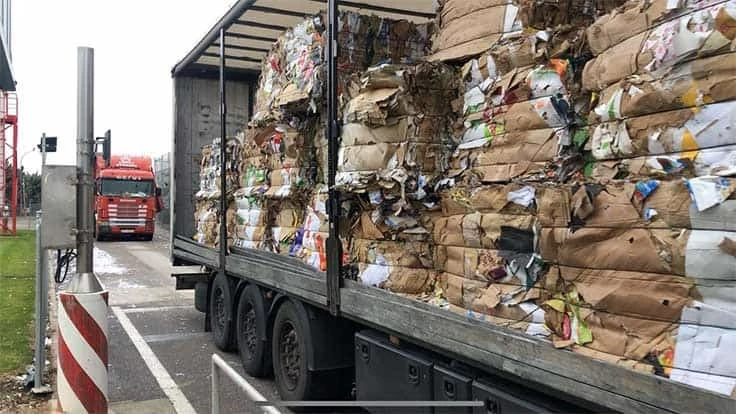
DS Smith
DS Smith, headquartered in London, has implemented a new moisture-measuring technology at some of its mills in Europe to assess the quality of incoming raw materials and to increase transparency with suppliers. The new system, dubbed Moisture Gate, measures moisture content in paper for recycling (PFR) that arrives at its paper mills in Rouen, France, in and Dueñas, Spain.

Guy Lacey
Guy Lacey, next generation technology director at DS Smith, says the Moisture Gate technology was first developed at those two mills when they were owned and operated by Europac. As the technology was being refined, DS Smith acquired the two mills in January 2019. Lacey says the company continued testing and refining the Moisture Gate system throughout 2019.
“When we acquire a business, we look at all of [the acquired company’s] programs,” he says. “In the summer of 2019, we started looking at this technology, and it was up and running at the end of last year.”
DS Smith reports that measuring moisture in PFR is typically a challenging and time-consuming task. The company states that these methods often only manage to spot check individual paper bales arriving for recycling rather than offering an overall measurement. The company’s mills in Rouen and Dueñas would have trucks coming in loaded with about 25 metric tons of PFR every hour, and it was challenging to develop a system that more accurately provided results for the total volume of inbound PFR.
Before DS Smith had this technology, Lacey says the company would manually measure the moisture levels of incoming fiber bales. With Moisture Gate, he says trucks can drive up slowly, and the technology more accurately provides data on moisture content.
“I think the technology confirmed what we knew or thought,” Lacey says. “Depending where material is coming from, you might have a good idea of what a bale is like based on if it was stored inside or coming from outside. The technology backs up what we knew. You can’t beat the power of data once you have it there.”
Because of the technology’s effectiveness, Lacey adds that it also was rolled out to the company’s mills in Kemsley, U.K., and in Zărnești, Romania in late 2019. He says the technology is enabling some of the company’s mills to accurately measure moisture content in PFR and increase transparency with its recovered fiber suppliers to ensure fair market price and improved quality as well.
Challenges of measuring moisture content
Accurately measuring the moisture content in a truckload of recovered fiber can be challenging. Existing methods, such as moisture meter plates, ovens and other manually operated systems, only measure a spot or small percentage of the overall volume. The same load, measured by these methods, often produces conflicting moisture readings. Also, paper yield can vary by as much as 6 percent between summer and winter as a result of moisture content variation alone, according to the company.
Another factor is overcoming frustrations experienced by some suppliers that are caused by unreliable data and old technology. When a high degree of moisture is detected in bales, suppliers then seek reliable, transparent data to support the credit, or supplier ranking of incoming materials, that DS Smith offers.
DS Smith reports that in customer surveys, suppliers have requested more data-driven insight and auditable solutions to help them improve their quality and increase their financial returns. In 2019, DS Smith introduced near-infrared technology (NIR) to better measure fiber quality and identify contaminants, such as metal and plastic. The company more recently looked into solutions for measuring moisture content.
Moisture Gate solution

All trucks that arrive at DS Smith paper mills that are equipped with the Moisture Gate pass through the scanner, which allows the company to accurately identify the moisture content of the load, not just on the surface area of the delivery. About 75 percent of the truckload is scanned within 30 seconds and, in less than one minute, a reading for the entire truck is calculated and recorded and the truck is free to proceed. The technology doesn't lead to vehicles being delayed at the mill. It's a simple process:
1. Trucks pass through the moisture gate at a speed of 3 to 5 kilometers per hour (or about 2 to 3 miles per hour). The moisture gate radiates the area between the antennas and scans the load. (See figure 1.)
2. Each scan covers about 5 cubic meters of the load. It takes about eight scans to measure a truck, which are all completed in about 30 seconds. (See figure 2.)

3. In less than one minute, an accurate moisture content readout is delivered on the screen without any manual intervention. The Data are then sent to the supplier in an easy-to-read format, along with weekly reports compiled.
Lacey says the data provided by Moisture Gate enables the company to share more information with its recovered fiber suppliers, which leads to better quality and price.
“We work very closely with our suppliers,” he says. “There are no secrets—we share the data, which is mutually beneficial. We can have higher quality recyclate coming into the mill, and the whole industry can increase recycling levels.”
The company reports that the technology also ensures that recyclers are paid a fair market price for their materials.
The system enables DS Smith to share moisture content data in easy-to-read formats and via weekly reports. The data help suppliers to identify and address any issues and help them advise customers whose waste management processes may need to be adjusted to meet targets.
“By improving measures of incoming paper for recycling, our mills could see increased manufacturing yields,” says Nuno Messias, waste paper manager at DS Smith Recycling Division. “Not only this, but our transparent reporting system will provide clear communications to customers.”
Latest from Recycling Today
- GreenMantra names new CEO
- Agilyx says Styrenyx technology reduces carbon footprint in styrene production
- SABIC’s Trucircle PE used for greenhouse roofing
- Hydro to add wire rod casthouse in Norway
- Hindalco to invest in copper, aluminum business in India
- Recycled steel price crosses $500 per ton threshold
- Smithers report looks at PCR plastic’s near-term prospects
- Plastics association quantifies US-EU trade dispute impacts