
The market for OTR tires is constantly growing and according to industry experts, OTR tires represent only one percent of the tire industry in unit volume. However, they take over 15 to 20 percent of the total weight of all tires.
Vast supplies of OTR tires lie in wait at mines, work sites, recycling facilities or have been illegally dumped. These tires can weigh around 12,000 pounds (5443 kilograms) each and cost thousands of dollars to move from location to location. These stockpiles are loaded with valuable materials that can be recovered for several uses such as crumb rubber, pyrolysis, landscape mulch, recovered Carbon Black (rCB) and others.
Eagle International’s Portable OTR Downsizing System consists of three machines: the OTR Debeader, the Punch Cutter II and the Titan II. All three machines are portable and work together to make OTR tires more manageable for recycling purposes. Learn more about how these machines work together HERE.
Each machine is designed to be road legal and can be hauled from location to location. Eagle International is the only provider of an entirely portable OTR recycling system. This reduces the need to load and haul thousands of whole OTR tires. Instead, it allows the scrap tires to be downsized for more efficient loads without the need for expensive permits or pilot cars. Since the vast sizes of these tires require downsizing prior to performing most processes, the transportation savings are an easy revenue benefit for these businesses.
Moving these three machines from one OTR storage site to the next will increase efficiency when processing the tires.
In THE FIRST STEP of the OTR Downsizing System, the Eagle OTR Debeader removes the high-quality steel bead. Pulling the bead from OTR tires not only provides high-quality scrap steel for recycling, but it also eliminates damaging material from the tire that can greatly reduce the life of tire shredding equipment.
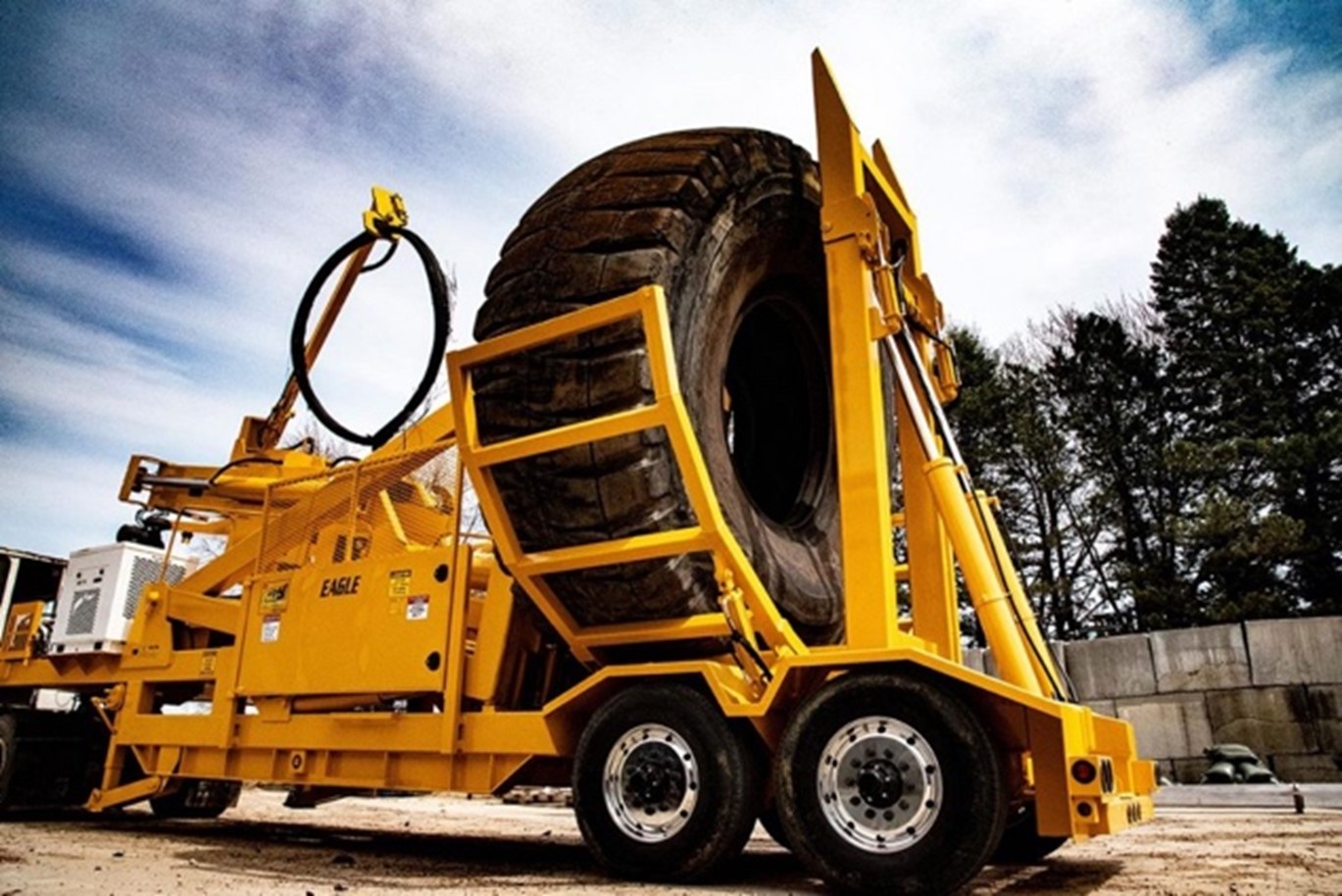
THE SECOND STEP includes the Punch Cutter II, which is used to cut the OTR tire in half down the center of the tread like a bagel. This step may not be necessary depending on the size of tires being processed and what the downstream system (shredder) requires for maximum size of feedstock.
