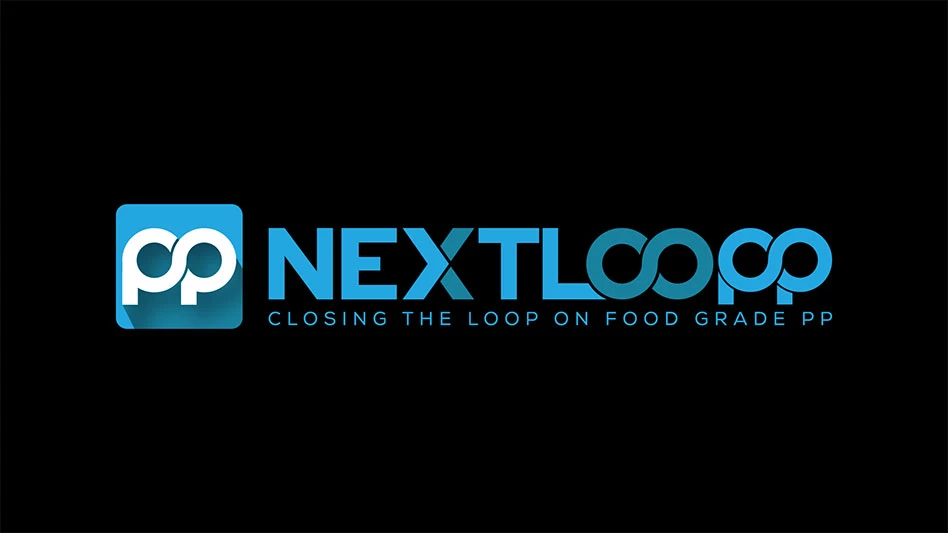
Image courtesy of NextLooPP
Bostik, Arkema’s adhesives solutions brand, recently became the 50th company to join Nextek Ltd.’s NextLooPP project to close the loop on food-grade polypropylene (PP). France-based Bostik and Nextek’s shared vision to develop self-adhesive labels that readily wash off packaging without leaving residual contamination (from either inks or adhesives) is at the heart of their joining forces.
Over the decades, the plastics sustainability experts at London-based Nextek have developed a range of science-based technologies to enhance the efficiency of mechanical recycling. This includes technologies that can remove odor and potential contaminants to deliver high-quality recycled plastics for nonfood and food-grade applications.
When Nextek launched NextLooPP in 2021 to address the specific challenge of food-grade recycled PP (rPP), the team reviewed the guidelines for packaging design for recycling.
In so doing, the team identified adhesives as one of the three key packaging components that limit recycling in addition to pigments and inks.
Reframing the way packaging is designed is key to evolving plastic packaging circularity. When it comes to packaging design, one of the big roadblocks to recycling has been labels because their adhesives and inks often can negatively affect the quality of the postconsumer resin (PCR).
Adhesives’ sticking point
Currently, many glues used for labels contain a range of resins and additives that can accumulate in the PCR as unintentionally added substances. Given these levels of contamination, the PCR might not be suitable for reuse in food-contact packaging.
Eric Parois, Bostik global market director – labels and narrow web technologies, and his team have developed a prototype wash-off label adhesive for high-density polyethylene (HDPE) that they believe will be helpful in the PP wash-off label adhesive development they are currently working on with NextLooPP.
In particular, this prototype is being tested in real-life industrial settings instead of in a lab to allow Bostik to better assess the circularity impact. Parois believes the HDPE prototype will enhance the team’s efforts for PP given that both polymers have similar characteristics, such as heat, chemical and moisture resistance as well as durability and surface energy levels. By considering how they are alike, they can speed up the development process as the adhesive formulation could be similar.
Nextek Managing Director Edward Kosior is interested particularly in the way Bostik can tailor its label requirements given current adhesive technology for pressure-sensitive labels often results in a progressive buildup of adhesive and ink residues in the recycled plastics that have an impact on the color and composition of recycled food-grade plastics.
Homing in on inks and coatings
Ensuring inks don’t bleed into the water during the recycling washing stages is another key facet to enhancing plastic recyclability. Bostik’s next-generation range of wash-off label solutions for PP, HDPE and polyethylene terephthalate can deliver on this, too.
Parois also is keen to explore labels and coatings further, particularly when it comes to improving packaging sorting performance, which he recognizes is critical to food packaging recycling. As such, NExtLooPP also is evaluating how fluorescent coatings using Bostik’s own systems can perform during the sorting phase.
Legislation to boost novel label technologies
Parois says despite some of these so-called novel label technologies being in existence for more than a decade, some brand owners have been reluctant to adopt them. He feels this is because of a reluctance to change. Now, legislation is stepping in to drive recycled content levels up by applying taxes on products that don’t contain targeted levels of recycled plastic and banning the export of end-of-life plastics across national boundaries to ensure recycling happens locally.
Parois anticipates this will accelerate the adoption of wash-off labels. In fact, he believes a number of factors are aligning to boost circular mechanical recycling, from legislation through to brands’ decisions to reduce their carbon footprint and their reliance on virgin materials.
Parois and Kosior acknowledge time is of the essence. Kosior says the technology exists to address the most awkward recycling challenges the world faces. We must apply realistic and scalable solutions to deliver outstanding results to achieve this.
Rethinking packaging design for circularity
As Kosior points out, we live in a world that still relies on plastic for a multitude of applications. We need to reframe our models for handling what we are producing and in particular revise how we design plastic products and packaging for the circular economy.
While recycling generally results in downcycling, circularity focuses on turning end-of-life products into recyclates that can be used to produce those same products. This crucial difference is a key reason why organizations such as Bostik are collaborating across the plastics supply chain to identify best practices that have the lowest carbon footprint and can turn valuable resources—such as food-grade rPP— back into food-contact packaging.
Latest from Recycling Today
- Aqua Metals secures $1.5M loan, reports operational strides
- AF&PA urges veto of NY bill
- Aluminum Association includes recycling among 2025 policy priorities
- AISI applauds waterways spending bill
- Lux Research questions hydrogen’s transportation role
- Sonoco selling thermoformed, flexible packaging business to Toppan for $1.8B
- ReMA offers Superfund informational reports
- Hyster-Yale commits to US production