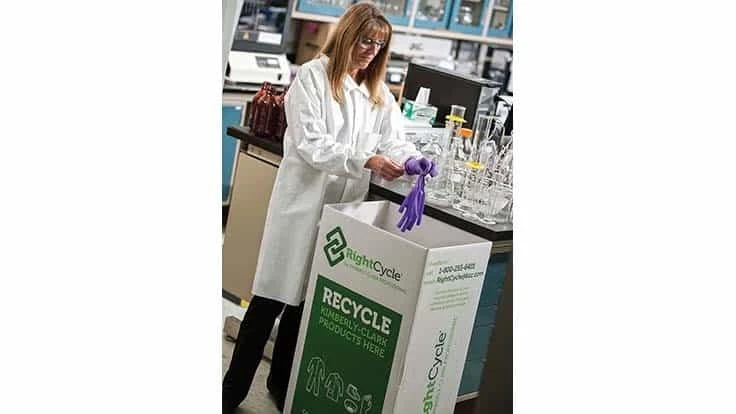
Photo provided by Kimberly-Clark and BCW.
The COVID-19 epidemic has brought about a greatly increased use in personal protective equipment (PPE), including face masks and gloves designed to prevent the spread of the virus.
Recycling discarded PPE may not have been the first thing large-scale users of PPE worried about, but thought and effort was already going into how to recycle rather than discard some of this material.
Global hygiene products manufacturer Kimberly-Clark Professional introduced its RightCycle program in 2011 to collect used PPE and find recycling destinations for the considerable volumes of this material already being generated.
Recently, Recycling Today Media Group Senior Editor Brian Taylor had the opportunity to ask Mayur Valanju, a vice president of product development and innovation with Kimberly-Clark Professional, about the program’s introduction and scale.
Recycling Today (RT): What types of PPE or lab accessories are being collected through RightCycle?
Mayur Valanju (MV): The RightCycle program collects used PPE such as protective clothing, nitrile gloves and safety glasses. Originating in the U.S. at a few scientific manufacturing locations, the program is now available in nine countries in Europe and North America across a variety of industries, including laboratories, food processing, zoos, universities and pharmaceutical and electronics manufacturing locations.
For detailed information on the eligible products list in each of the three categories, readers can refer to this web page or this video.
RT: Which resins do these materials tend to be made of, and what kind of (resin) pellets are being produced?
MV: The materials are made of the following: apparel, polypropylene (PP); safety glasses, polycarbonate (PC); and gloves, acrylonitrile.
The used PPE is processed and densified into pellet form, which is then sold to manufacturers of consumer goods who use these pellets to produce new plastic-based products. The recycling processes for apparel, safety glasses and nitrile yield primarily PP, PC and nitrile materials that are then blended into custom resins.
The recycled pellets go into durable consumer goods such as shelving, totes, and garden furniture.
We’re proud to contribute to the circular economy by creating a solution for these previously hard-to-recycle items to be used in new products. As supply chain technologies continue to evolve, we can hopefully one day include these recycled resins back into new PPE products. The performance and regulatory requirements limit us today, but we are hopeful for continued innovation.
RT: Does Kimberly-Clark see this program as continuing into the decade, beyond any pandemic measures that may at some point be phased out?
MV: Since the onset of the COVID-19 pandemic, PPE usage has increased dramatically, leading to higher levels of PPE waste in the environment. According to UN News in September 2020, 75 percent of used masks are likely to end up in landfills or seas. Even in 2020, as many facilities closed, RightCycle enrolled 82 new customers globally, showing that sustainability goals are as important now as ever.
Momentum continues to build year after year of the program, expanding to new markets as capability and demand grew for this unique solution. The RightCycle program is celebrating its 10th anniversary this year, and since 2011, over 800 customers have diverted more than 1,400 metric tons of waste.
Active programs are currently in place in North America and Europe, and we plan on continuing this successful program. Just in 2020, over 300 facilities participated in The RightCycle program, capturing and recycling 678,072 pounds (nearly 340 tons) of PPE waste.
PPE is a daily requirement in workplaces across the globe, protecting workers from potential hazards or, providing a barrier between workers and the ‘clean’ process, such as in cleanrooms. Much PPE is designed for limited or single use and is made of plastic. While serving a critical role, tension can be created in organizations with waste reduction goals, especially for plastic. The RightCycle program meets this critical need for customers. In fact, nearly 60 percent of the lifetime total of recycled PPE occurred in the last three years, from 2018 to 2020.
Beyond circularity benefits, the program also makes a difference in the lives of people with disabilities through its partnership with a recycling organization that provides employment for people who have survived traumatic brain injuries or have been diagnosed with autism spectrum disorders, learning disabilities and other conditions. These workers sort and prepare used PPE prior to its recycling.
RT: To what extent has the RightCycle program been financially viable as a way to divert and recycle materials that used to meet with a disposal outcome?
MV: We consider it an investment to support our own sustainability goals as well as our customers’ goals. Companies who are investing in programs to divert waste from landfills see the RightCycle program as worth investing in to achieve these goals.
From a business perspective, this deepens the partnership between Kimberly-Clark Professional and customers, as those who use RightCycle represent some of our longest standing relationships. The recycler benefits from an increased amount of clean, high-quality resins/polymers being put into the supply chain.
Kimberly-Clark’s strategic 2030 ambition is to make lives better through purpose-driven brands with a goal to advance well-being of 1 billion people through innovation and programs that deliver essentials to underserved communities while reducing our environmental footprint by 50 percent. This program delivers on two of these pillars, Social Impact and Plastics Footprint.Latest from Recycling Today
- Green Cubes unveils forklift battery line
- Rebar association points to trade turmoil
- LumiCup offers single-use plastic alternative
- European project yields recycled-content ABS
- ICM to host colocated events in Shanghai
- Astera runs into NIMBY concerns in Colorado
- ReMA opposes European efforts seeking export restrictions for recyclables
- Fresh Perspective: Raj Bagaria