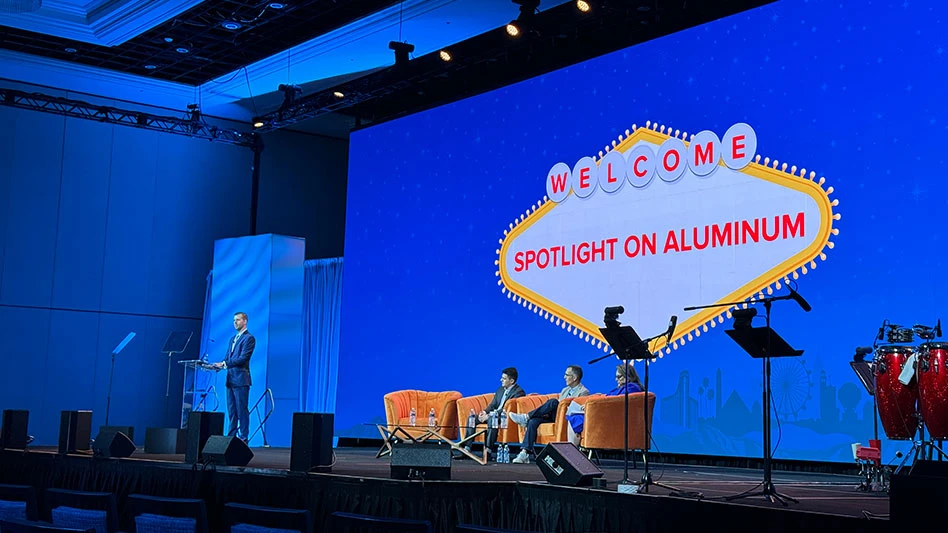
Photo by DeAnne Toto
Aluminum is used in a variety of markets that include transportation, packaging, constriction and electrical. Despite that diversity of use, 2023 saw aluminum demand contract further after peaking in 2021.
Ibrahim Yucel, a principal consultant with CRU Group who is based out of the Pittsburgh area, told attendees at the Spotlight on Aluminum session during the Institute of Scrap Recycling Industries (now the Recycled Materials Association) 2024 Convention and Exposition, ISRI2024, aluminum demand in many markets will begin to increase staring in 2026.
“You already see a rebound in the aluminum market when it comes to the transportation end user, and that is associated with increased automotive assembly,” he said. “We see that picking up both due to more vehicles being produced and to increased aluminum penetration across the board.”
CRU expects canstock demand to be relatively weaker in 2024 and 2025 before picking up.
“When it comes to demand, we are not currently at levels that we saw in 2021 and 2022, but we are slowly rebounding to matching that level and then due to aluminum’s favorable uses both in terms of electrification as well as substitution away from copper, for example, as well as substitution away from steel in transportation markets, we see that there is going to be a relative increase in overall demand moving forward,” Yucel said.
He noted aluminum production capacity in the U.S. will increase significantly through 2028, with capacity also growing in Mexico. Cansheet will see the most growth followed by autobody sheet, though building sheet and foil also will grow. This growth in domestic production capacity will lead to a relative reduction in import requirements, he said, but ongoing trade restrictions related to Section 232 and anti-dumping and countervailing tariffs also will play a role as.
Yucel then shared a map of more than a dozen new aluminum recycling investments that have been announced in North America, noting that it did not include all such announcements. “In every single one of these new capacity expansions in aluminum, they are going to be using significant volumes of scrap,” he said. “With this, we are looking at more than 2 million tons in remelt or scrap intensive capacity.”
These new facilities as well as existing ones will look to maximize new scrap use and to use incrementally more old scrap through the close of this decade.
By 2034, Yucel said, the cansheet market in North America is forecast to consume 750,000 more tons of postconsumer scrap than it does today, while bodysheet producers are making a concerted effort to increase their use of postconsumer material as well.
Regarding the availability of sufficient quantities of recycled material of the quality needed to feed new and existing aluminum production capacity, he said companies will have to optimize their use of preconsumer scrap—process scrap generated by can makers or the auto industry, for instance—or maximize postconsumer scrap use by increasing its quality or both. When it comes to preconsumer scrap, however, Yucel said most of this material already is accounted for.
However, preconsumer material generally does not hold as much decarbonization potential as postconsumer aluminum, and as customers start asking their suppliers for information for their Scope 3 reporting, they will be more interested in the proportions of pre and postconsumer recycled aluminum in products.
Maximizing the use of postconsumer scrap hinges on the ability to sort to a higher purity or breakthroughs in melting technology, and that may not be commercially viable by 2030, Yucel said.
However, while the technology exists to sort this material by alloy today, other market conditions such as the supply of the material and the demand pull from the customer are coming together to make the commercialization of alloy sortation more viable.
“Collection and processing in the future might need to become more binary,” Yucel said, even for postconsumer scrap.
In a market where supply might be constrained in terms of the types of materials the rolling mills want, he said, we will see more vertical integration as we’ve seen in steel.
“One of the key wildcards in the supply chain market balance is going to be zorba and twitch,” Yucel added, which are mixed aluminum grades. “Based on my analysis, I do see a significant supply surplus of this material that will occur over the next few years” unless technology is developed to sort this material for use in rolled products.
The wrought alloy content in this material will rise significantly as aluminum-intensive vehicles reach end of life.
Twitch, which accounts for 10 percent of the total input into an auto shredder, he said, could increase to up to 20 percent in next few years.
Yucel was joined during the session by Mary Hlepas, vice president of purchasing at Chicago-based Imperial Group, and Joe Tomoro, a trader with Sims Alumisource, based in Pennsylvania, who shared their perspectives on the industry, including their takes on the prospect of consolidation.
Tomoro said the industry remains very fragmented with plenty of competition, while Hlepas said consolidation could reduce competition, leading to more control over pricing and potentially decreasing innovation.
Regarding the prospect of vertical integration, Hlepas said she doesn't feel as if it is a trend.
Tomolo said such maneuvers are "all about the metal." He added that companies could take different approaches to realize that same result, whether they be strategic partnerships or acquisitions.
Latest from Recycling Today
- Analyst: Scrap imbalance lost amid copper’s critical status
- AF&PA report shows decrease in packaging paper shipments
- GreenMantra names new CEO
- Agilyx says Styrenyx technology reduces carbon footprint in styrene production
- SABIC’s Trucircle PE used for greenhouse roofing
- Hydro to add wire rod casthouse in Norway
- Hindalco to invest in copper, aluminum business in India
- Recycled steel price crosses $500 per ton threshold