
Photo courtesy of Cirba Solutions
In David Klanecky’s view, the growing use of electric vehicles (EV) presents a once-in-a-lifetime transformation for the United States’ transportation system.
As the CEO of Charlotte, North Carolina-based battery recycler Cirba Solutions, his goal is to help push that transformation forward.
“I’m just excited about the space,” he says. “How we move people and goods around the country is going to be electrified. That’s pretty exciting. Being a part of that is just very unique, and the growth that our company is seeing and going to see in the future is also kind of a once-in-a-lifetime opportunity.”
RELATED: Cirba Solutions embarks on community education effort
Since Cirba Solutions was formed in 2022 through the merger of three experienced battery recycling companies in Retriev Technologies, Battery Solutions and Heritage Battery Recycling, the company has positioned itself at the forefront of the industry in terms of lithium-ion battery (LIB) recycling.
The company boasts seven facilities throughout the U.S. and Canada; has developed numerous feedstock partnerships with companies that include automaker Toyota, retailer Batteries Plus and recycling organization Call2Recycle; and has built a robust logistics network for safely transporting material to its processing facilities.
Cirba Solutions has been recognized for its efforts. Since 2022, the company has received approximately $82 in grant funding from the U.S. Department of Energy (DOE) through the Bipartisan Infrastructure Law (BIL), as well as about $295 million in investments from firms including Japan-based Marubeni Corp. and Sweden-based EQT Infrastructure that it is using to upgrade existing facilities and build new ones. It is in the process of a more-than $200 million upgrade at its recycling facility in Lancaster, Ohio, and is in the early stages of developing a flagship facility in Richland County, South Carolina.
Klanecky says all this work is in the service of keeping the batteries consumers use every day away from landfills once they reach end of life and, instead, extracting the critical materials, which include lithium, cobalt, nickel and manganese and recycling them to recover these critical materials for use in new products.
“We’ve got the largest operating mine in the world driving around on our streets every day,” he says. “People talk about mining and digging holes in the ground and all the things we’ve got to do because we’ve got to get those metals. But the biggest mine today operating in the world is actually driving around the streets, and it’s our job at Cirba to make sure that material gets into our facility, gets reprocessed and reused again.”
Growth period
Cirba Solutions claims 30 years of battery recycling experience and has serviced more than 7,000 customers while recycling hundreds of millions of pounds of batteries over the course of its history. The company’s facilities are in Wixom, Michigan; Mesa, Arizona; Baltimore and Lancaster, Ohio; Brea, California; Trail, British Columbia; and Eloy, Arizona.
Currently, the company is working to greatly increase its capabilities.
In August 2023, Cirba Solutions began expanding its LIB processing facility in Lancaster. The more-than $200 million project has been aided in part by an $82 million grant through the DOE’s Office of Manufacturing and Energy Supply Chains—the first such grant awarded by that office. The funding is part of the first phase of more than $7 billion in total funding provided through the BIL.
RELATED: Cirba Solutions and Jacobs partner to build out battery materials facilities
Previously, the facility processed all types of battery chemistries, including nickel-based and lead-acid batteries, before a 2013 expansion into lithium-ion. After the current expansion is complete, the company says the facility will be one of the largest of its kind in North America, capable of producing enough battery-grade raw materials to power more than 200,000 new EVs annually while creating about 150 new jobs.
The facility is scheduled to begin operations in three phases. Klanecky says the first, slated for August, will increase its capability to process batteries and create black mass. The second phase, planned for April 2025, will expand the black mass extraction further, and the third, slated for the end of 2025, will include Cirba Solutions’ hydrometallurgical process, where it will be able to extract nickel, lithium, cobalt and manganese from black mass and purify it to battery-grade quality to sell back into the supply chain.
“We’re on track and our timelines are still intact, and we’re spending a lot of money there," Klanecky says of the Lancaster plant. “The investment in Lancaster is probably going to be over $350 million, which is a pretty big investment for that site and for that area.
“The city and the state, everybody’s excited about that. It puts Ohio on the map. It puts Lancaster on the map, too, from a battery supply chain perspective. It [creates] 150-plus really good jobs in that facility, which is great. It can be an economic driver for the community and for the people that live there.”
In March 2023, Cirba announced an initial investment of more than $300 million to build its eighth facility, a lithium-ion EV battery recycling flagship site in the Pineview Industrial Park in Richland County, South Carolina. The facility will be located strategically in the U.S. “Battery Belt,” an area between Michigan and Georgia where more than 15 new LIB gigafactories or expansions have been announced since 2021.
