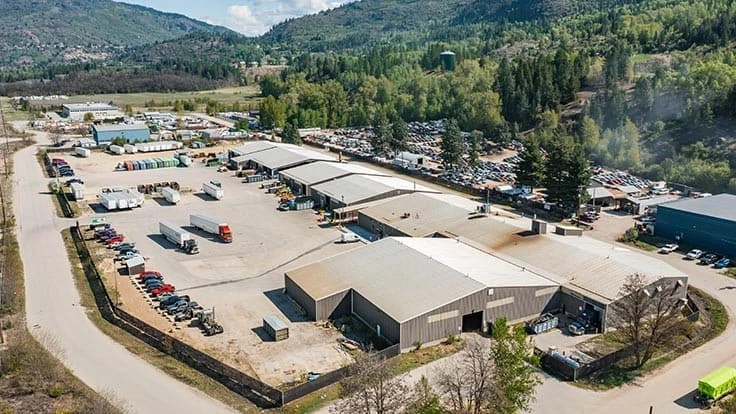
Photo courtesy of KC Recycling
KC Recycling Ltd. has been awarded $852,000 from the CleanBC Plastics Action Fund to jumpstart a $1.2 million plant upgrade, which will create a circular solution to recycle the plastic cases on car batteries already processed at the operation in Trail, British Columbia.
According to a news release from KC Recycling, the company is renovating its facility to create a polypropylene (PP) extruding operation. The company says the operation will help to stimulate economic growth for the region.
“We’re thrilled our project meets the CleanBC Plastics Action Fund criteria to increase domestic recycling capacity as Canada makes changes to keep plastics out of the ocean and comply with the global Basel Convention,” says Pete Stamper, KC Recycling’s CEO. “The whole KC Recycling team is proud we’re expanding operations to enable production of finished recycled plastic and providing a real circular economy solution right here in the Kootenays. It aligns with our mission of preserving a sustainable world for future generations.”
KC Recycling says its expansion will “strengthen the region’s economy with the addition of five positions as the new facility comes online.” The plant will continue to recycle cathode-ray tube (CRT) glass from old televisions and monitors and electronic scrap while growing its car battery recycling operation with the addition of in-house plastic recycling.
“For every automotive battery processed at our facility, 4.5 percent of the inbound weight is composed of high-quality polypropylene plastic," says Dan Di Filippo, KC Recycling operating partner and director of business development. “With an annual automotive battery process rate of approximately 80 million pounds, we generate about 3.6 million pounds of regrind polypropylene plastic per year."
This unfinished plastic regrind is currently exported to PP compounders, where it is pelletized into product specifications that meet manufacturers’ requirements. KC Recycling says its new plant will localize this last step with an on-site washing, extrusion and pelletizing lab. KC Recycling will test the refined material to ensure it meets specs before shipping it to battery manufacturers where it is an input for new batteries.
“The Pacific Northwest is an underserved region for car battery recycling in the sense that there is not enough local recycling capacity, which results in higher export-rates for scrap batteries than in other regions,” Di Filippo says. “Hopefully, this improved closed-loop system will provide further incentive to recycle product domestically in North America; more product means more jobs as well as economic growth for the region. All-in-all there’s a good knock-on effect.”
Administered by the Alacrity Canada Cleantech Program in partnership with the British Columbian government, the CleanBC Plastics Action Fund seeks to bolster the region’s circular economy by reducing virgin plastics and making better use of postconsumer recycled plastic in manufacturing processes. KC Recycling serves as an ambassador for cleantech as they work toward economic recovery and resilience. With initial rollout focused on plastic car battery casings, the new polypropylene extruding operation also looks to accommodate other postconsumer plastic streams.
Latest from Recycling Today
- AF&PA report shows decrease in packaging paper shipments
- GreenMantra names new CEO
- Agilyx says Styrenyx technology reduces carbon footprint in styrene production
- SABIC’s Trucircle PE used for greenhouse roofing
- Hydro to add wire rod casthouse in Norway
- Hindalco to invest in copper, aluminum business in India
- Recycled steel price crosses $500 per ton threshold
- Smithers report looks at PCR plastic’s near-term prospects