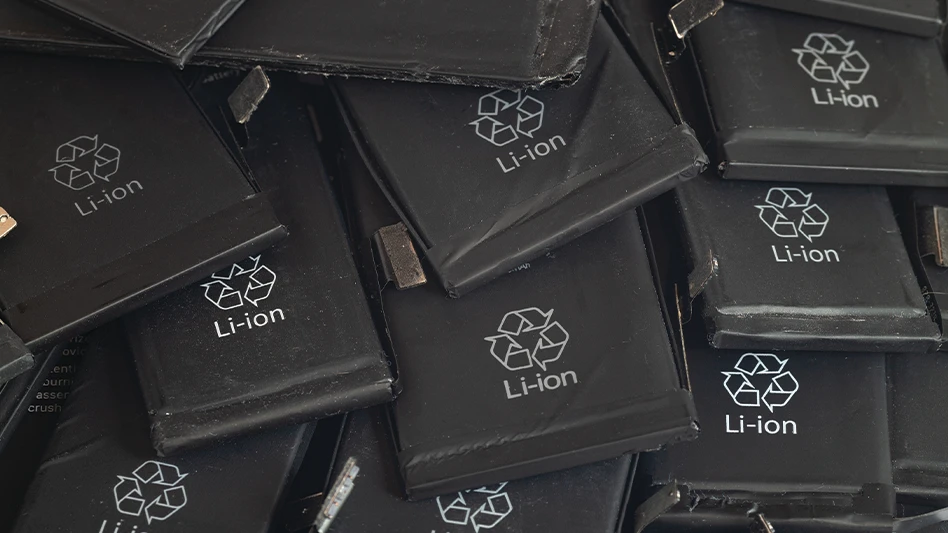
skiminok | stock.adobe.com
Toronto-based lithium-ion battery (LIB) recycler Electra Battery Materials Corp. has provided an update on its battery materials recycling trial taking place at its Ontario refinery complex.
The company says recent optimizations have resulted in additional improved recoveries of lithium, nickel, cobalt and other critical minerals, further bolstering the quality of saleable products. At this time, the company’s plant-scale black mass recycling trial is largely complete, and Electra is compiling an internal report detailing the proprietary methodologies used, as well as various optimizations and modular growth scenarios.
RELATED: Electra to extend black mass processing trial
“Throughout this 12-month demonstration operation, our team has continued to refine and optimize the processes resulting in successive improvements to the saleable products,” Electra CEO Trent Mell says. “These results support our thesis that Electra’s battery materials recycling flow sheet could be an important contributor to our refinery operations.
“The Ontario refinery is a unique asset that can be expanded on a modular basis, leveraging existing permits and infrastructure. As the transition continues toward green energy solutions and electrification, the supply of material in need of recycling will increase. Electra’s technical team successfully operated the first refinery in North America to process black mass on a plant scale, providing important insights on what will be required to operate a black mass plant and support our downstream cell manufacturing clients.”
Recent black mass optimizations:
- Electra has improved its lithium carbonate product quality by nearly 20 percent from its initial processing and product quality is now approaching “technical grade” lithium carbonate. Electra says discussions are ongoing with lithium companies to assess the tradeoffs between collaboration or producing a technical grade in-house.
- The manganese recovery rate has been improved to approximately 95 percent by strategically modifying the use and sequencing of reagents.
- Continued refinements to the process parameters for the nickel-cobalt mixed hydroxide precipitate (MHP) produced from the recycling process have at times improved paymetal concentration in the final MHP product to nearly 50 percent nickel and cobalt, well above quoted market standards. Improved metal concentration creates the opportunity to generate a higher metal payable, thereby improving the potential economics of continuous recycling operations.
- Continued optimization studies are underway, including metal recovery from internal recycling streams such as reusing tailings water as process water to feed the plant, thus making the process entirely closed circuit with the minimal environmental impact.
- Preliminary results of laboratory work to explore the potential of isolating cobalt from nickel contained in the leach liquor using hydrometallurgical methods are positive. Isolating the cobalt could improve the overall payability of both the resultant cobalt and nickel product.
Electra launched a black mass trial in late 2022 at its Ontario refinery complex to recover critical minerals from black mass in shredded LIBs and says it successfully operated its demonstration process throughout 2023 on a semi-continuous basis to maximize product recoveries. The company says the battery recycling strategy is part of a multipronged development plan for a battery materials park supplying battery-grade material to third-party cathode precursor manufacturers.
The company says it has developed proprietary hydrometallurgical technology targeting all of the critical minerals present in the black mass as saleable products. Once recovered, the products can further be upgraded to battery-grade materials and reused by gigafactories to produce batteries or other products.
According to Electra, additional black mass program highlights include:
- the processing of 40 tons of black mass material in a plant-scale setting;
- an improvement in recovery rates for all targeted materials—lithium, nickel, cobalt, graphite and manganese—since the start of the trial in December 2022;
- the shipment of 28 tons of nickel-cobalt MHP product to customers;
- and the reduction in reagent requirements and, in some cases, the use of alternative and less costly reagents for improved overall metal recovery.
Electra claims established North American battery recyclers have focused on collecting and shredding batteries, with the resulting black mass material primarily exported or treated by a pyrometallurgical smelting process that has a higher carbon footprint and lower metal recoveries than hydrometallurgical processes.
Latest from Recycling Today
- Ascend Elements alters Kentucky plans, will return $164M grant to DOE
- US plastic scrap imports reached record high in 2024
- Egypt soaks up European scrap: Navigate Commodities
- S. Norton hosts tour of shredder yard
- Tariffs prepare path for US metals production boost: Goldman Sachs
- PCA announces planned management changes
- Greif CEO says Q1 results highlight ‘resilience’ of new business model
- Cards Recycling, Total Environmental form strategic partnership