
nosha | stock.adobe.com
Aluminum quickly is becoming the new metal of choice.
Because of its lightweight, durability and corrosion-resistant properties, aluminum has secured its place as an essential material in the modern automotive and construction industries. On an international scale, aluminum consumption is increasing, with key regional trends shaping demand:
- In Asia, China and India lead the world in aluminum consumption, accounting for 60 percent of the demand, with a 6-8 percent annual growth rate.
- In Europe, sustainability regulations are driving moderate consumption growth of 2-4 percent annually.
- In the United States, demand is rising by 3-5 percent per year, fueled by increased use of electric vehicles (EVs) and sustainable construction materials.
With sustainability becoming a growing priority, demand for secondary aluminum, or recycled aluminum, also is increasing give its 95 percent lower energy consumption than that of primary aluminum. However, despite its environmental advantages, secondary aluminum presents notable challenges, particularly in corrosion resistance. Impurities and alloying elements introduced during the recycling process can weaken its durability, making it less suitable for certain high-performance applications without proper surface treatment.
This year, it is crucial to examine aluminum’s expanding role, the industry’s shift toward secondary aluminum and the latest advancements in corrosion protection technologies designed to enhance its performance and longevity.
Aluminum in the automotive and construction industries
In the automotive industry, aluminum is rapidly emerging as a material of choice for EV design. Its lightweight properties help offset the added weight of EV batteries, improving overall efficiency.
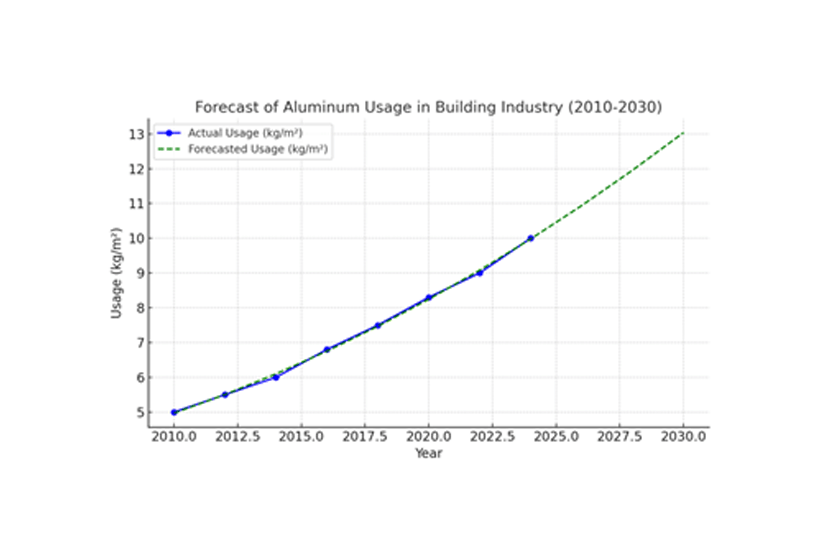
On average, EVs use 30 percent more aluminum than traditional vehicles, primarily in battery enclosures, body structures and lightweight components. This growing reliance on aluminum is driving demand, aligning with the industry’s push for energy-efficient and sustainable transportation solutions.
Beyond automotive applications, aluminum also plays a crucial role in the construction industry, where it is widely used in windows, facades, doors and structural elements. Its ability to reduce overall building weight and improve insulation has made aluminum a key material in energy-efficient building designs. As the industry seeks greener solutions to comply with evolving regulations, aluminum’s contribution to sustainable construction continues to grow and gain importance.
The shift to secondary aluminum
As the demand for aluminum has increased across the automotive and construction industries, recycled aluminum is becoming an attractive alternative to traditional solutions. Recycled aluminum offers environmental benefits, reduced manufacturing costs and energy savings during production.
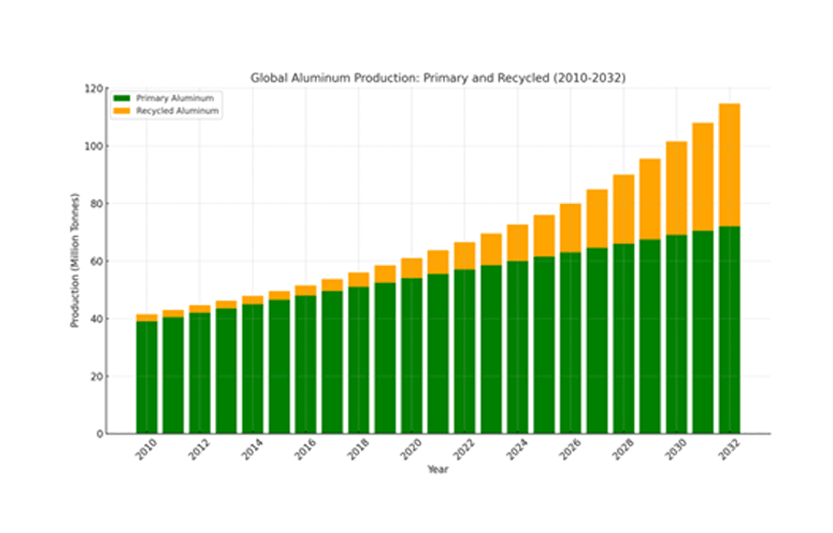
However, these advantages do not come without challenges, especially related to aluminum use in high-performance applications. Impurities and variations in alloy composition from the recycling process can compromise corrosion resistance and surface quality. To ensure long-term durability and aesthetic appeal, advanced protective treatments are essential.
