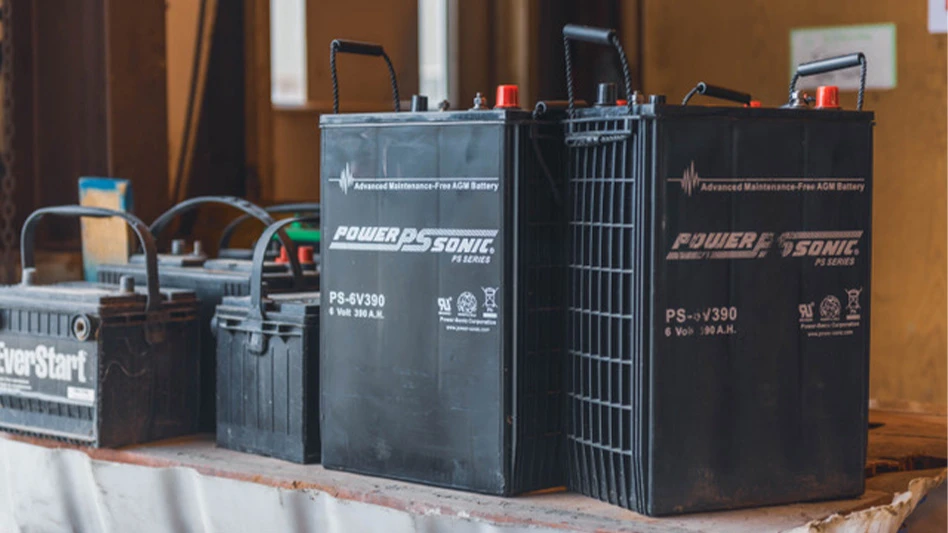
Photo courtesy of KC Recycling
Lead battery recycler KC Recycling is expanding its polypropylene (PP) plant in its hometown of Trail, British Columbia, with the help of $1.2 million from the CleanBC Plastics Action Fund.
The company plans to use the investment in part to increase its ability to accept additional plastics, which it says will increase the volume of high-quality plastic resin it produces by 1,000 metric tons annually.
The project, which KC Recycling says will total around $2 million, also will streamline operations, including bulk material handling processes, and implement a contamination reduction system that will result in its plastic meeting “the most stringent quality standards.”
“This project will ensure our recycled plastic can be used as the resin for many, many more products, as resin quality can limit the applications for certain industrial products,” KC Recycling CEO Pete Stamper says. “Plus, improving and expanding plastic recycling isn’t just good for the environment—it’s a critical investment in our economy.”
RELATED: KC Recycling, East Penn Manufacturing form partnership
According to KC Recycling, lead batteries are the most recycled consumer product in North America, with more than 99 percent of the lead recovered and recycled.
KC Recycling processes plastic from end-of-life lead battery casings to produce recycled PP pellets and closes the loop by supplying that recycled plastic resin to manufacturers across North America to produce battery cases, paint buckets, plastic liners and more.
After the expansion project is complete, the company says it will utilize a new bulk material handling system, allowing it to serve suppliers and customers with bulk shipments via rail or truck. Notably, KC Recycling says, this system will open the door to accepting feedstock from other battery recyclers that cannot produce resin.
“KC Recycling plays a key role in the success of Metal Tech Alley establishing this region as a battery hub for Western Canada,” says Jacomien van Tonder, director of Metal Tech Alley, a group of industry professionals that works to adopt best practices and lead in the global industrial circular economy movement. “KC Recycling will be a part of the R&D facility on the plastics side. That is where this funding will be of great importance.”
In 2021, KC Recycling was awarded $852,000 from CleanBC Plastics Action Fund to jumpstart the project, adding its PP extruding operations.
“The Pacific Northwest is an underserved region for car battery recycling in the sense that there is not enough local recycling capacity, which results in higher export-rates for scrap batteries than in other regions,” KC Recycling operating partner and Director of Business Development Dan Di Filippo said at that time. “Hopefully, this improved closed-loop system will provide further incentive to recycle product domestically in North America; more product means more jobs as well as economic growth for the region. All-in-all there’s a good knock-on effect.”
Latest from Recycling Today
- Aqua Metals secures $1.5M loan, reports operational strides
- AF&PA urges veto of NY bill
- Aluminum Association includes recycling among 2025 policy priorities
- AISI applauds waterways spending bill
- Lux Research questions hydrogen’s transportation role
- Sonoco selling thermoformed, flexible packaging business to Toppan for $1.8B
- ReMA offers Superfund informational reports
- Hyster-Yale commits to US production