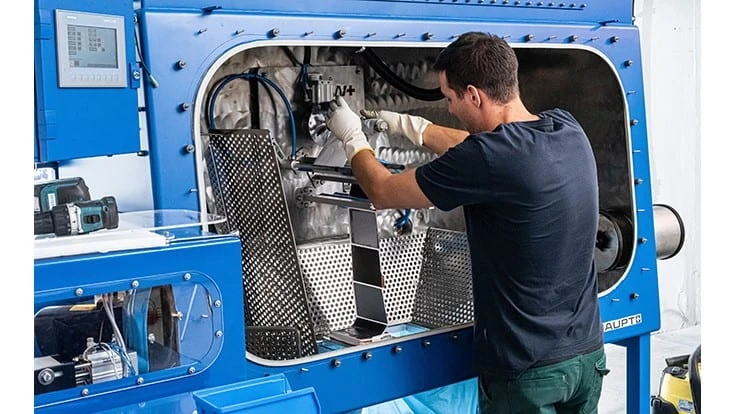
Photo provided by Kyburz Switzerland AG.
Switzerland-based electric vehicle (EV) manufacturer Kyburz has cooperated with a federal laboratory and a university to create what it calls an in-house system to recycle the lithium-ion batteries it uses in its EVs. The plant in Freienstein, Switzerland, went into operation on Sept. 4, using a recycling process Kyburz says enables up to 95 percent of contained metals in batteries to be recovered.
Kyburz says the recycling process it developed in collaboration with the Eidgenössische Materialprüfungs- und Forschungsanstalt (EMPA) institute and the Zurich University of Applied Sciences (ZHAW) is “environmentally friendly and offers potential beyond our own production.”
Three-wheel scooters from Kyburz are in use around the world, says the firm, including by Swiss Post. Before the Freienstein plant opened, Kyburz used an external recycling process through which batteries were shredded and then either melted down or treated with chemicals. The company says it began looking for an alternative.
“Our goal was to develop a recycling process that is efficient, environmentally friendly and safe,” says Olivier Groux, who became responsible for the project. As part of his bachelor’s degree in environmental engineering at ZHAW, Groux had been studying ways to sustainably recycle lithium-ion batteries. “I thought to myself: If batteries are assembled from different materials, it must be possible to separate them again.”
Groux performed research for his bachelor thesis and developed a process for lithium iron phosphate (LFP or LiFePO4) batteries to be recycled through what he calls “optimal discharging, careful cell dismantling and purification with water,” without the use of chemicals.
In the first stage, the LiFePO4 batteries are discharged to 2.5 volts and broken down into their individual components. The cathodes and anodes are then treated with water to separate the aluminum and copper foils. Lithium salt is obtained from the electrolytes in a distillation process, and the carbonates that are distilled out are reused in the recycling process. The anodes are additionally treated with heat in order to decompose the binding materials.
The EV producer’s Managing Director Martin Kyburz was won over by the idea, and so hired Groux. “We attach great importance to sustainability and are looking for ways in which we can implement the ideas of the circular economy in our company,” says Kyburz. “An in-house facility for recycling our batteries is a big step in this direction.”
Groux says he further developed the in-house recycling system in close collaboration with Marcel Gauch, Lorena Toledo and Rolf Widmer from EMPA St. Gallen. The team summarized findings from the project in a research paper that subsequently was awarded first prize at a World Resources Forum.
The long-term goal is a production facility that can break down all LiFePO4 batteries Kyburz has ever installed back into their raw materials. In the first expansion stage, around 4,000 cells are to be processed per year. When completed, the system will have a capacity of up to 24,000 cells per year, which corresponds to the annual production of 3,000 vehicles, according to Kyburz.
Kyburz Switzerland AG, which was founded in 1991 by Martin Kyburz, develops and produces electric vehicles for delivery and industrial companies and for private individuals. More than 22,000 Kyburz vehicles have been produced by the company’s more than 150 employees.
Latest from Recycling Today
- Aqua Metals secures $1.5M loan, reports operational strides
- AF&PA urges veto of NY bill
- Aluminum Association includes recycling among 2025 policy priorities
- AISI applauds waterways spending bill
- Lux Research questions hydrogen’s transportation role
- Sonoco selling thermoformed, flexible packaging business to Toppan for $1.8B
- ReMA offers Superfund informational reports
- Hyster-Yale commits to US production