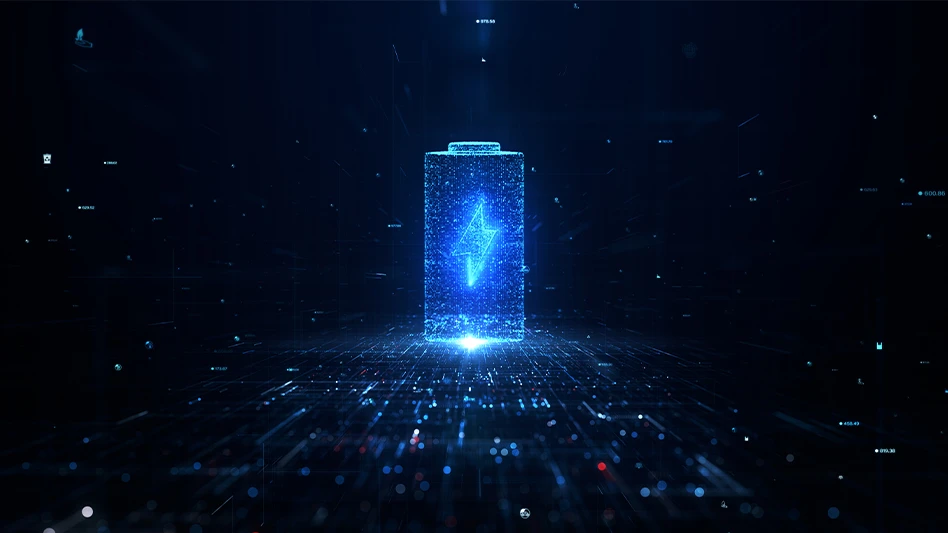
KanawatTH | stock.adobe.com
Toronto-based based lithium-ion battery recycler Electra Battery Materials Corp. says it has successfully completed the first plant-scale recycling of black mass material in North America, recovering critical metals such as nickel, cobalt and manganese using its proprietary hydrometallurgical process at its refinery in Ontario.
The results, as well as interest expressed by potential commercial partners, have prompted Electra to extend its black mass processing and recovering activities through June, beyond the company’s initial target of 75 metric tons.
“Initial results from our black mass trial are extremely encouraging,” Electra CEO Trent Mell says. “The results validate that our proprietary hydrometallurgical process is able to recover high-value elements from shredded lithium-ion batteries effectively and confirm the commissioning work we have completed to date has made our refinery operational again after being idle for more than a decade.”
Mell says the preliminary results also mark what Electra believes to be the first recovery of a mixed hydroxide nickel and cobalt product. The company says it now can “maximize the cashflow opportunities generated through the sale of multiple products critical to the EV [electric vehicle] battery supply chain in North America.”
.jpg)
processed at Electra's refinery
in Ontario.
Electra launched its black mass demonstration plant at the end of December 2022, which was designed to recover and recycle high-value elements in lithium-ion batteries such as nickel, cobalt, manganese, copper, lithium and graphite. The company says engineering studies will be completed to assess capital costs for a permanent recycling facility adjacent to its cobalt refinery.
Electra says it has identified multiple sources of supply and has yet to determine the amount of material to be processed and recovered through June, but notes it consumes end-of-life consumer electronics, lithium-ion battery manufacturing scrap, end-of-life lithium-ion batteries from the e-mobility sector and end-of-life batteries from energy storage systems.
All of Electra’s recovered material will be sold to third-party companies for additional processing and resuse.
“We have established relations with black mass producers in North America and abroad to support our continued efforts,” Mell says.
Cobalt refinery project update
Electra says since November of last year, it has made continued progress on the commissioning and construction of its cobalt refinery project despite ongoing supply chain disruptions and equipment delivery delays.
The company lists several developments through Feb. 10:
- completion of all testing of existing brownfield equipment;
- completion of 90 percent to 95 percent of all procurement;
- completion of 90 percent to 95 percent of detailed engineering;
- completion of approximately 90 percent of the erection of the solvent extraction plant;
- completion of construction of the cobalt sulfate loadout facility; and
- increased the project owners’ team to 31, including engineers, operators, lab technicians and more.
However, because of critical equipment damage and continued supply chain issues, Electra has withdrawn its fourth-quarter 2022 guidance along with any forward-looking statements previously made on the timing of commissioning, capital spend and production of the refinery.
Sponsored Content
Don’t Let Screen Jamming Decrease Material Recovery
General Kinematic’s FINGER-SCREEN™ prevents material bypass with its tapered finger designs, unique cam-out surfaces, and staggered positions. It allows for continuous, dynamic material flow to enhance and optimize separation and classification. If your current setup is prone to process challenges, let GK’s FINGER-SCREEN™ be the solution!
Optimize your process today with GK!
delivered to Electra's refinery
in Ontario.
A custom-built falling film evaporator vessel was damaged in transit, and though deemed suitable for installation, the equipment will require on-site repairs before it can be commissioned. The evaporator vessel costs about $600,000 and is used to vaporize water from the cobalt solution before it can be crystallized into cobalt sulfate.
Global supply shortages of microchips also have resulted in delivery delays of several process control system components, and although Electra says it has advanced the construction of the refinery, it has been unable to progress fully on some work projects pending delivery of the process control components.
“While we evaluate a number of options, including the procurement of equipment from alternative sources of supply, construction has progressed ahead of equipment deliveries,” Mell says. “Site-level leadership is completing a baseline review of the project and the company anticipates providing an update in conjunction with our year-end results to be issued before the end of March.”
Get curated news on YOUR industry.
Enter your email to receive our newsletters.
Latest from Recycling Today
- Ace Green Recycling inks lead, lithium licensing agreements in Armenia
- Call2Recycle partners to start high-energy battery recycling program
- Closed Loop Partners releases report on small-format packaging recovery
- Battery recycling and reuse management platform launches
- Elemental Holding secures European funding
- BCA subsidiary offers EV battery pack shredder
- Europe’s paper and board industry rebounds in 2024
- Europe’s WEEE regulations might need a rethink