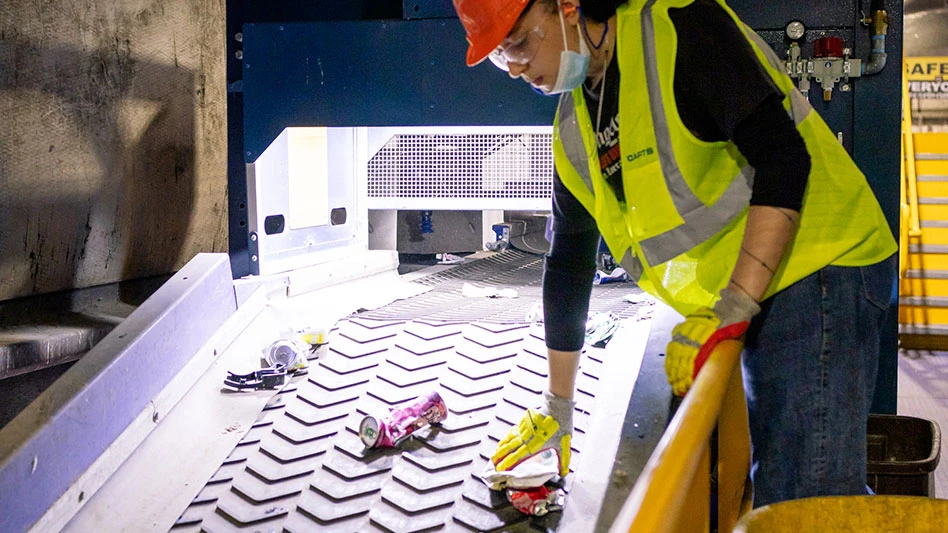
Photo by Backstory Creative
According to research from the Can Manufacturers Institute (CMI), Washington, up to 1 in 4 used aluminum beverage cans (UBCs), or 25 percent, is missorted at a typical material recovery facility (MRF). As a result, MRFs cannot maximize their revenues, and the aluminum industry is struggling to reach its targeted UBC recycling rates of 70 percent by 2030 and 90 percent by 2050.
The CMI says accurate sorting at MRFs could increase the U.S. recycling rate by 3 percent. Therefore, as part of its strategy to increase UBC recycling, the CMI is working to improve technology at MRFs to capture more missorted cans. The organization’s beverage can manufacturer members Ardagh Metal Packaging and Crown Holdings have funded grants for can-capture equipment, while CMI also has introduced a leasing model that involves revenue sharing to help MRF operators invest in sorting equipment.
CMI analyzed UBC sorting at five loss points across three diverse MRFs, with UBC losses averaging between seven to 36 cans per minute at each point, which is equivalent to an average annual revenue loss of $71,940.
In September of last year, CMI initiated a project to fund an EverestLabs robot at Caglia Environmental's Cedar Avenue Recycling and Transfer Station (CARTS) MRF in Fresno, California.
In early 2021, Caglia retrofitted its CARTS MRF with a new processing line capable of handling 25 to 35 tons per hour supplied by San Diego-based CP Group. That retrofit included a new metering box, an auger screen, an anti-wrapping screen, an OCCScreen, a CPScreen, two FiberMax optical sorters, two PlasticMax optical sorters, a barrel magnet and an eddy current.
CMI provided financing for a two-year lease on a robot that was placed on the “last chance line” at the CARTS MRF with funding from Ardagh Metal Packaging and Crown Holdings. In return, Caglia agreed to share 50 percent of the revenue generated from the UBCs collected by the robot.
“CMI paid upfront the full cost of the two-year lease,” EverestLabs CEO JD Ambati says, noting CMI plans to use the revenue received through the revenue-sharing model to finance can-capture equipment in other MRFs.
Caglia estimates, based on previous analyses, that EverestLabs’ robot could capture 32,000 pounds of UBCs per year that otherwise would have gone to landfill. This is equivalent to collecting a little more than 1 million UBCs per year, or roughly three UBCs per minute of operation. Caglia will share with CMI 50 percent of all revenue from the cans collected via the leased robot, including the revenue from the sale of the UBCs and the revenue from California’s beverage container recycling refund program.
The EverestLabs’ robot is equipped with advanced artificial intelligence, or AI, and a 3D depth-sensing camera and was selected because technologies can be deployed within a few hours with no downtime or retrofits. Additionally, its performance would be tracked around the clock by professional monitors, and it would provide minute-by-minute data on the material types coming across the line.
“It took a week to install, calibrate and fine-tune the models,” Ambati says of the technologies’ installation at CARTS.
When no UBCs are present on the last-chance line, the technology can prioritize picking other containers that were missed, further increasing material recovery.
CMI says a key reason this lease model is successful is because EverestLabs provides robotics performance analytics to Caglia and CMI, providing a daily view on the value recovered and data on the UBCs and containers that were missed and information on the progress of the lease payback.
“Right now, EverestLabs provides CMI and Caglia with data on robot performance and a daily view on the volume and value of UBCs on their residue line and the value and volume of UBCs recovered,” Abati says. “We also provide them with information on GHG [greenhouse gas] emissions prevented by not landfilling and mining for virgin material production.
“EverestLabs customizable dashboards allow our customers to choose which data they would like to see. This could include material characterization, line performance assessments, measuring bale quality, value lost to landfill, material volume and value recovered, etc.”
“EverestLabs’ real-time and easy-to-use analytics platform, alongside an easily retrofittable robotic cell with zero disruptions and guaranteed highest recovery in the industry, ensures all possible UBCs are recovered,” adds Corey Stone, plant manager at Caglia Environmental. “With CMI wanting to recycle more aluminum beverage cans and Caglia becoming a recycling industry leader, this program is a win-win for everyone.”
Sponsored Content
Labor that Works
With 25 years of experience, Leadpoint delivers cost-effective workforce solutions tailored to your needs. We handle the recruiting, hiring, training, and onboarding to deliver stable, productive, and safety-focused teams. Our commitment to safety and quality ensures peace of mind with a reliable workforce that helps you achieve your goals.
According to CMI and EverestLabs, the AI and robot are recovering an average of 1,565 UBCs per day, reducing the volume of waste sent to landfills and generating revenue for Caglia and CMI. The additional UBC recovery saves an average of 671.4 kilowatt-hours of energy per day, which is equivalent to the energy needed to power a U.S. home for 618 hours.
CMI plans to use information from this initiative to support additional UBC capture equipment at MRFs, further enhancing the recycling industry's efficiency. CMI and EverestLabs are now looking to expand their partnership and are exploring placing a robotic system in another MRF.
“What happens with the robot after the two-year lease is up will be decided closer to when it is up,” Abati says of the EverestLabs RecycleOS AI and robotics platform installation at Caglia.
Get curated news on YOUR industry.
Enter your email to receive our newsletters.
Latest from Recycling Today
- AF&PA report shows decrease in packaging paper shipments
- GreenMantra names new CEO
- Agilyx says Styrenyx technology reduces carbon footprint in styrene production
- SABIC’s Trucircle PE used for greenhouse roofing
- Hydro to add wire rod casthouse in Norway
- Hindalco to invest in copper, aluminum business in India
- Recycled steel price crosses $500 per ton threshold
- Smithers report looks at PCR plastic’s near-term prospects