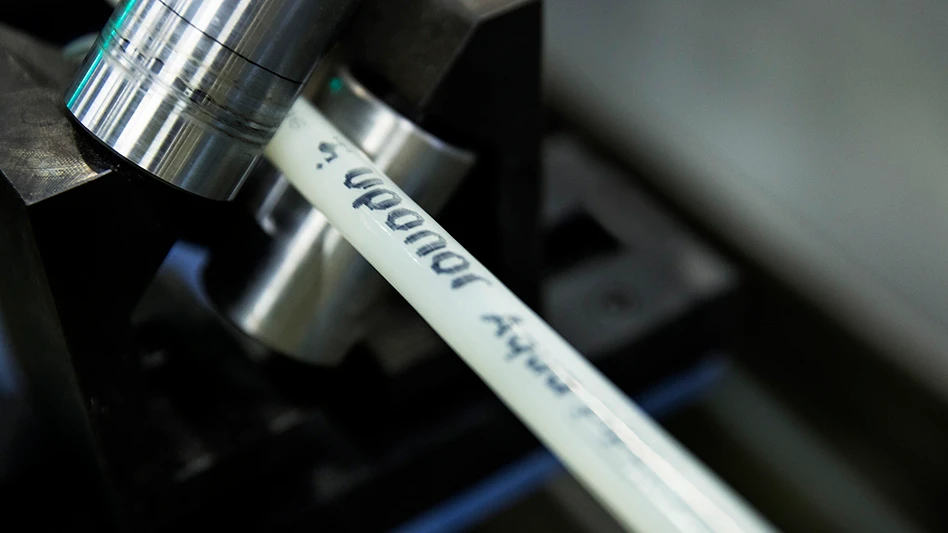
Photo courteous of Borealis AG
A consortium of Europe-based companies has cooperated to create a process that produces pipes made of cross-linked polyethylene (PEX) that uses feedstock derived from chemically recycled postindustrial plastic scrap. The four companies cooperating on the project are Finland-based Neste Oyj, Austria-based Borealis AG, Finland-based Uponor and Finland-based Wastewise.
The companies say they are “successfully using an International Sustainability and Carbon Certification (ISCC) PLUS certified mass-balancing approach” in what they call among the first implementations of the chemical recycling of PEX materials. “The whole value chain is traceable via ISCC PLUS certified mass-balancing,” Borealis says.
PEX pipes are used in heating and plumbing applications “due to their robustness, temperature resistance and longevity,” the companies say. However, the interconnected polymer chains can make them difficult to recycle with mechanical recycling technologies.
The project has been designed to show that chemical recycling “can close the circularity loop” for hard-to-recycle plastic scrap, “turning it into high-quality polymers feedstock and enabling the consecutive manufacturing of products with quality and properties identical to those in their previous life,” Borealis states in a press release.
The effort entails Wastewise using its pyrolysis-based chemical recycling technology to liquefy industrial scrap from Uponor’s PEX pipe production process, breaking the polymers down back into their building blocks and creating “an oil-like recycled intermediate.”
That liquid is then co-processed in Neste’s oil refinery in Porvoo, Finland, and “upgraded into high-quality drop-in feedstock for the production of new polymers,” Borealis says.
Borealis is feeding the resulting raw material into its steam cracker and “consequently polymerizing it into polyethylene as part of the company’s chemical recycling portfolio." Finally, Uponor uses the resulting polyethylene to create new PEX pipe products which are then used in the construction sector for heating, plumbing and cooling applications.
“We are very excited about this collaboration as it gives us a head start on our transition to circular materials,” says Thomas Fuhr, chief technology officer at Uponor. “At Uponor we have just celebrated the first 50 years of our PEX piping, and now our new long-term goal is to use 100 percent of our PEX [scrap] as raw material through closed-loop recycling.”
Borealis Global Commercial Director John Webster says, “Hard-to-recycle [scrap] plastic as input and high-quality polymers as output are not in contradiction anymore. In fact, we are able to integrate chemically recycled PEX pipe [scrap] plastic as a raw material into our established manufacturing processes. It doesn’t require additional tests, approvals or validation. It’s a drop-in solution ready to use even for drinking water applications.”
“The curtain is opening for chemical recycling,” says Mercedes Alonso, executive vice president at Neste. “It will still take time to reach large-scale operations, but this project is providing the blueprint for circular value chains for polymers via chemical recycling. It’s pushing the technology from the promise to the delivery phase. Further, it shows the importance of bringing the right partners together to cooperate.”
The companies say “little more than six months passed” between the start of the project and the production of the first pipes made with chemically recycled PEX scrap.
Latest from Recycling Today
- Domestic aluminum demand up through Q3 2024
- IntelliShift honored at IoT Breakthrough Awards
- Ace Green Recycling finalizes plans for battery recycling site in India
- Ambercycle, Benma partner to scale circular polyester
- NIST database aimed at increasing textile recycling
- ILA, USMX announce tentative agreement
- Innventure subsidiary acquires rights to advanced plastics recycling technology
- Radius experiences sixth consecutive quarterly loss