New solutions have been developed to address these concerns, including advanced anodizing processes, trivalent chromium passivation and optimized conversion coatings. These technologies enhance corrosion resistance, improve aesthetic consistency and ensure secondary aluminum can meet the stringent demands of the automotive and construction industries.
Enhancing corrosion protection of recycled and difficult alloys
Secondary aluminum components are particularly vulnerable to uniform and filiform corrosion, both of which can compromise material integrity and longevity. Uniform corrosion affects the entire exposed surface, leading to gradual material degradation, while filiform corrosion spreads beneath protective coatings, weakening adhesion and compromising surface treatments. These issues are further exacerbated by the presence of intermetallic compounds, which have electronegativity differences that are more pronounced in secondary aluminum alloys.
To address these challenges, advanced surface protection technologies have been developed to enhance the durability and corrosion resistance of secondary aluminum:
- Trivalent chromium passivation (TCP) forms a robust and uniform protective layer containing zirconium (Zr) and trivalent chromium, providing superior corrosion resistance in harsh environments.
- Anodizing techniques strengthen aluminum by converting its natural oxide film into a thicker, more uniform aluminum oxide layer through an anodic current, improving surface hardness, chemical resistance and overall durability.
- Chromium-free (Cr-Free) conversion coatings improve resistance to environmental degradation while enhancing filiform corrosion protection under painted surfaces.
- Hybrid coating systems combine anodizing with advanced sealants or organic coatings to further enhance corrosion resistance, particularly for applications exposed to extreme conditions.
These advancements are critical for EV applications where long-term performance and material stability are essential. By implementing these solutions, secondary aluminum can become a viable and sustainable choice for high-performance industries.
Enhancing corrosion resistance in EN AC 46000 for EV battery enclosures
A recent study evaluated process developments mitigating the impact of alloying elements in aluminum, particularly for demanding applications like EV battery enclosures. EN AC 46000 was selected due to its high strength-to-weight ratio and excellent machinability. However, its high copper content, while beneficial for mechanical properties, significantly compromises corrosion resistance. An untreated EN AC 46000 sample exhibited severe degradation, lasting only eight hours in a neutral salt spray (NSS) test.
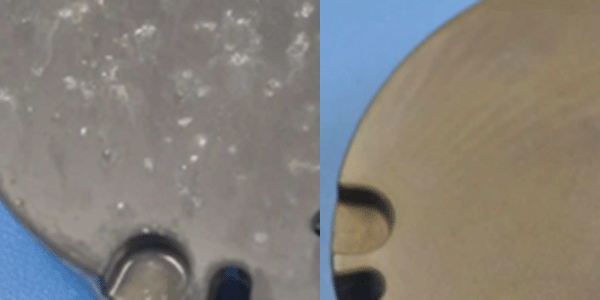
EN AC 46000 with Iridite TCP III process after 120 hours of NSS test
To address this issue, a specialized passivation system was applied to enhance corrosion resistance and electrical conductivity—critical factors for battery enclosures. The Iridite TCP III process significantly improved corrosion resistance, extending NSS test performance to 120 hours. However, samples exposed to 240 and 480 hours of NSS testing still exhibited substantial corrosion, highlighting the need for further optimization.
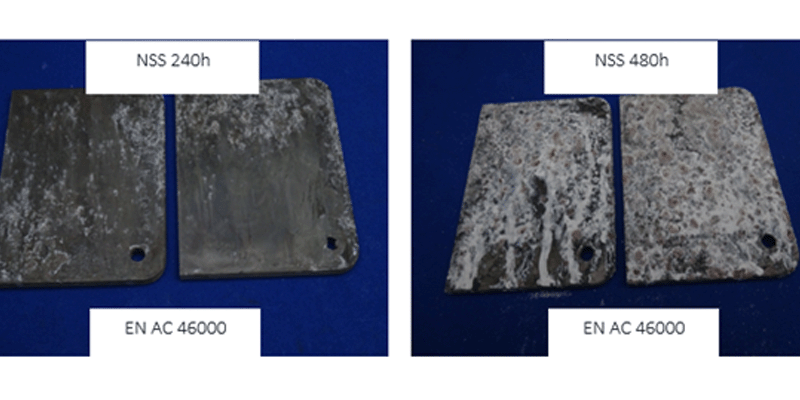
To further enhance corrosion protection, an additional postdip treatment using Iridite Cor-Guard 40 was introduced. This treatment increases surface hydrophobicity, reducing the contact time of the corrosive media with the aluminum surface. As a result, corrosion resistance improved significantly, with treated samples maintaining their protective properties for up to 480 hours in NSS tests. These results, shown in Figure 6, confirm the extended service life of treated EN AC 46000, even under the harsh conditions expected in real-world EV applications.