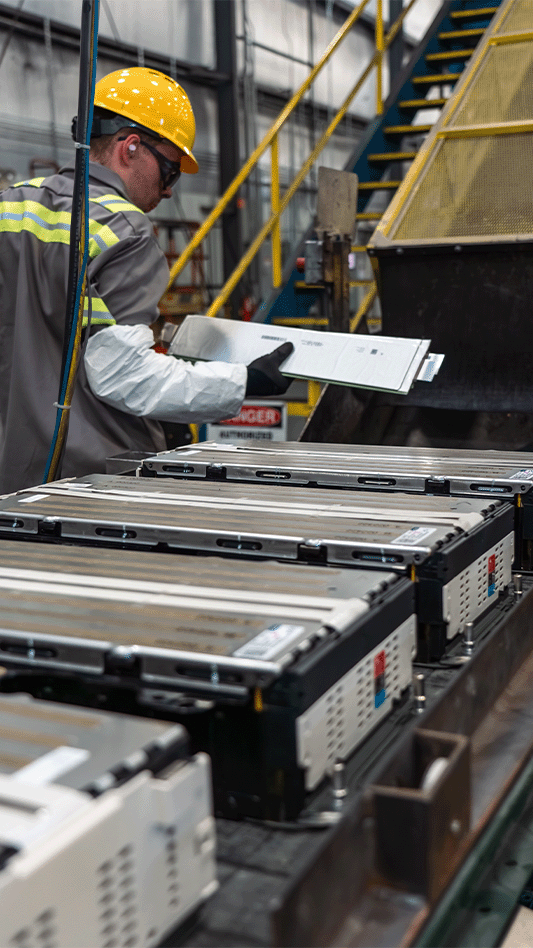
At the time of Cirba Solutions’ announcement, county documents showed the facility will sit on approximately 206 acres of the industrial park and create 310 jobs.
Klanecky says the company is in the process of securing all of the necessary permits, and construction is likely to begin in 2025. He estimates the facility will begin operations by 2027 or early 2028 and, when operating at full capacity, will be capable of providing enough battery-grade materials to power more than 500,000 EVs annually.
“We’re pacing it with the market,” he says of the construction process, adding that the company doesn’t want to rush while it also is working to get the Lancaster site online.
“We want to make sure that we’re successful in Lancaster and not spread ourselves too thin in terms of the resource constraints that we have and just making sure we’re doing the right thing in terms of starting these assets up. I’ve got one engineering team, one technology team, and spreading them between two different sites was going to be a challenge, and we realized that early on.”
Klanecky adds that there’s a lot of excitement about the Richland County site internally. “There will probably be some new technology that we’ll implement there," he says. "We’re working on that right now in terms of our design phase of that project, and the state of South Carolina has been extremely helpful, like Ohio has as well.”
Cirba likely is not stopping its expansion after the South Carolina facility is built, Klanecky says, noting the company has a five-to-10-year strategic plan that factors in which regions of the U.S. make the most sense logistically, which states are likely to have the most end-of-life batteries coming online in the coming years and where gigafactories are being built.
Cirba Solutions is considering areas west of the Battery Belt, where states in the Midwest and on the West Coast, such as California, will eventually have a high number of EV batteries reaching end of life.
“I would venture to guess that our footprint is going to move west next,” Klanecky says. “We’re looking at a number of different locations already out there as the next phase of our build-out. and we’re talking with the states out in that region just to understand what the best options are for us.”
When looking for a potential facility site, Klanecky says Cirba Solutions considers the workforce, making sure “we’ve got the right people to be able to start the facility up and keep it running.” Also, Cirba Solutions looks at a location’s proximity to its customers, whether battery and manufacturing scrap generators or companies needing battery materials.
For the rest of this year, Klanecky says the company’s main focuses are continuing to operate its facilities safely while upgrading, starting up the upgraded Lancaster facility and looking at long-term expansion opportunities.
“We want to make sure we’ve got the right partnerships with our customers,” he says. “In order for us to grow, we’ve got to make sure that we’ve got not only the front end of our business solidified in terms of being able to find feedstock, whether it’s with auto manufacturers, battery cell manufacturers or even cathode producers to some extent, because there’s a lot of material we want to bring into the process.
“But then it’s also making sure that we’ve got the right partnerships downstream to have a successful business model going forward. So, it’s safety, it’s asset build-out and it’s making sure we’ve got the right customer relationships.”
Logistics leader
One area Cirba Solutions prides itself on is its logistics platform, which Klanecky says is an industry leader.
Developed with the help of systems previously used at Retriev and Battery Solutions, Cirba Solutions has its own fleet of 16 trucks, 25 trailers and a team of drivers who travel across North America daily to collect batteries for processing.
Additionally, Klanecky says the company has access to about 300 “virtual warehouses,” or aggregation centers it uses to fill truckloads and move them to its recycling facilities cost-effectively. The Heritage Group, which also has a number of waste management companies in its portfolio with the capability of handling hazardous waste, gives Cirba Solutions access to its network of about 1,200 trucks throughout North America.
