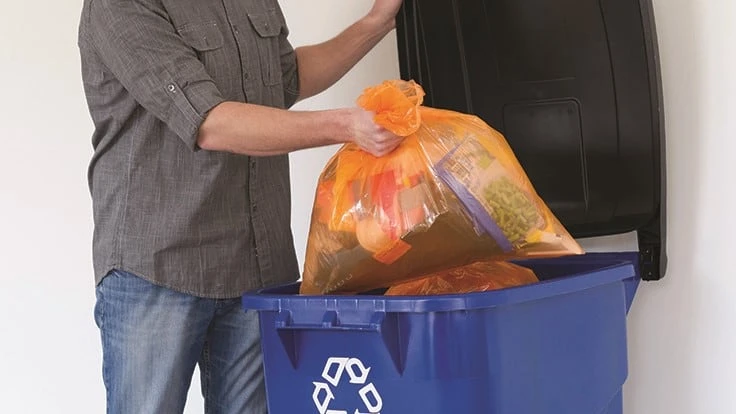
The Alliance to End Plastic Waste, headquartered in Singapore, and Firstar Fiber Corp., headquartered in Omaha, Nebraska, have announced a three-year collaboration to develop an integrated recycling complex alongside Firstar’s material recovery facility (MRF) in Omaha that will target hard-to-recycle plastic. The memorandum of understanding was signed in conjunction with the official opening of Firstar’s new MRF extension.
A news release announcing the partnership says Firstar and the Alliance plan to address the challenge of hard-to-recycle plastics through the integration of sorting, processing and manufacturing facilities to reduce the operational costs of recycling; create value from hard-to-recycle plastic by converting it into suitable feedstock for a variety of useful applications, such as composite lumber for decking; and explore establishing other manufactured plastic products using advanced recycling technologies. If successful, the model could be adopted at other recycling facilities, the partners say.
Dale Gubbels, Firstar president and CEO, says the MRF extension measures 5,000 square feet and will house what he describes as a “PRF,” or plastics recovery facility. At the PRF, the company will produce recycled pellets made from MRF residue as well as from plastic films and other hard-to-recycle plastic packaging collected throughout Omaha and Lincoln, Nebraska, in Hefty Energy Bags. The site also will house plastic lumber manufacturing equipment supplied by Rivalries Corp. of Barrie, Canada. The pelletizing and lumber manufacturing equipment will be able to handle the higher level of contaminants and the broader range of resin types found in the feedstock Firstar will be using, allowing the company “to utilize what otherwise would be trash here at our MRF,” Gubbels says.
Firstar provides recycling services across several Midwestern states, processing and marketing nearly 100,000 tons of recyclables annually. The company has been working with Dow Chemical Co. through the Hefty Energy Bag Program to collect plastic bags and films curbside that are converted into energy, fuel and durable building materials since 2016.
Firstar received $1.35 million from the Alliance to fund the expansion, Gubbels says, adding that the company will receive a substantially larger second round of funding once it has identified additional consumers that can locate nearby and consume the recycled pellets Firstar produces.
“The typical waste management system in the U.S. faces many barriers to recycling and reselling hard-to-recycle plastics because of the lack of end markets and the complex steps and partners involved in collecting, sorting, processing and remanufacturing these plastics,” he says. “With this project, we have the opportunity to bring all of those elements together—literally under one roof—in order to find sustainable solutions and provide value to all plastics, even those previously destined for the landfill or the environment.”
Gubbels says Firstar expects to consume one-fifth of the plastics it reprocesses on-site in the plastic lumber it will produce. The rest will be sold to other end consumers, with the ultimate goal being to find companies that will collocate at the site or within the state. He says Firstar and the Alliance will collaborate on a request for proposals from potential consumers of Firststar’s pellets.
Firstar will blend the plastics it reprocesses to meet specific end market needs, Gubbels adds.
“Recycling is among a number of important areas that must be invested in for a more sustainable future,” says Steve Sikra, vice president and head of Americas for the Alliance to End Plastic Waste. “In line with the Alliance’s mission to end plastic waste in the environment, this project aims to develop solutions that address gaps in the current recycling ecosystem. The Alliance is supporting pioneers like Firstar in creating value for hard-to-recycle plastic at the municipal and regional level. We look forward to working with them to maximize impact with the objective to replicate such efforts in other cities in the U.S. and internationally.”
Gubbels adds that the Alliance indicated that part of the appeal of Firstar’s proposal was the way it integrated a manufacturing component at the MRF. “They are looking for this to be a model,” he says.
“We have long thought that every MRF should look at ways to become more fully integrated,” Gubbels adds. “The circular economy will be well-served when MRF can be a starting point for feedstock and take it through to some kind of end product.”
Latest from Recycling Today
- Aqua Metals secures $1.5M loan, reports operational strides
- AF&PA urges veto of NY bill
- Aluminum Association includes recycling among 2025 policy priorities
- AISI applauds waterways spending bill
- Lux Research questions hydrogen’s transportation role
- Sonoco selling thermoformed, flexible packaging business to Toppan for $1.8B
- ReMA offers Superfund informational reports
- Hyster-Yale commits to US production