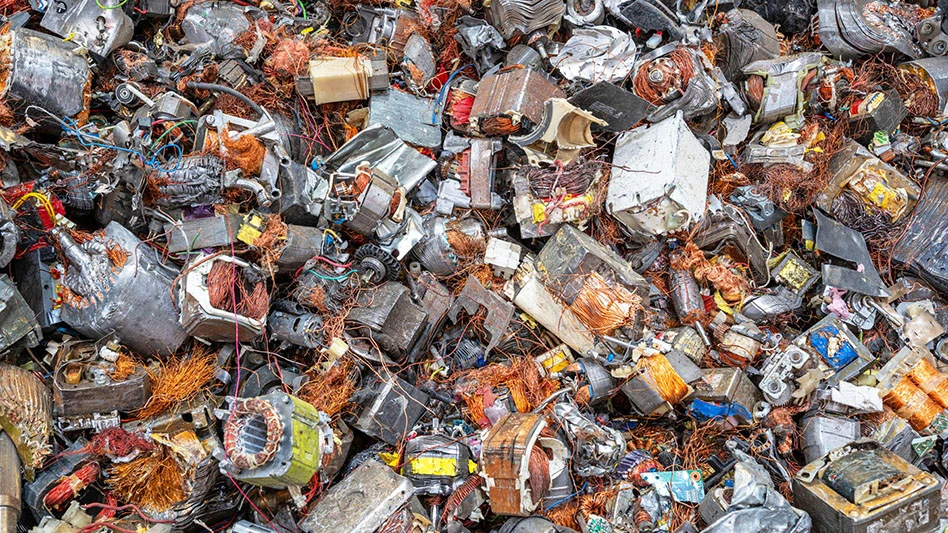
Photo courtesy of Stadler Anlagenbau GmbH
Germany-based sorting and recycling equipment provider Stadler Anlagenbau GmbH has completed a project along with fellow Stadler Group company weeeSwiss Technology AG to design and install an electronic scrap sorting plant with and for Immark AG in Regensdorf, Switzerland.
The new facility replaces an existing plant, increasing the site’s processing capacity “while ensuring consistent standout quality in its output,” Stadler says.
Immark AG, part of the Switzerland-based Thommen Group, is an electronic scrap recycler in Switzerland, a nation with a recycling rate of up to 95 percent, which “far exceeds the requirements of the European Waste Electrical and Electronic Equipment Directive (WEEE),” Stadler says.
The company chose Stadler to design and install a new sorting plant to replace its existing facility in Regensdorf. “It is the largest processing plant for electronic [scrap] in Switzerland, and it must ensure high throughput and capability to process the volumes we receive,” says Patrick Wollenmann, a project manager at Immark.
Stadler says the new facility is the first e-scrap sorting plant to use a ballistic separator. The plant operates in two shifts with a capacity of up to 12 tons per hour and also seeks to optimize the recovery of printed circuit boards, (PCBs).
“For us, Stadler’s convincing technology of the conveyor belts and ballistic separator, and their proximity to Zurich were decisive,” Wollenmann says. “We also appreciate very much the work of the competent project managers, the quick and constructive implementation and solution-oriented approach.”
“The Stadler STT5000 ballistic separator pre-sorts the material into three different fractions,” says Jan Dollenmaier, project manager at Stadler. “It separates the material into fines, flat plastics and cables, as well a cube-shaped material such as electronic motors.”
The sorting plant takes in large and small household appliances, IT equipment and consumer electronics that in the Stadler system are processed in several different processing modules. Leaving the plant are nonferrous, ferrous, PCBs, stainless steel and plastic fractions.
The first module of the process involves manually sorting to remove items identified as having toxins and hazardous components, as well as materials such as cables, PCBs and metals.
Remaining items and components are then shredded so that both the remaining hazardous components, such as batteries or capacitors, and the various recyclables, such as iron, nonferrous metals and plastic, can be sorted.
Recyclables are sorted out using magnetic technology, eddy current separation and sensor sorting technology. The iron fractions are resorted in a sorting cabin to ensure quality and increase the degree of purity, Stadler says.
The fine fraction also goes through various sorting steps to separate the plastics from the metals, with the latter then ground to separate the various metal granules.
Automated fire detection and extinguishing systems were installed after the shredding units, with a detected fire source automatically discharged from the plant process into a steel bunker via a hatch system, where workers can extinguish the fire.
Stadler says the plant was designed to simplify maintenance as much as possible. “All key points and motors are accessible via maintenance platforms or access ladders,” the firm says.
The design and assembly of the new plant was coordinated to minimize disruptions. “In addition to the installation of the new system, the old system continued to operate,” Wollenmann says. “This meant that the new plant had to be built in several stages and the old plant had to be dismantled at the same time. In addition, the available space on the construction site was very limited.”
The modular design of the new plant was a key element for the successful completion of the project and for the high speed of assembly, according to Stadler. “The modular design of the individual units has limited the assembly time to a very short period,” Wollenmann says.
“This was a major electrical [scrap] project, with many new machines being installed and many suppliers involved,” Stadler project manager Philipp Frechen adds. “We had a lot of new interfaces. All in all, we managed everything very nicely in cooperation with Immark’s team.”
Latest from Recycling Today
- Green Cubes unveils forklift battery line
- Rebar association points to trade turmoil
- LumiCup offers single-use plastic alternative
- European project yields recycled-content ABS
- ICM to host colocated events in Shanghai
- Astera runs into NIMBY concerns in Colorado
- ReMA opposes European efforts seeking export restrictions for recyclables
- Fresh Perspective: Raj Bagaria