“We’ve got partnerships with those companies within The Heritage Group, and they work with us on [collection],” Klanecky says. “They’ll say, ‘Hey, there’s a bunch of batteries here. We’re going to aggregate them.’ And then we work on getting them to our facilities as well. That gives us another virtual 1,200 trucks that we can use when we need them to be able to collect material and bring it to our facilities.”
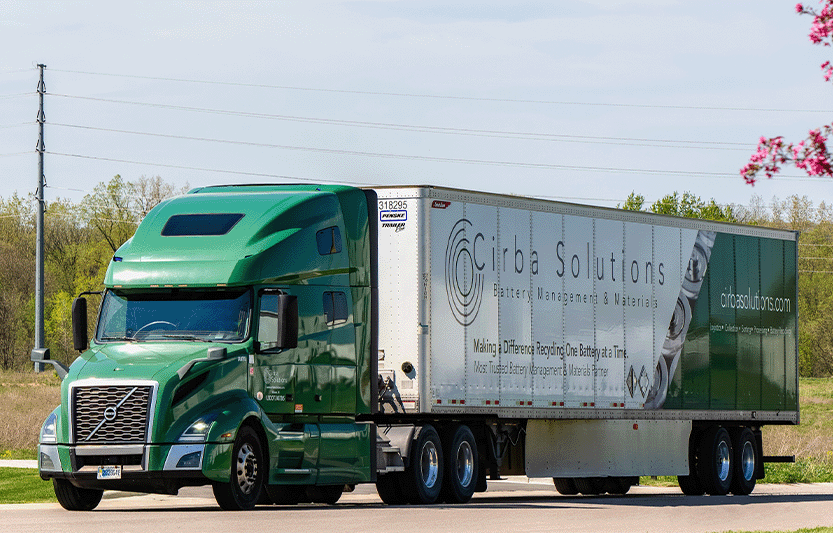
With drivers on the road carrying loads of batteries that can be extremely hazardous, Cirba Solutions places a premium on training and safety for its drivers and customers.
“When you’ve got lithium-ion batteries, there’s always a risk of a thermal event,” Klanecky says. “Safety starts with packaging. We try to educate our customers on packaging and make sure that they’re packaging these materials safely. … It really starts at that education piece on packaging.”
Cirba Solutions' drivers also receive special training and trucks are outfitted with safety devices to ensure a potential thermal event can be under control within seconds. The company’s trucks use a specially designed sensor to track thermal profiles or smoke. Once the sensor is activated, Klanecky says a system kicks in that removes all oxygen from the trailer, denying a potential fire a key fuel source.
“We pay a lot of attention to the safety of transporting the materials, the safety devices we have in our trucks and the training that all of our drivers get on a regular basis,” he says.
Fast-moving industry
Klanecky says in the last five years, the battery recycling industry has really taken off, with numerous new recycling companies entering the picture, spurred by federal and private investment and a desire to build a domestic supply chain for battery materials.
“The new car sales, EVs still are growing rapidly in North American and, really, globally,” he says. “China is obviously taking a massive leap forward with what they’re trying to do in terms of electrification there, and Europe’s catching up real fast. In the U.S., we have a lot of [investment] encouragement from the Department of Energy [and] Department of Defense. ... North America is also kind of accelerating that growth.
“For our company, that’s great, because we’ve got a lot of experience in how we process batteries, and we’ve been processing lithium-ion batteries since 2009. Our facilities have been built to do that. It’s just been a lot of consumer devices and smaller batteries. But now we’re getting more volume with EV batteries and gigafactory scrap material that needs to be recovered.”
Because of the combined experience of the three companies that merged to form it, Cirba Solutions claims a head start of sorts in terms of logistics, packaging and processing know-how.
Klanecky says the pace of the industry’s development is only going to get faster.
“I would say it’s like we’re in a baseball game,” he says. “We’re in the first inning of a game that’s going to go into extra innings, most likely, and we’re running a 100-meter-dash pace in a marathon. We’ve got to make sure this is a sustainable industry that’s going to continue to build going forward. … It’s going to see its cycles because you’re building a manufacturing base in North America. That doesn’t happen smoothly; there’s chunks of volume that come on. We’re just trying to make sure that we’re working really closely with our customers and prepare ourselves for that.”
He says Cirba is motivated and excited to work toward building a domestic supply chain for batteries.
“[Our employees] have purpose," he continues. "You give them a purpose, you give them some goals of what we want to achieve every year, and everybody’s pretty motivated.”
Get curated news on YOUR industry.
Enter your email to receive our newsletters.
Latest from Recycling Today
- Fenix Parts acquires Assured Auto Parts
- PTR appoints new VP of independent hauler sales
- Updated: Grede to close Alabama foundry
- Leadpoint VP of recycling retires
- Study looks at potential impact of chemical recycling on global plastic pollution
- Foreign Pollution Fee Act addresses unfair trade practices of nonmarket economies
- GFL opens new MRF in Edmonton, Alberta
- MTM Critical Metals secures supply agreement with Dynamic Lifecycle Innovations