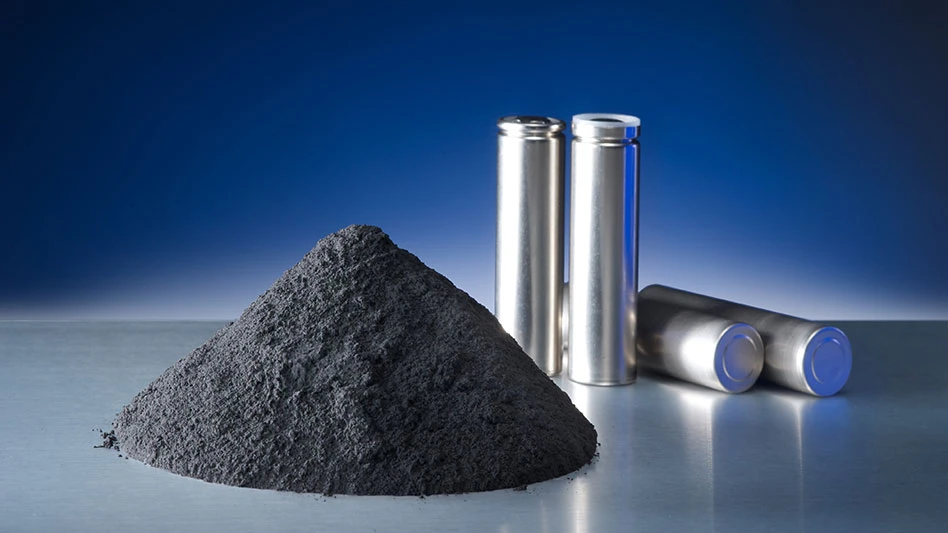
Photo courtesy of EMR
U.K.-based EMR has announced that it is working with academics at the University of Birmingham to explore new ways to sustainably and efficiently recover graphite from end-of-life electric vehicle (EV) batteries. The project is part of the U.K.-based Faraday Institution’s Industry Sprint program that builds industry relationships where specific short-term research needs have been identified.
While lithium-ion battery recycling often focuses on recovering lithium, cobalt and nickel, graphite is classified as a critical material, and commercial EV batteries can contain as much as 11 times more graphite than lithium by mass, the recycling company says.
In addition to being used to make new EV batteries, graphite recovered by EMR can be used in steelmaking and to manufacture brake linings and new pencils.
EMR has helped to advance EV battery recycling technology, including participating in the Recovas research project that brought together recyclers, academics, engineering and energy specialists and automotive manufacturers such as JLR, BMW and Bentley. Earlier this year, EMR consolidated the lessons learned during that project by opening its Battery Recycling Centre in Coventry.
With EMR’s help, researchers at the University of Birmingham will investigate the recovery and regeneration of graphite from black mass and explore ways to upcycle the material to the highest-capacity silicon oxide (SiOx) graphite for use in the most demanding applications, creating a circular economy for the material in the U.K.
EMR’s Managing Director for Technology and Innovation Roger Morton says, “At EMR, our team of dedicated recycling experts are proud to have led the way when it comes to end-of-life vehicle (ELV) recycling, and developing the technologies required for the transition to EVs continues this journey.”
He adds that the volume of graphite used in EV batteries makes finding environmentally friendly and economical recovery methods a growing priority.
“As the recent arrival of our new Battery Recycling Centre in Birmingham shows, the era of industrial-scale EV battery recycling is already here, but this new industry sprint highlights the huge potential that still exists to develop sustainable new technologies and processes that can improve how we operate.”
The company's Battery Recycling Centre in Birmingham can handle more than 2,000 metric tons of EV batteries annually, the company says.
The facility is EMR's second such facility, with the company having opened its first in Hamburg, Germany, in partnership with Northvolt, one of Europe’s largest battery manufacturers, in the late summer of 2023.
The Birmingham plant was opened Sept. 18 with a special ceremony attended by some of the largest names in the automotive sector, including partners from the RECOVAS consortium such as Bentley, Jaguar Land Rover, and BMW.
Batteries arriving at the site, initially sourced via product recalls, warranty failures and end-of-life e-bikes and e-scooters, will be assessed to determine whether the battery pack can be reused in a new vehicle, remanufactured for use in the energy storage sector or recycled, with shredding occurring on-site.
Latest from Recycling Today
- Fitch Ratings sees reasons for steel optimism in 2025
- P+PB adds new board members
- BlueScope, BHP & Rio Tinto select site for electric smelting furnace pilot plant
- Magnomer joins Canada Plastics Pact
- Out of touch with reality
- Electra names new CFO
- WM of Pennsylvania awarded RNG vehicle funding
- Nucor receives West Virginia funding assist