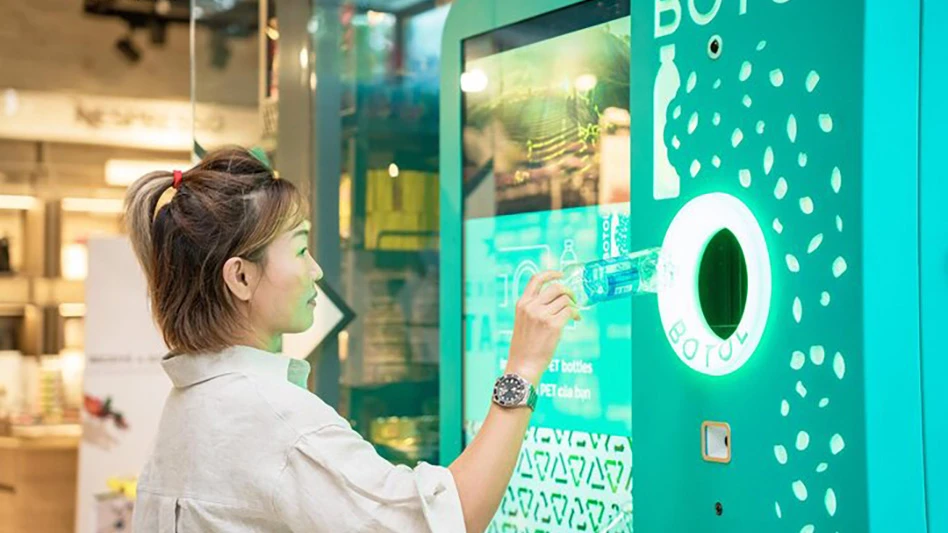
Photo courtesy of Vietnam Multimedia Corp. and Greencore Resources Ltd.
Recycling industry veteran Max Craipeau, CEO of Singapore-based Greencore Resources Ltd., is offering a reverse vending machine (RVM) to the Asian market designed to efficiently handle the recycling of polyethylene terephthalate (PET) beverage containers.
Greencore and Craipeau have long focused on PET, specifically with an eye on diverting ocean-bound PET into an established recycling and processing systems.
In addition to running a processing plant and engaging in global trading of reprocessed PET, Craipeau committed to increasing collection of the material—and helping divert it from the environment and the ocean—in the Southeast Asia region where he lives and works.
The commitment involved the design and manufacturing of an RVM branded as Botol that Craipeau says he has successfully tested and placed in Vietnam, with efforts in Indonesia and other nations nearly ready to launch.
Craipeau says the word “botol” is found in some languages used in Indonesia and other Southeast Asian countries as an approximation of the English word bottle, showing “it is a word understandable by everyone globally.”
In October, Botol hosted a media event at a grocery store in Ho Chi Minh City, Vietnam, to introduce the Botol RVM to that market.
“I am happy to say, the media showed a great deal of interest, with one publication writing, ‘The Botol advanced RVM machine aims to create local jobs and promote economic growth through encouraging recycling,'” Craipeau tells Recycling Today.
Craipeau says the current plan is to have 100 to 200 Botol machines operating in and near Ho Chi Minh City by the middle of next year. “If we can build them, Vietnam will provide a home for them,” he says. The Botol machine, in addition to focusing exclusively on PET bottles, offers extended producer responsibility- (EPR-) linked identification technology, Craipeau says.
The Botol RVM includes internal shredding and sorting technology designed to increase the cost-effectiveness of transporting lightweight PET while safeguarding quality, he adds. (Although the machines focus on PET, they also can accept aluminum used beverage cans, or UBCs.)
Transporting PET bottles that are shredded immediately, rather than carrying unshredded bottles filled with air, can reduce the number of trucks needed to haul the same volume of bottles from 10 trucks to one, Craipeau calculates.
Regarding quality, Craipeau says the machine can create sorted (separated by clear, blue and green) materials that, with minimal additional processing, meet U.S. Food and Drug Administration (FDA) standards for food-contact material. This includes removing any polyvinyl chloride (PVC) that could contaminate the stream.
Sponsored Content
Labor that Works
With 25 years of experience, Leadpoint delivers cost-effective workforce solutions tailored to your needs. We handle the recruiting, hiring, training, and onboarding to deliver stable, productive, and safety-focused teams. Our commitment to safety and quality ensures peace of mind with a reliable workforce that helps you achieve your goals.
Sponsored Content
Labor that Works
With 25 years of experience, Leadpoint delivers cost-effective workforce solutions tailored to your needs. We handle the recruiting, hiring, training, and onboarding to deliver stable, productive, and safety-focused teams. Our commitment to safety and quality ensures peace of mind with a reliable workforce that helps you achieve your goals.
Sponsored Content
Labor that Works
With 25 years of experience, Leadpoint delivers cost-effective workforce solutions tailored to your needs. We handle the recruiting, hiring, training, and onboarding to deliver stable, productive, and safety-focused teams. Our commitment to safety and quality ensures peace of mind with a reliable workforce that helps you achieve your goals.
Sponsored Content
Labor that Works
With 25 years of experience, Leadpoint delivers cost-effective workforce solutions tailored to your needs. We handle the recruiting, hiring, training, and onboarding to deliver stable, productive, and safety-focused teams. Our commitment to safety and quality ensures peace of mind with a reliable workforce that helps you achieve your goals.
Sponsored Content
Labor that Works
With 25 years of experience, Leadpoint delivers cost-effective workforce solutions tailored to your needs. We handle the recruiting, hiring, training, and onboarding to deliver stable, productive, and safety-focused teams. Our commitment to safety and quality ensures peace of mind with a reliable workforce that helps you achieve your goals.
In terms of forging alliances, Craipeau says he has developed a business-to-business model “where we can lease, sell, and/or jointly operate the [RVM] fleet in countries” with a partner. Partners can include brand owners, supermarkets, petrochemical companies and other recycling firms.
Craipeau says that while the machines have been designed to work within EPR systems, that is not a necessary precondition—and, in fact, the Botol devices can help gather data leading up to EPR implementation.
Botol is in its early stages, Craipeau says, adding, “We have lots of demand and, and after an oversubscribed pre-seed round with industry titans, we are now organizing our seed round, which we are looking at closing by year-end, and we welcome inquirers from serious investors.”
Get curated news on YOUR industry.
Enter your email to receive our newsletters.
Latest from Recycling Today
- Athens Services terminates contract with San Marino, California
- Partners develop specialty response vehicles for LIB fires
- Sonoco cites OCC shortage for price hike in Europe
- British Steel mill’s future up in the air
- Tomra applies GAINnext AI technology to upgrade wrought aluminum scrap
- Redwood Materials partners with Isuzu Commercial Truck
- The push for more supply
- ReMA PSI Chapter adds 7 members