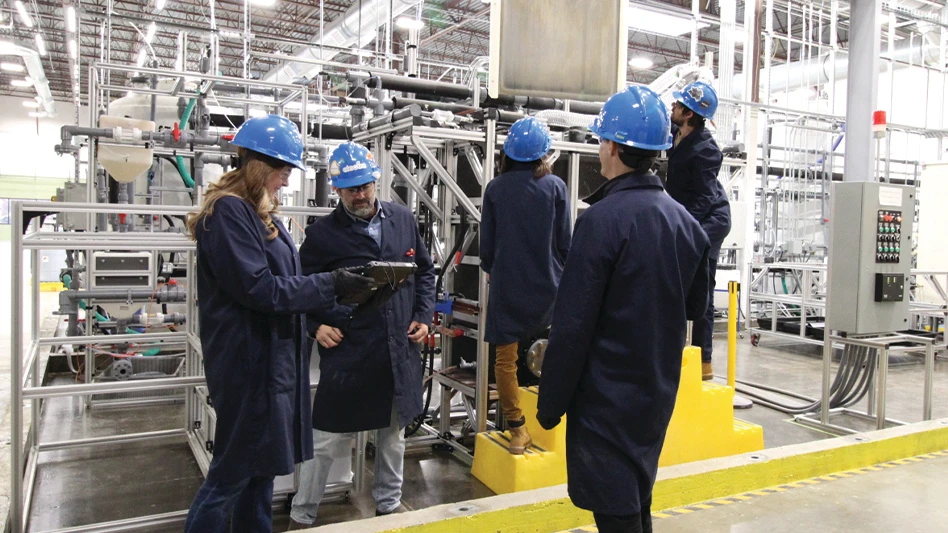
Photo courtesy of Electra
Electra, a Boulder, Colorado-based low-carbon iron developer, has commissioned its pilot plant in Boulder. The company says the pilot will demonstrate its technology to produce metallic iron from already mined, high-impurity, commercially stranded ores to accelerate decarbonization, sustainability and circularity across the ore-to-steel value chain.
The company says 90 percent of steel production’s CO2 emissions come from ironmaking, and its electrochemical process takes on this challenge by operating at 140 degrees Fahrenheit, enabling seamless integration of renewable energy resources and making emissions-free iron possible at temperatures “colder than coffee.”
RELATED: Nucor invests in zero-carbon iron startup
Electra's process intakes a wide range of ores and the principal iron ore impurities like alumina and silica are selectively refined as coproducts. Electra claims its low-carbon iron has greater than 99 percent purity and, combined recycled scrap steel, offers the highest value-in-use for electric arc furnace (EAF) steelmakers, while reducing the capital intensity, cost and waste across the value chain.
The pilot is designed to produce low-carbon iron in approximately 1-meter square plates, and the company is increasing capacity in a phased approach to validate modularity. By repeatedly connecting the iron plates already demonstrated at the pilot scale, the plant capacity is increased to millions of tons of iron production at the commercial scale. BHP, a seaborne iron ore supplier to the steel industry based in Australia and an Electra investor, supplied the iron ores for the pilot.
“Clean iron produced from a wide variety of ore types is the key constraint to decarbonizing the steel industry sustainably,” Electra co-founder and CEO Sandeep Nijhawan says. “With support from our partners across the value chain, the pilot brings us closer to our goal of producing millions of tons of clean iron by the end of the decade.”
Another Electra investor is Charlotte, North Carolina-based steelmaker Nucor Corp., and its Executive Vice President of Raw Materials, Noah Hanners, says Electra’s pilot plant is a significant step towards a cleaner, more sustainable and circular steel industry. “Electra’s pure iron metal is uniquely positioned to allow the upcycling of a broader range of steel scrap into higher-value sustainable steel products, improving the circularity and sustainability of the steel industry," he says.
“While the road ahead is long, the arc of our progress is fast," Electra co-founder and Chief Technology Officer Quoc Pham adds. "The commissioning of the pilot within three-and-a-half years of the company’s founding reflects the strength of our team and our ability to leverage knowledge from adjacent industries and push the boundaries of clean iron production to tackle one of the hardest-to-abate sectors of our economy.”
Latest from Recycling Today
- Biden officially blocks Nippon Steel’s acquisition of US Steel
- Highland Sanitation awarded solid waste and recycling contract in Wanamingo, Minnesota
- Ecobat gathers support for California permit renewal
- RecyclX platform designed to provide materials transparency
- Turkish mills sampled wide scrap market in 2024
- GLE Scrap Metal acquires interest in Mallin Cos.
- 2024 marks strong year for Van Dyk
- Recycled metal portrayed as former dictator’s fiefdom