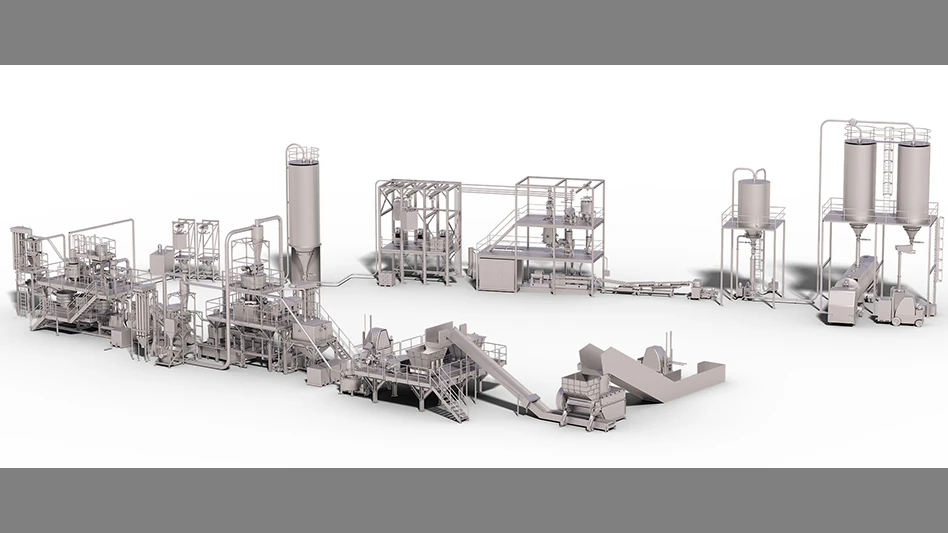
Rendering courtesy of Hillenbrand, Coperion and Herbold Meckesheim
Germany-based recycling equipment and technology vendors Coperion and Herbold Meckesheim are collaborating with India-based preform and plastic packaging manufacturer Magpet Polymer Pvt. Ltd. to build a polyethylene terephthalate (PET) bottle-to-bottle recycling facility.
The recycling system being installed encompasses all process steps leading up to extrusion with a ZSK twin screw extruder, including pelletizing and an SSP (solid state polycondensation) reactor.
The PET bottle recycling system is designed for a throughput of 5,500 kilograms (12,125 pounds) per hour and it will deliver recycled-content PET that is approved by the European Food Safety Administration (EFSA) and the United States Food and Drug Administration (FDA) for direct contact with food. The PET pellets also will be brand owner approved, according to the companies.
“Magpet has always pursued the goal to be a first mover when it comes to embracing new technology,” says Devendra Surana, managing director of Magpet, which is a part of the Kolkata, Incia-based Magnum Group. “This PET recycling unit [goes] hand in hand with our efforts to take over business responsibly for a bigger eco purpose. We are excited to partner with Herbold and Coperion to set up this state-of-the-art PET bottle recycling line in India.”
Magpet awarded the contract for the entire system to Coperion and Herbold Meckesheim, operating companies of Indiana-based Hillenbrand, with the vendors saying there were judged to “consistently and reliably deliver high PET recyclate quality.”
The bottle-to-bottle recycling system first processes the PET bottles into flakes, using Herbold granulators with forced feeding and washing system technologies that process the PET to minimize material loss due to fines formation and thus maximize yield.
Material is the fed into the ZSK recycling twin screw extruder, where the PET regrind is gently melted, intensively dispersed and processed into a homogeneous mass.
Following discharge from the ZSK recycling extruder, the still-warm material stream is transferred via a gear pump to an underwater granulator and an SSP reactor, where it is then condensed and decontaminated.
“In the bottle-to-bottle recycling plant for Magpet, we have united the advantages of Coperion and Herbold Meckesheim technologies,” says Jochen Schofer, head of sales-recycling at Coperion. “All process steps, from mechanical pretreatment to producing finished recyclate, are optimally coordinated to produce PET of high quality—and with maximum energy efficiency.”
“With this bottle-to-bottle recycling system, Magpet takes the next step in their journey. We wish Magpet every success and look forward to continuing to work together,” says Mehmet Kaya, sales team leader for Asia for Herbold Meckesheim.
Magpet Polymers is a PET converter serving east and northeast India, serving regional and global companies and has more than 25 years of experience in the plastic packaging industry.
Coperion offers plastics compounding and extrusion systems, sorting, size reduction and washing systems, feeding, weighing, material handling and pneumatic conveying systems while Herbold Meckesheim produces machinery and plants for reprocessing discarded plastic.
Get curated news on YOUR industry.
Enter your email to receive our newsletters.
Latest from Recycling Today
- Toppoint Holdings expands chassis fleet
- Lego creates miniature tire recycling market
- Lux Research webinar examines chemical recycling timetables
- Plastics producer tracks pulse of wire recycling market
- Republic Services, Blue Polymers open Indianapolis recycling complex
- Altilium produces EV battery cells using recycled materials
- Brightmark enters subsidiaries of Indiana recycling facility into Chapter 11
- Freepoint Eco-Systems receives $50M loan for plastics recycling facility