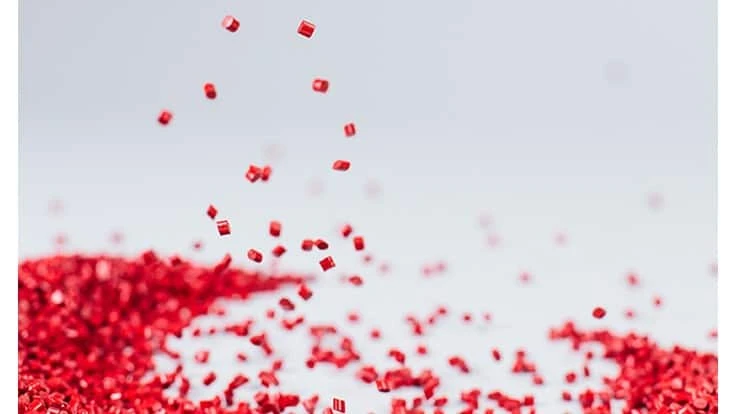
© Yauhen Leukavets - stock.adobe.com
Researchers at Case Western Reserve University (CWRU), Cleveland, say they have developed a new technology to recycle rigid, long-lasting plastics used in cars, planes, wind turbines and other industrial uses. Using the new technology, end-of-life thermoset plastics can be broken down into a reusable resin.
Ica Manas-Zloczower, a professor in CWRU’s Department of Macromolecular Science and Engineering, and her postdoctoral researcher Liang Yue are leading research and development on the new technology. The technology aims to increase the types of plastics that are recyclable and, therefore, reduce the amount that ends up in landfills or are directed to energy conversion processes.
While soft thermoplastics can be highly recyclable, thermoset polymers—used in applications in the automotive, aerospace and wind industries that require strength and light weight—are built to be durable and cannot be recycled easily by conventional methods, such as by being dissolved in a solvent or melted.
Manas-Zloczower and Yue’s research has uncovered a new way to take rigid thermoset plastics and reprocess them to remake the original product or to make new products.
“There’s two types of plastic; one is thermoplastic,” Yue says. “Thermoplastic can be recycled and reshaped. It can be used as a daily product like bottles—those types of materials. Thermoset is another type of plastic. They cannot be recycled because they have a cross-link structure. Those types of materials [thermosets] have very good mechanical properties, [such as] chemical resistance. They are used in the engineering field as structure materials like a wind turbine blade or even aerospace [applications]—which require very high mechanic[al] properties.”
Manas-Zloczower and Yue say they are solving this problem by converting permanent, cross-linked structures into dynamic cross-linked ones.
The dynamic cross-linked network allows reshaping and reprocessing by conventional methods, such as hot-press molding or injection molding, to fabricate a new product with comparable or better value.
In 2018, while working at Manas-Zloczower’s Case School of Engineering Lab, Yue started questioning how thermoset plastics could be made more recyclable. He sought to find a way to obtain “a closed loop of recycling” in order to achieve sustainability and reduce pollution. Yue says he started research to see the feasibility of recycling the thermoset and then developed this technology with Manas-Zloczower.
The new solvent-assisted process called “vitrimerization” transforms the thermoset plastic into a new class of materials known as vitrimer polymers, which can be reformed and reprocessed.
The next step the team is discussing with industrial partners is a process known as “mechanochemical ball-milling” to produce tons of reusable powder resin, with no solvent involved.
Yue says, “So far, those power resins we have recycled, we made in [the] lab and they are pure, so there's no additives. In reality, in the industry application, when we use those types of thermosets, you really have to [have] some additive—cotton fiber, glass fiber—as a reinforcement.”
Manas-Zloczower adds that fillers will allow the material to have “properties tailored to various applications.” In this way, “We can expand the range of applications depending on the properties which you get in the vitrimerized thermoset.”
“We want to start to see how those fibers will affect recycling. So, with this technology, it may take some time to figure out how can we more efficiently recycle those thermoset[s] with this fiber inside. So, that’s our next step. If we can solve this problem with the fiber inside, then we can push this technology to the market,” Yue says.
Looking to the future of thermoset recycling, Yue adds, “This technology can be further promoted to other cross-link thermoset[s] like rubber, which is also another big problem. So, with this concept, we want to further develop this or further promote this technology to apply to other chemistry.”
Eventually, the researchers want all thermosets to be recyclable, but technological problems must still be addressed in the lab before this goal can be reached.
Regarding her research, Manas-Zloczower comments, “I think it will have a tremendous impact if this technology is going to be expanded to an industrial scale. Because—just imagine all the material, all the thermoset [material] that is currently in the U.S. and worldwide— if we can actually use that thermoset for other purposes, not to end up in the landfill, this will be tremendous. And not to mention that those vitrimerized thermosets can be recycled more than one time. So, you make a material and then you can recycle it again, maybe not for the same purpose, but for a different purpose.”
Manas-Zloczower says their work over the last two years was funded in part by the National Science Foundation. She and Yue are working closely with the Great Lakes Energy Institute and the CWRU Office of Technology Transfer to identify potential industry partners, research funders or investors to take the next steps toward fully testing the process at industrial scale.
Latest from Recycling Today
- Aluminum Association seeks certainty on tariffs
- EPA plans to revisit numerous environmental, climate regulations
- Scientists use air, inexpensive catalyst to break down plastic
- Miami-Dade Innovation Authority launches fifth Public Innovation Challenge
- EVSX installation supported by Call2Recycle Canada
- Wendt commissions shredding plant, nonferrous system at Island Recycling
- Fornnax wins Green Innovation of the Year award
- Recyclers opening doors to the public through APR program