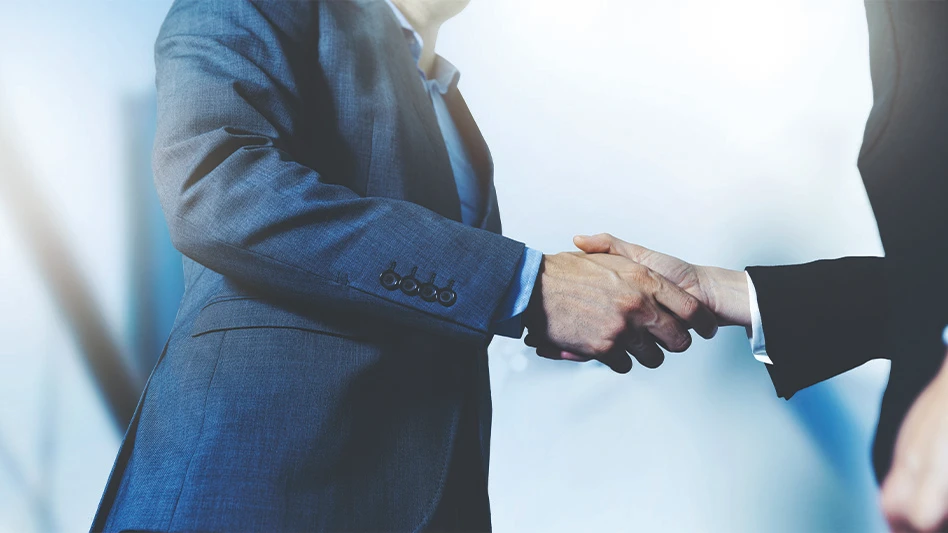
ronstik | stock.adobe.com
Toronto-based lithium-ion battery (LIB) recycler Li-Cycle Holdings Corp. has entered a partnership with Portland, Oregon-based Daimler Truck North America (DTNA) to help the automaker integrate a comprehensive circular economy approach across its operations and reduce its carbon footprint.
Under the partnership, Li-Cycle will recycle LIBs from DTNA electric vehicles (EVs) that reach the end of their life cycle. Recycling LIBs is part of DTNA’s plans to maximize battery lifespans and reduce scrap to tackle global sustainability challenges. The company’s strategy emphasizes repairing, remanufacturing, repurposing and recycling LIB materials.
“We are proud to partner with companies such as DTNA to support their sustainability and carbon reduction goals,” Li-Cycle President and CEO Ajay Kochhar says. “Our environmentally friendly and safe recycling technologies can recover critical materials to help create a domestic closed-loop battery supply chain, giving new life to these battery materials and helping power the world’s transition to clean energy.”
In a news release outlining its sustainability strategy for batteries, DTNA says that by leveraging advanced technology, it can discern when a LIB no longer meets its standards required for vehicle use, and that insight guides the decision on the optimal process to maximize materials for a second life, with repair taking precedence whenever possible.
While batteries receive significant attention because of their use of metals like cobalt and nickel, DTNA says, its approach extends to all components of the EV product.
“As part of our commitment to maximizing material life cycles, we meticulously assess environmental and ethical implications from sourcing to post-production,” says Rakesh Aneja, vice president and chief of the Zero-Emission Transformation Group at DTNA. “Our primary goal is to repair our lithium-ion battery materials and reduce the consumption of new resources.”
When a battery or EV component is beyond repair, it enters the remanufacturing process at existing Detroit Diesel Remanufacturing locations across the United States, DTNA says. This process involves partial disassembly, module replacement and rigorous testing for optimized reliability. All remanufactured products are updated with the latest technology and must meet or exceed new product standards to be reintroduced to the market.
For repurposing batteries, DTNA has partnered with Sunnyvale, California-based Nuvation Energy to pilot a battery energy storage system (BESS) designed to assist in charging, peak shaving, backup storage and microgrid scenarios, allowing DTNA to repurpose batteries that cannot be reused in a vehicle.
For recycling batteries, DTNA cites Li-Cycle’s process that recycles batteries within a liquid-based solution, achieving up to a 95 percent recovery rate for returning critical materials back to the battery supply chain while producing minimal water discharge.
“This circular approach extends beyond just batteries,” Aneja says. “We are actively working to apply this concept to other facets of our product development, aiming to increase our utilization of reusable or recyclable materials. Our goal is to continue contributing positively to the preservation of our planet for future generations.”
In line with its sustainability goals, DTNA says it aims to achieve carbon neutrality for all new products and services from direct suppliers in Europe, the U.S. and Japan by 2039. DTNA says it also plans to achieve carbon neutral production at all its remaining truck manufacturing plants by 2025.
Latest from Recycling Today
- Biden officially blocks Nippon Steel’s acquisition of US Steel
- Highland Sanitation awarded solid waste and recycling contract in Wanamingo, Minnesota
- Ecobat gathers support for California permit renewal
- RecyclX platform designed to provide materials transparency
- Turkish mills sampled wide scrap market in 2024
- GLE Scrap Metal acquires interest in Mallin Cos.
- 2024 marks strong year for Van Dyk
- Recycled metal portrayed as former dictator’s fiefdom