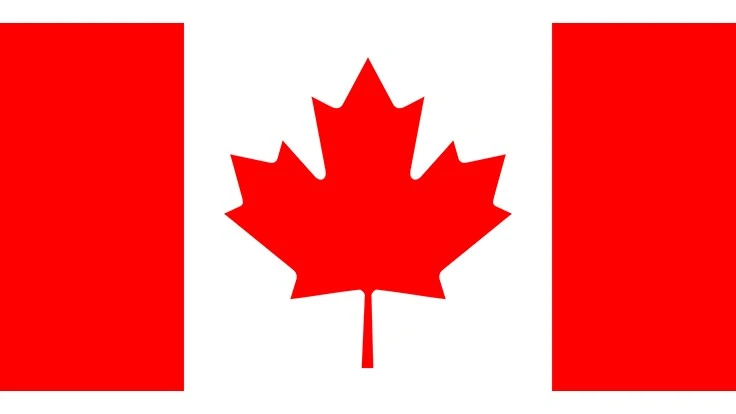
Kingston, Ontario-based Cyclic Materials says it has completed its “proof-of-concept bench-scale test work, carried out at Kingston Process Metallurgy Inc. (KPM), as well as the delivery of the first samples of high-purity recycled rare-earth oxides to downstream service providers.”
Cyclic says its recovery process means a circular supply chain for rare earths “is no longer a pipe dream.” Cyclic Materials CEO Ahmad Ghahreman tells Recycling Today rare-earth elements recovered by the company are neodymium, praseodymium, dysprosium, terbium and “small amounts of samarium.” The elements are used in electronics, battery, magnet and metal alloying applications.
“There is a huge opportunity to produce rare-earth elements in a more responsible and sustainable way,” says Ghahreman. “We aspire to reduce the pressure to open three-to-four new mines, thereby improving land use and reducing the use of harsh processing chemicals.”
Cyclic says it now is focused on building its pilot plant, which it calls “the first step toward scaling up its recycling process to satisfy exploding demand.”
“The continued electrification of society will be key in curbing carbon emissions and mitigating the worst effects of climate change,” the company says. It calls obtaining sufficient rare-earth metals “a major barrier to achieving that goal.” The firm adds, “Cyclic Materials aims to remedy this issue using one of the oldest tricks in the resource management playbook: recycling.”
The Canadian company says most metals are produced with approximately 40 percent recycled content, but only about 1 percent of rare earths are recovered at end of life, meaning “the rare earth circular economy could grow as much as fortyfold in the coming years.”
Cyclic says “a robust supply chain for recycled rare earths will accelerate domestic production of these materials, which are deemed ‘critical’ by many Western countries. Recycling also will decrease the need for new green-field mining projects, which can take years to break ground, require massive capital investment and carry profound environmental consequences.”
The company says Ghahreman’s track record includes helping devise processes that are “currently being employed, at scale, to turbocharge the efficiency of copper mines across the world and introduce recycled lithium back into the supply chain.”
Ghahreman’s LinkedIn profile indicates he served as a technical advisor to lithium-ion battery recycling firm Li-Cycle and on the mining front has served with Canada-based Barrick Gold Corp. and the Queen’s University Department of Mining in Kingston. The CEO also tells Recycling Today he also was co-inventor of technology deployed by Colorado-based copper sulfides producer Jetti Resources Inc.
With its initial sample delivery, Cyclic Materials has taken its first step toward revolutionizing rare-earth recycling in a similar fashion, claims the company.
“Today’s shipment of sample product is an important step in the creation of a sustainable supply of these critical metals,” says Ghahreman. “It demonstrates the high-quality product we produce and will allow us to build the downstream supply chain necessary to create rare earth magnets with 100-percent-recycled material.”
Latest from Recycling Today
- AF&PA report shows decrease in packaging paper shipments
- GreenMantra names new CEO
- Agilyx says Styrenyx technology reduces carbon footprint in styrene production
- SABIC’s Trucircle PE used for greenhouse roofing
- Hydro to add wire rod casthouse in Norway
- Hindalco to invest in copper, aluminum business in India
- Recycled steel price crosses $500 per ton threshold
- Smithers report looks at PCR plastic’s near-term prospects