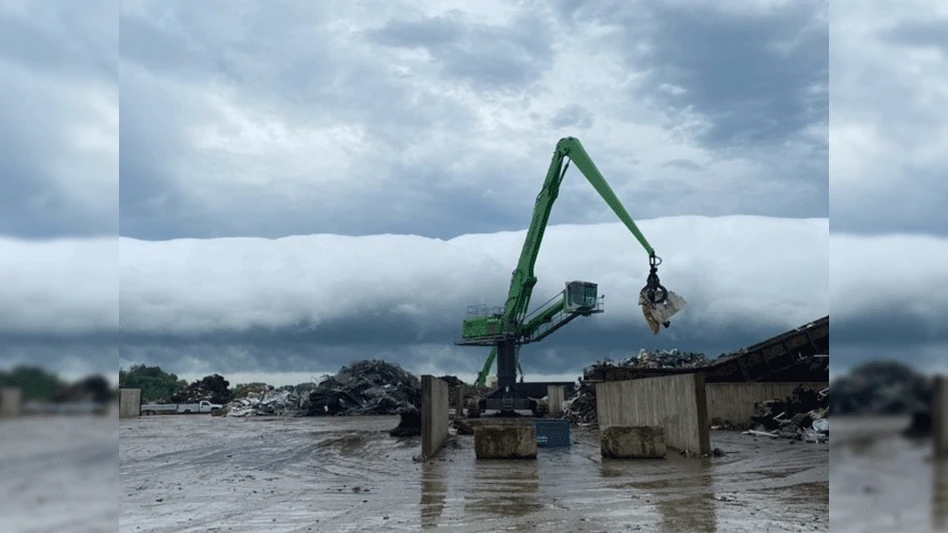
Photo courtesy of Cimco Resources Inc.
Electric material handlers might be viewed as novelties by some scrap processors compared with traditional diesel options, however, material handling equipment manufacturers say electric options are proving to provide the same level of reliability.
“Electric material handlers have had a very long tradition at [Terex Fuchs], with our first electrically powered equipment being delivered to customers as early as the 1980s,” says Florian Bender, head of product management and marketing at Terex Corp., headquartered in Norwalk, Connecticut.
Bender recently visited a scrap yard in Germany that has an electrically powered machine that has accumulated 100,000 operating hours.
“The performance of our electrically powered machines is in no way inferior to that of our diesel-powered variants,” Bender says. “On the contrary, thanks to the extremely load-stable electric motors combined with the high torques, electric machines offer strong performance in the field.”
Loves Park, Illinois-based Cimco Resources Inc. experienced that “strong performance” when it began to operate an electric scrap handler last year. The company added an electric-drive 870 Hybrid material handler from Sennebogen, a German company with a U.S. subsidiary, Sennebogen LLC, based in North Carolina, to its scrap yard in Sterling, Illinois—one of six recycling facilities the company operates in Illinois.
For many years, a diesel-powered crane fed materials to the auto shredder at the Sterling yard. The facility receives up to 800 tons of material per day, with much of it destined for the site’s Metso auto shredder.
“We run multiple products through our shredder, so we have multiple piles of materials around the infeed area,” says Ron Brenny, operations manager at Cimco.
Cimco mounted the 220,000-pound 870 Hybrid material handler on a 9-foot pedestal. The machine features a 90-foot boom that can reach multiple piles of sorted material without moving, and the semistationary material handler features tracks so it can be moved through the yard as needed.
After adding the 870 Hybrid last year, Brenny says he noticed an improvement in efficiency when feeding the shredder, noting it’s a quick machine with fast cycle times despite its large size. “It’s unbelievably quick, probably as fast as a smaller [material handler],” he says.
While reduced mobility can be a concern for scrap processors when trying an electric scrap handler, many material handler manufacturers say they offer solutions.
Christopher Keyes, product manager at Newport News, Virginia-based Liebherr USA Co., says many manufacturers offer battery packs or mobility packs to ensure electric options stay running as they move around a yard. Keyes visited a scrap yard in Munich that was operating a Liebherr electric material handler equipped with a battery pack and says that machine ultimately helped the yard increase its cycle times loading its shredder.