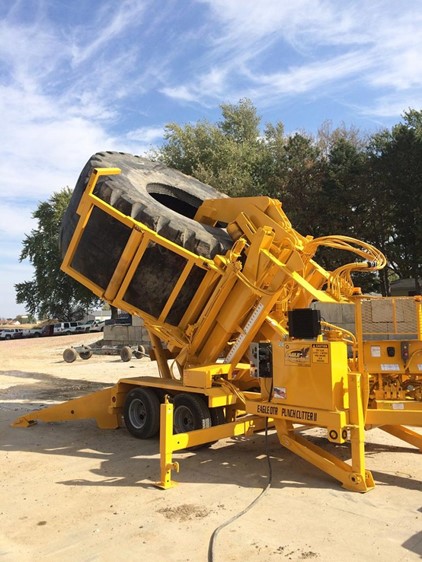
THE THIRD, AND FINAL, STEP is the Titan II. This OTR tire shear is used to cut the halved tires into smaller segments that are acceptable for downstream processing. The Titan II is also capable of cutting whole tires up to 40 inches (102 centimeters) tread width (i.e. 40.00R57) with beads still intact.
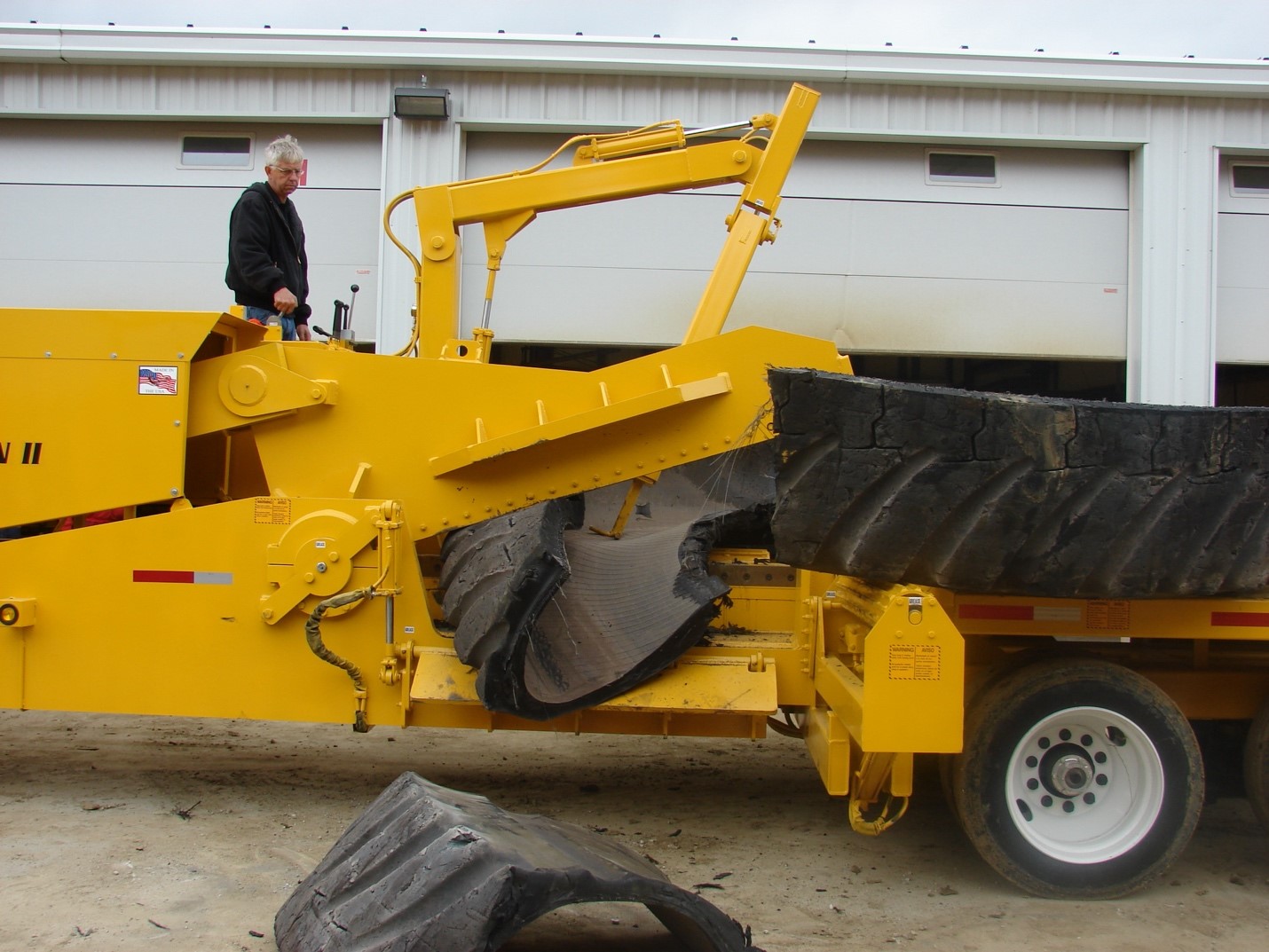
Once the tire has been halved and segmented, you can reduce the size of an OTR tire by approximately 70 percent. This means you can save money by hauling more scrap rubber in each load that leaves the site.
Latest from Recycling Today
- Athens Services terminates contract with San Marino, California
- Partners develop specialty response vehicles for LIB fires
- Sonoco cites OCC shortage for price hike in Europe
- British Steel mill’s future up in the air
- Tomra applies GAINnext AI technology to upgrade wrought aluminum scrap
- Redwood Materials partners with Isuzu Commercial Truck
- The push for more supply
- ReMA PSI Chapter adds 7 members