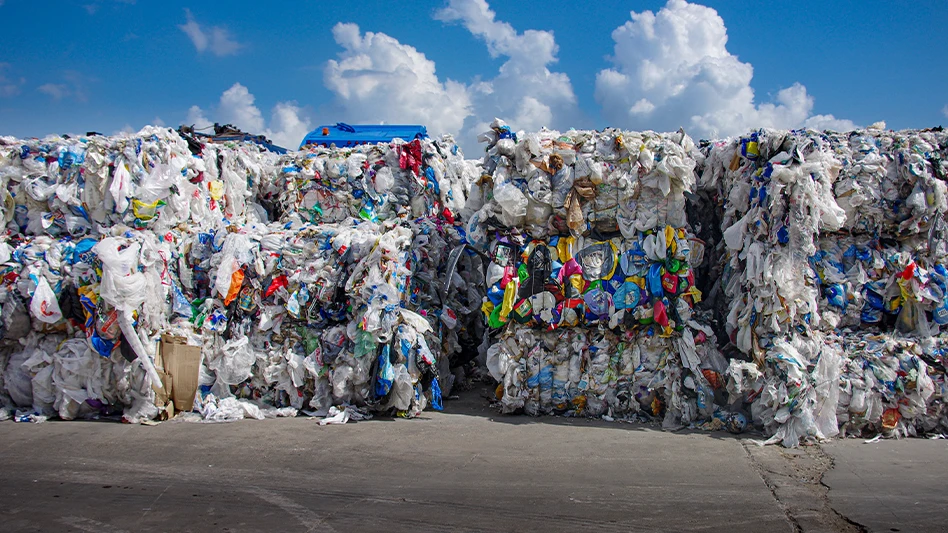
Philip | stock.adobe.com
EFS-plastics, a Listowel, Ontario-based plastics reclaimer, intends to invest around $17 million in recycling technology upgrades at its plants in Hazelton, Pennsylvania, and Lethbridge, Alberta, with the aim of increasing its capacity to process films and rigid scrap.
According to Hendrik Dullinger, EFS-plastics U.S. vice president of business development, each facility will receive half of the funding. At the company’s Hazelton plant, which primarily focuses on recycling flexibles, the goal is to open up its capability to accept different grades.
RELATED: EFS-plastics introduces new product line
“We have a full film recycling line there already, but we want to open up our sales floor for a greater spec of materials,” Dullinger says.
The facility currently recycles Grade A commercial films, but, citing increased competition for those bales, Dullinger says upgrades to its sorting, washing and extrusion equipment will allow it to take on Grade B and C bales. In addition, the site also will start testing curbside collectible films. “We’re considering changing parts along the entire line to meet that,” he adds.
The new sorting equipment is expected to be operational in early 2024, while the third processing line is expected to be up and running by the summer.
The expansion in film processing capability is designed to meet potential requirements under extended producer responsibility (EPR) legislation and help brands meet circularity goals, Dullinger says.
“Because we have a large footprint on the Canadian side of the border, this is what we have to focus on when it comes to curbside film, is the upcoming EPR legislation,” he says. “It requires the PROs [producer responsibility organizations] to look at films and flexibles and make sure they can become circular, so we’ll use Hazelton as a test facility as well to see how well it can do on curbside.
“But also in the U.S., if you look at some of the brands, brand commitments are a little weak at this point, but we still believe in the long-term,” he adds. “Brands will have to take action. We know that they’re increasingly looking at flexibles, so there will be a push eventually to take more of the residential film materials.”
The 70,000-square-foot plant in Lethbridge, which was added in 2022 and has primarily served as a secondary sorting facility feeding the company’s Listowel operation, will add washing and extrusion equipment.
The facility processes Nos. 1-7 mixed rigid plastic bales sourced from material recovery facilities in the western U.S. and Canada.
“The idea when we started [the Lethbridge plant] out was always to eventually add technology,” Dullinger says. “So, it was [at first] a smaller start to fill capacity in Listowel, but now, we’re ready to take the next step there.”
RELATED: Companies partner to make compost bag with recycled content
Dullinger adds that sorting equipment in the front of the line is getting more and more important. Though equipment suppliers haven’t been revealed yet, he says the company is doing a lot of testing. “We don’t buy anything off the shelf,” he says. “Everything is engineered for that plant in Alberta. That’s also the location for EFS-equipment, so we are our own OEM [original equipment manufacturer]. We do our own silos, we do a lot of the conveyor belts and put together the parts that fit it the best, so it’s a homemade engineered system.”
Upgrades at the Lethbridge location are expected to be operational during the first quarter of 2025.
Latest from Recycling Today
- Aqua Metals secures $1.5M loan, reports operational strides
- AF&PA urges veto of NY bill
- Aluminum Association includes recycling among 2025 policy priorities
- AISI applauds waterways spending bill
- Lux Research questions hydrogen’s transportation role
- Sonoco selling thermoformed, flexible packaging business to Toppan for $1.8B
- ReMA offers Superfund informational reports
- Hyster-Yale commits to US production