Colleen Miller, sales and national accounts manager at Sennebogen LLC, says while diesel material handlers sometimes have a hard time starting in extreme temperatures, electric material handlers start regardless of the working conditions.
“Whether working in northern British Columbia in negative degrees or in Arizona, electric material handlers always run,” Miller says. “That is an advantage for customers working in extreme conditions—you won’t have issues with ambient temperatures.”
Increasing rates of adoption
Brenny says Cimco is one of the first scrap processors to add the 870 Hybrid into its operations.
Material handler manufacturers say adoption of these machines has been somewhat slow in the U.S., and Keyes says he suspects the fear of change has affected that rate.
“An owner of a company that has been very successful for many years working with the same type of machines is naturally reluctant to change in a new system,” he says.

Cimco's 870 Hybrid sits on a 9-foot
pedestal at its yard in Sterling, Illinois.
However, many makers of material handlers say they think more electric models will be adopted in the U.S. in the coming years.
“Europe is generally very tech-savvy,” Bender says. “The development of electric drives is being actively driven primarily by our European customers. Scandinavia, for example, is playing a pioneering role in the field of zero emissions. Government subsidy programs are increasing demand for more environmentally friendly drives and at the same time accelerating technical developments.”
Miller says high diesel costs in Europe have helped scrap processors make the switch to electric options in that region.
“The cost of diesel is very different in the U.S. than in Europe,” she says. “Diesel costs four times more in Europe. If you’re paying four times [more] for diesel, you’re going to look at other options. … So, European companies are adopting electric models.”
In the U.S., Bender says he sees steadily growing demand for electric-powered material handlers. “While this has not yet reached the same extent as in Europe, we are certain that we will see significantly more electrically powered handling equipment in the U.S. in the future,” he says.
Sponsored Content
Still relying on manual sorters?
Let AI do the heavy lifting. Waste Robotics delivers reliable, high-performance robots tailored for complex waste streams. They require minimal maintenance, are easy to operate, and are designed to boost your recovery rates. Smarter sorting starts with the right partner. Waste Expo Booth #1969 & REMA #2843
Click here to see our robots in action!Sponsored Content
Still relying on manual sorters?
Let AI do the heavy lifting. Waste Robotics delivers reliable, high-performance robots tailored for complex waste streams. They require minimal maintenance, are easy to operate, and are designed to boost your recovery rates. Smarter sorting starts with the right partner. Waste Expo Booth #1969 & REMA #2843
Click here to see our robots in action!Brenny notes that the overall purchase cost might be another factor deterring some processors from adding electric material handlers to their fleets.
“The only thing I can see why someone would have hesitation is the cost,” he says. “You’re looking at paying almost twice as much [for an electric material handler]. You have to justify why you’re paying that.”
Miller adds that some of Sennebogen’s customers have taken advantage of grant funding to integrate electric equipment in their facilities. She says one of Sennebogen’s customers in the port industry received a grant from the Environmental Protection Agency that covered 65 percent of the cost of an electric material handler as well as fully covered the cost of bringing power to the site.
“To think that 65 percent of that project is paid for by the government is an unbelievable victory,” she says.
Despite the higher initial price tag on the electric model Cimco purchased, Brenny says the 870 Hybrid has more than paid for itself in the past year. The company decided to choose an electric option because, he says, it provided dependability, less downtime and significantly less maintenance than diesel options.
Although diesel machines might offer more mobility, Brenny says they require a bigger investment in maintenance, adding that electric options are almost maintenance-free compared with diesel.
“With the cost savings in maintenance, we feel the electric model basically paid for itself in that way,” he says.
Get curated news on YOUR industry.
Enter your email to receive our newsletters.
Latest from Recycling Today
- Recyclers likely to feel effects of US-China trade war
- BCMRC 2025 session preview: Navigating battery recycling legislation and regulations
- Yanmar Compact Equipment North America appoints new president
- LYB publishes 2024 sustainability report
- Plum Creek Environmental acquires Custom Installation LLC
- Avis introduces Harris American Co.
- International Paper in talks to divest 5 European box plants
- Recycled PP from Polykemi, Rondo Plast used in flood protection product