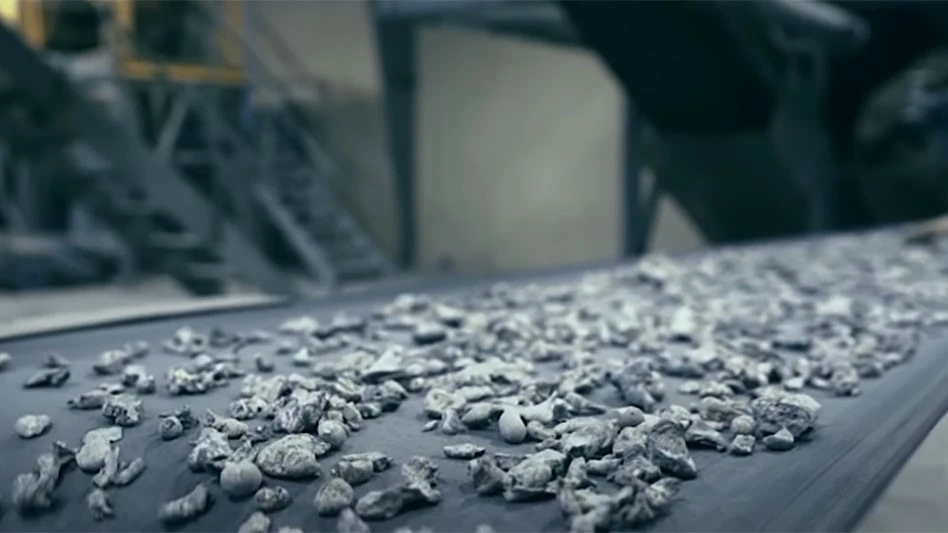
Photo courtesy of Constellium
Constellium SE, headquartered in Paris, has announced that it is leading a new consortium of automakers and suppliers to develop lower-carbon, lower-cost aluminum extrusion alloys by maximizing the use of postconsumer scrap.
The 10 million pounds sterling, or $12.2 million, CirConAl (Circular and Constant Aluminum) project is sponsored by a grant from the U.K.’s Advanced Propulsion Centre (APC). It aims to maximize the use of postconsumer scrap in a new generation of high-strength alloys that emit less than 2 tons of CO2 per ton of aluminum produced, Constellium says.
According to the company, by designing, developing, prototyping and testing aluminum automotive components at scale, the project is expected to demonstrate that high-strength alloys with high recycled content can meet or exceed original equipment manufacturer (OEM) requirements for strength, crushability, durability as well as other performance criteria.
The partners also will develop scrap sorting technologies to ensure that valuable metal is recycled into new automotive solutions rather than downcycled, Constellium says, preserving its value and contributing to a circular economy.
“Low-carbon solutions require collaboration across the supply chain, and Constellium is proud to lead the CirConAl project in partnership with the APC, automakers and suppliers as the industry works toward carbon neutrality,” says Philippe Hoffmann, president of Constellium’s Automotive Structures & Industry Business Unit. “Taking advantage of Constellium’s high-strength HSA6 aluminum extrusion alloys, as well as new scrap sorting and blending technologies, we expect this next generation of alloys to provide automakers with ultra-low embodied CO2 material to drastically reduce the carbon footprint of their products.”
The company says aluminum extrusions and components for the CirConAl project will be prototyped and tested at its University Technology Center (UTC) at Brunel University London. The UTC is a center of excellence for the development of aluminum crash management systems and body structure components, as well as for battery enclosures for electric vehicles. Its industrial scale casting and extrusion equipment allows for rapid prototyping, reducing development times by at least 50 percent for the advanced alloys required to lightweight automotive components, Constellium adds.
The company says it has committed to reaching a 30 percent reduction in its carbon emissions intensity by 2030 (Scopes 1, 2 and 3) compared with 2021 and pledged that at least 50 percent of all aluminum Constellium uses will be from recycled sources by 2030. The company recently joined the First Movers Coalition, a global coalition to decarbonize hard-to-abate sectors, and is a founding member of the Aluminum Stewardship Initiative, aglobal nonprofit standards-setting and certification organization.
Latest from Recycling Today
- ReMA offers Superfund informational reports
- Hyster-Yale commits to US production
- STG selects SolarPanelRecycling.com as exclusive recycling partner
- Toyota receives $4.5M to support a circular domestic supply chain for EV batteries
- Greyparrot reports 2024 recycling trends
- Republic Services opens Colorado hauling facility
- ABTC awarded $144M DOE grant
- Massachusetts awards $4 million in waste and recycling grants