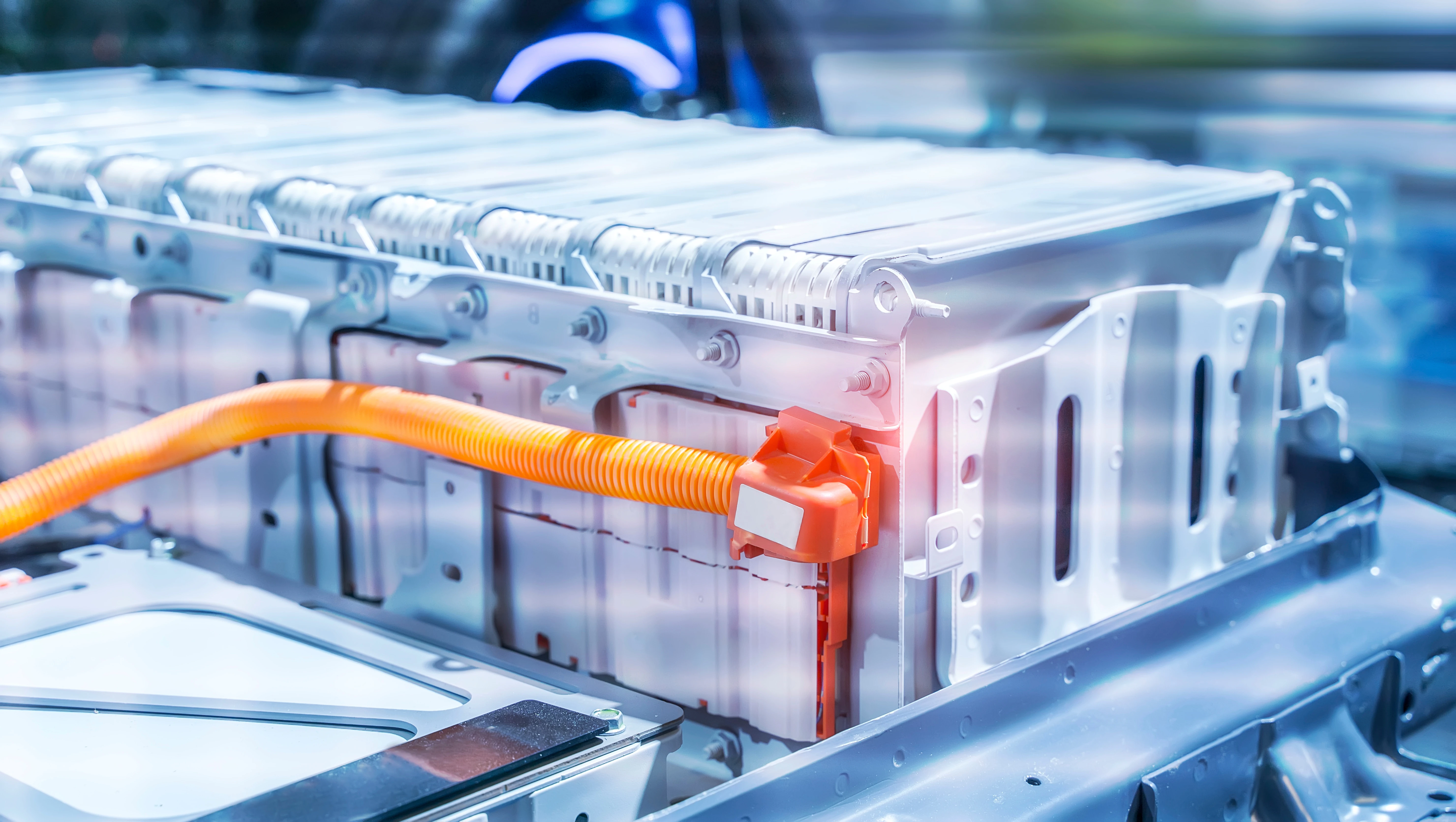
xiaoliangge | stock.adobe.com
Cox Automotive has opened its EV Battery Solutions (EVBS) service center in Conyers, Georgia, reflecting the rapid growth of the industry in Georgia, with EV facility investments from various automakers and battery manufacturers.
The company says it continues to grow its global EV battery service network, which measures more than 1 million square feet, to reflect its customer-first mindset.
“The geographic expansion of our EV battery service network reinforces our dedication to both our customers and the growth of the new and used electric vehicle market in the U.S.,” says Lea Malloy, assistant vice president of EV Battery Solutions, Cox Automotive, which is headquartered in Atlanta. “As the global leader of integrated battery caretaking services, we provide flexible capacity and logistics expertise that frees OEM resources to focus on new product development and customer engagement that is essential to further driving EV growth.”
Cox Automotive says it supports practices that enable the extension of EV battery first lives and end-of-life reuse and recovery treatments. This includes a variety of storage, logistics, diagnostics, repair and remanufacturing services being conducted at the company’s global EV battery service facilities in Oklahoma City, Oklahoma; Belleville, Michigan; Las Vegas; Conyers; Ede, Netherlands; and select Manheim operating locations. Manheim has more than 100 locations worldwide and provides a wholesale vehicle marketplace.
The company’s Conyers facility will be equipped with EV test equipment, lifting equipment and racks for battery storage, the company says. At full capacity, the facility can handle about 9,000 battery packs through various parts of the EV life cycle.
Conyers is the first EVBS facility to be on the East Coast, according to Cox Automotive, and provides logistical advantages to regional customers as EVBS looks to continue expanding to support its goals of maximizing the reuse and recycling of EV auto parts.
Battery packs will be received in the facility's approved Department of Transportation containers, according to the company. During the intake process, battery packs are inspected to ensure they are safe for processing. Any battery pack or container that is found to be defective immediately will be moved to the outside battery quarantine area. This includes battery packs or dunnage that show signs of physical damage, overheating or off-gassing and any battery packs or dunnage that have been pierced, dropped or crushed during material handling.
Latest from Recycling Today
- Turkish mills sampled wide scrap market in 2024
- GLE Scrap Metal acquires interest in Mallin Cos.
- 2024 marks strong year for Van Dyk
- Recycled metal portrayed as former dictator’s fiefdom
- Aqua Blaster takes aim at dust and fire suppression market
- Commentary: Merger opposition yields opponents of its own
- Textile recycler to open manufacturing facility in Vietnam
- Call2Recycle Canada, Ontario county achieve battery recycling milestone