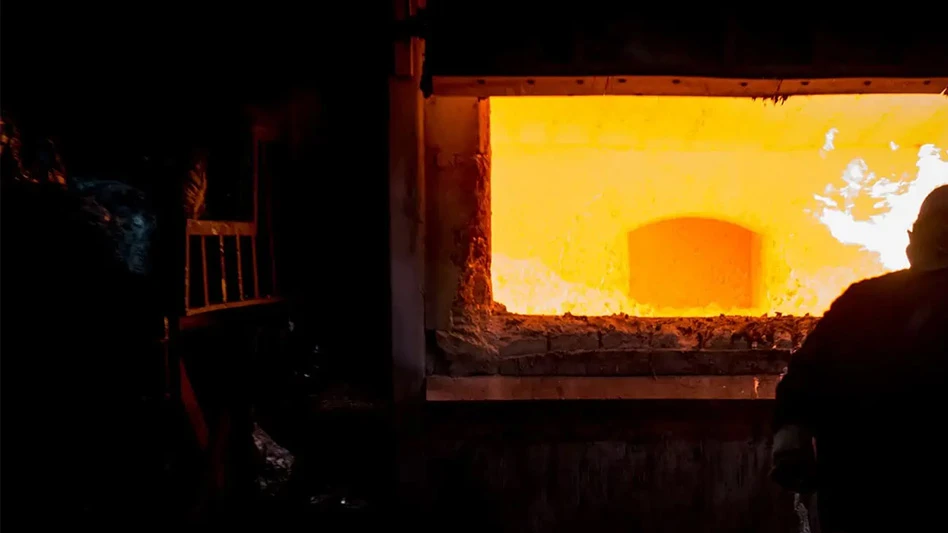
Photo courtesy of Golden Aluminum
Among the recent U.S. Department of Energy (DOE) decarbonization-related grants announced, two are going toward projects planned by existing recycled-content aluminum producers.
Cleveland-based Real Alloy Recycling could receive up to $67.3 million from the DOE for a project at its Wabash, Indiana, facility it calls “Zero Waste Advanced Aluminum Recycling.” That project is geared toward the recycling of salt slag, a melt shop byproduct.
Another $22.3 million in DOE funding could go to Colorado-based Golden Aluminum for its “Nexcast - Next Generation Aluminum Mini Mill” project to be undertaken in Fort Lupton, Colorado.
The two projects to decarbonize and boost U.S. aluminum production go along with those planned by Century Aluminum at an as-yet unselected location and Owl’s Head Alloys in Mississippi as capacity expansion and protection projects selected by the DOE.
According to the project synopsis published by the DOE, Golden Aluminum plans to upgrade its Fort Lupton facility using the Nexcast process to reduce natural gas consumption, improve process efficiency and recycle 15 percent more mixed-grade aluminum scrap.
Although Golden Aluminum has its roots in making cansheet for beverage can production, the upgrades would allow the facility to produce aluminum products for electric vehicle and other clean energy technology applications.
The DOE says the project would be highly replicable among other U.S. aluminum producers and can help solidify the U.S. as a world leader in decarbonized secondary aluminum production.
Although the DOE writeup does not mention the Germany-based SMS Group by name, that metals production technology vendor markets its Nexcast equipment as “the next generation minimill” thanks to its ability to allow the casting and rolling of aluminum strips in one continuous production process.
“The new Nexcast minimill produces strips of all kinds of aluminum and aluminum alloys, with sufficient surface quality for most applications, good to very good thickness, profile and flatness tolerances and [a] very stable final rolling temperature over the strip body length," SMS says.
As part of the Golden Aluminum project, the company will train existing Fort Lupton employees on the new technology. Additionally, the project is projected to improve air quality and the Nexcast technology uses about 85 percent less water compared with existing direct chill technology. The latter feature, the DOE says, “is critical in the increasingly arid western U.S.”
In Indiana, the Real Alloy Recycling project might not increase the amount of scrap purchased in Wabash, but it likely indicates a commitment to keep the facility viable.
As part of the project, Real Alloy Recycling plans to build a processing plant on the back end of an existing secondary aluminum production facility and enable the normally landfilled salt slag components to be recycled back into the aluminum recycling process or beneficially used in other industries, such as cement.
The company says the project could create nine new jobs while also securing the existing 33 jobs at the Real Alloy Recycling facility in Wabash.
Latest from Recycling Today
- Green Cubes unveils forklift battery line
- Rebar association points to trade turmoil
- LumiCup offers single-use plastic alternative
- European project yields recycled-content ABS
- ICM to host colocated events in Shanghai
- Astera runs into NIMBY concerns in Colorado
- ReMA opposes European efforts seeking export restrictions for recyclables
- Fresh Perspective: Raj Bagaria