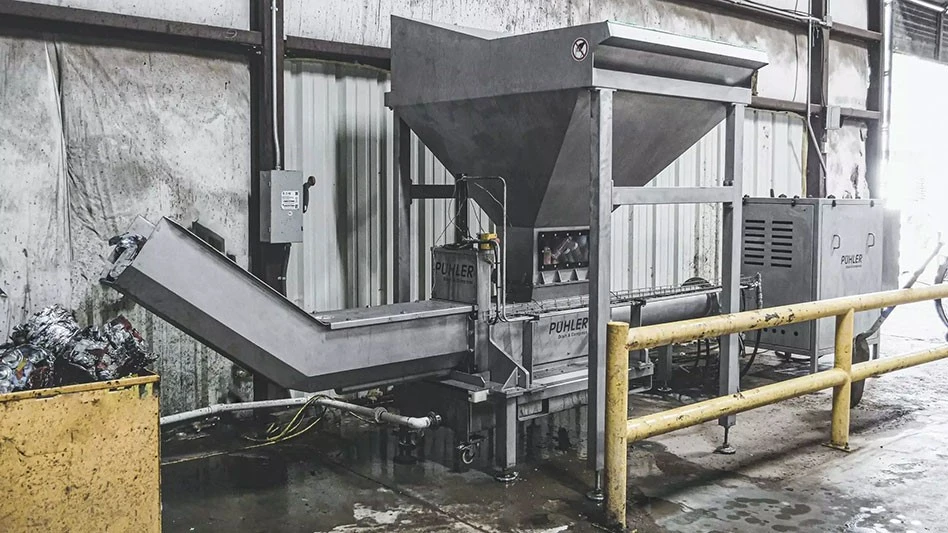
Photo provided by Weima America Inc.
Custom Recycling, which offers industrial and demolition recycling services from its facility in York, South Carolina, has added a Puehler G.200 drainage press from Fort Mill, South Carolina-based Weima America Inc. to its facility to process pallets of filled aluminum cans that were rejected from local beverage suppliers and canning lines.
The Puehler G.200 drainage press empties filled cans and compresses the aluminum in one step. According to a press release from Weima about the installation, the cans that the machine drains and compresses “would typically be dumped out by hand or discarded into a landfill” were it not for the drainage press.
Custom Recycling receives used beverage containers (UBCs) from local beverage manufacturers and distributors. With the new drainage press, Custom Recycling dumps cardboard cases of full cans into a tipping device used to load the hopper of the drainage press. The machine punctures the cans within the hopper, and the liquid drains out of the machine while the aluminum is compressed into 200-millimeter discs. According to Weima, those discs are baled and left to dry for two to three weeks, at which point they are sold to a mill for further processing. The cardboard packaging also is baled and sent to be recycled.
Although UBC recycling only comprises 2 percent of Custom Recycling’s overall business, Weima reports that Custom Recycling processes between 1,000 and 1,200 pounds of UBCs per day.
“While looking for a solution in separating the liquid and aluminum for our full beverage cans, we came across Weima. Luckily, they were local and invited us the next day for a demonstration,” says Tim Weaver, CEO and owner of Custom Recycling. “Instead of waiting for [a machine] to be built, they allowed us to purchase their floor model, so we didn’t have to wait.”
Latest from Recycling Today
- Haber raises $44M to expand to North America
- Canada Plastics Pact releases 2023-24 Impact Report
- Reconomy brands receive platinum ratings from EcoVadis
- Sortera Technologies ‘owning and operating’ aluminum sorting solutions
- IDTechEx sees electric-powered construction equipment growth
- Global steel output recedes in November
- Fitch Ratings sees reasons for steel optimism in 2025
- P+PB adds new board members