Looking ahead
As the global demand for aluminum rises and sectors such as automotive and construction push for more sustainable solutions, it remains a material of choice due to its lightweight strength and durability. The growing use of secondary aluminum has introduced both benefits and challenges, requiring advanced surface treatment technologies to maintain performance and longevity.
Sponsored Content
Redefining Wire Processing Standards
In nonferrous wire and cable processing, SWEED balances proven performance with ongoing innovation. From standard systems to tailored solutions, we focus on efficient recovery and practical design. By continually refining our equipment and introducing new technology, we quietly shape the industry—one advancement at a time.
Sponsored Content
Redefining Wire Processing Standards
In nonferrous wire and cable processing, SWEED balances proven performance with ongoing innovation. From standard systems to tailored solutions, we focus on efficient recovery and practical design. By continually refining our equipment and introducing new technology, we quietly shape the industry—one advancement at a time.
Sponsored Content
Redefining Wire Processing Standards
In nonferrous wire and cable processing, SWEED balances proven performance with ongoing innovation. From standard systems to tailored solutions, we focus on efficient recovery and practical design. By continually refining our equipment and introducing new technology, we quietly shape the industry—one advancement at a time.
Sponsored Content
Redefining Wire Processing Standards
In nonferrous wire and cable processing, SWEED balances proven performance with ongoing innovation. From standard systems to tailored solutions, we focus on efficient recovery and practical design. By continually refining our equipment and introducing new technology, we quietly shape the industry—one advancement at a time.
Sponsored Content
Redefining Wire Processing Standards
In nonferrous wire and cable processing, SWEED balances proven performance with ongoing innovation. From standard systems to tailored solutions, we focus on efficient recovery and practical design. By continually refining our equipment and introducing new technology, we quietly shape the industry—one advancement at a time.
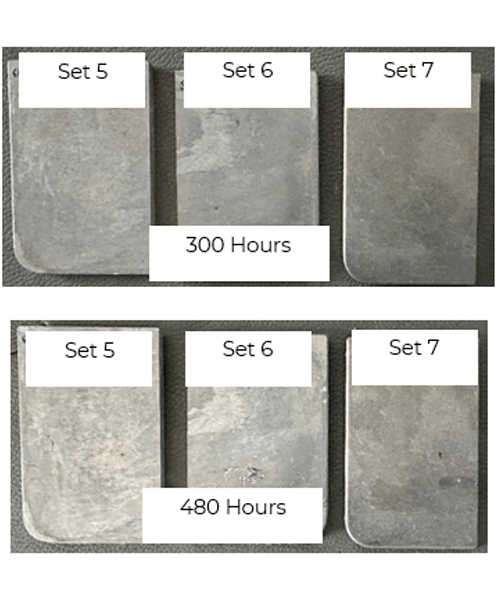
Cor-Guard 40 as postdip process after 300
and 480 hours of NSS test
To address these challenges, innovative solutions such as trivalent chromium passivation, anodizing optimizations, and advanced conversion coatings have proven highly effective. Corrosion resistance is influenced by both material composition and surface preparation, making it essential to develop tailored treatment strategies for each aluminum application.
Looking ahead, continued research into emerging protective technologies, including nanocoating and self-healing layers, has the potential to further improve the performance of recycled aluminum in demanding applications. Collaboration across industries, bringing together material scientists, manufacturers and regulatory bodies, will be key to establishing best practices and standards for maximizing aluminum’s sustainability and performance.
With ongoing advancements in corrosion protection and alloy optimization, secondary aluminum is positioned to play an increasingly vital role in shaping a more sustainable future for manufacturing while meeting the evolving demands of modern industries.
Dr. Can Akyil is the light metal solutions global business director at Waterbury, Connecticut-based MacDermid Enthone Industrial Solutions, and Dr. Pinar Afsin is its global technology leader of research and development. Learn more here.
Get curated news on YOUR industry.
Enter your email to receive our newsletters.
Latest from Recycling Today
- Steelmakers await impact of tariff policy
- Radius loses money, says merger on track
- Electrostatic technology vies for role in ASR sorting
- ReMA board to consider changes to residential dual-, single-stream MRF specifications
- Trump’s ‘liberation day’ results in retaliatory tariffs
- Commentary: Waste, CPG industries must lean into data to make sustainable packaging a reality
- DPI acquires Concept Plastics Co.
- Stadler develops second Republic Services Polymer Center