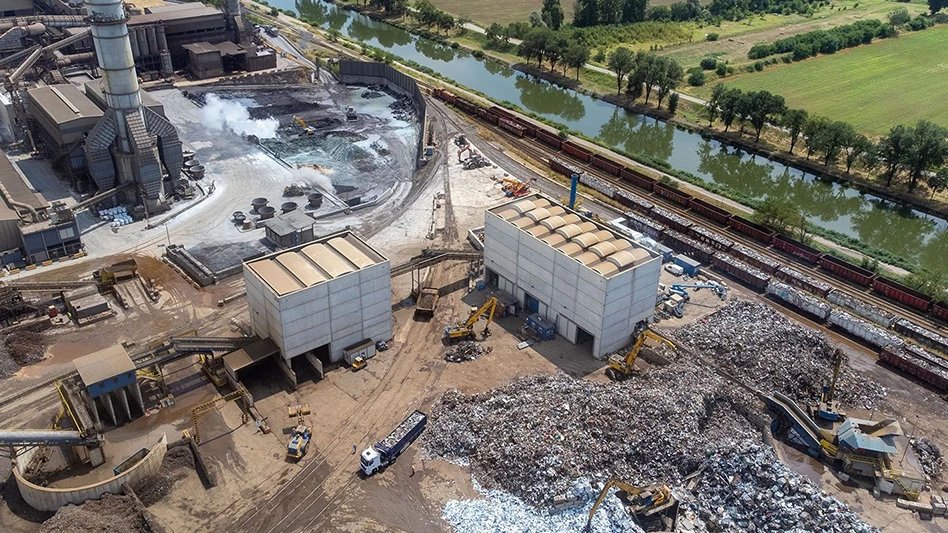
Photo courtesy of Danieli & C. S.p.A.
Danieli & C. S.p.A., Buttrio, Italy, has supplied a 7,000-horsepower (hp) metals shredding plant to steel producer Acciaieria Arvedi, who will operate the plant near its electric arc furnace (EAF) mill in Cremona, Italy.
According to Danieli, the plant has been designed to process 200 tons per hour of ferrous scrap produce a shredded grade that will be “optimal” for an EAF operation.
The Danieli Centro Recycling shredder, which is being commissioned this autumn, is described by the steelmaking and recycling technology supplier as a “high-performance, shredder-based steel scrap processing plant.”
To help meet the adjacent Cremona EAF mill’s feedstock needs, the shredder is intended to process nearly 1 million tons per year of what Danieli calls light-to-medium iron grades of scrap and sheared light demolition scrap.
Acciaieria Arvedi’s goal, says Danieli, is to “obtain a high-density quality product that guarantees the best EAF performances –yield and power consumption—and further shrinkage of [its] carbon footprint.”
A ferrous downstream line separates steel from nonferrous metals using what Danieli calls high-efficiency, cascade air and magnetic systems, “enabling cleanness levels close to 100% percent” for scrap headed to the EAF mill.
An accompanying offline nonferrous separation line will allow Acciaieria Arvedi to harvest zorba and zurik for resale.
Before reaching the main shredder, a pre-shredder has been installed to process heavy bales, thus reducing the power absorption and limiting the wear inside the other shredding chamber, says the equipment supplier.
The 7,000-hp shredder is fed by what Danieli calls a 30 meters (98 feet) long “jumbo industrial-strength steel belt conveyor that constantly feeds the powerful machine.”
Danieli says its patented, variable-speed drive system (also known as an inverter) will help to ensure electrical power consumption that is up to 20 percent lower than many existing systems.
A noise and vibration analysis system has been designed to automatically detect scrap pieces that cannot be shredded so that an automatic control can direct them out a reject door.
“A dedicated maintenance system informs about components’ wear and tear, suggesting the right replacement time,” adds Danieli.
On its website, Acciaieria Arvedi refers to its Cremona site as “Europe’s first and the world’s second mini-mill for the manufacture of flat rolled steel.” According to the firm, since 2009 the site has “two complete lines for the production of steel in the form of hot rolled coils, each fitted with its own melt shop.”
Get curated news on YOUR industry.
Enter your email to receive our newsletters.
Latest from Recycling Today
- Two factors raise ferrous export questions in April
- Analyst: Scrap imbalance lost amid copper’s critical status
- AF&PA report shows decrease in packaging paper shipments
- GreenMantra names new CEO
- Agilyx says Styrenyx technology reduces carbon footprint in styrene production
- SABIC’s Trucircle PE used for greenhouse roofing
- Hydro to add wire rod casthouse in Norway
- Hindalco to invest in copper, aluminum business in India