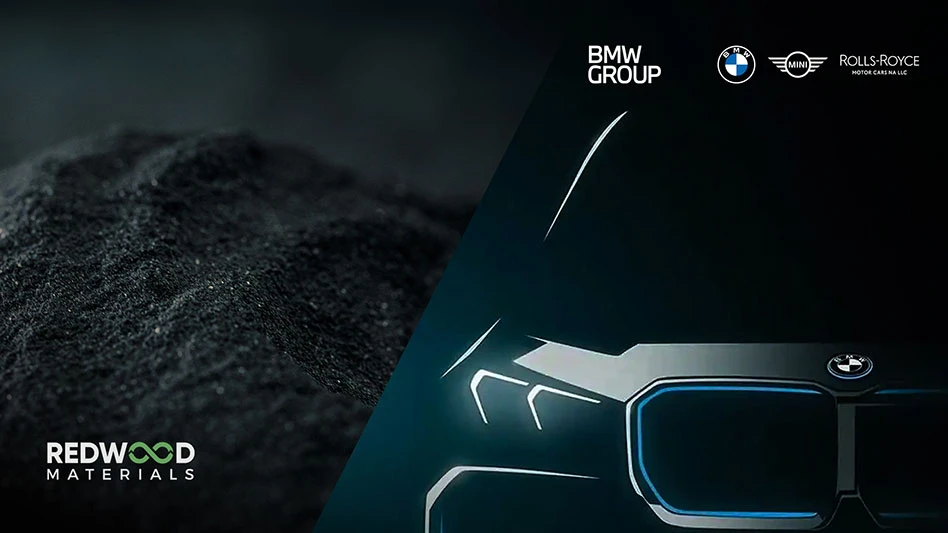
Photo courtesy of BMW of North America
BMW of North America, based in Woodcliff Lake, New Jersey, and Reno, Nevada-based Redwood Materials have partnered to recycle lithium-ion batteries from all-electric, plug-in hybrid-electric and mild hybrid BMW, Mini, Rolls-Royce and BMW Motorrad vehicles in the U.S.
Redwood Materials will work directly with BMW Group's network of approximately 700 locations across the U.S., including dealerships, distribution centers and other facilities, to recover end-of-life lithium-ion batteries and ensure critical minerals such as nickel, cobalt, lithium and copper are recycled and refined in the U.S. The partners say 95 percent to 98 percent of these critical minerals will be returned to the battery supply chain to build increasingly sustainable electric vehicles.
“Together with Redwood Materials, BMW is laying the groundwork for the creation of a fully circular battery supply chain in the U.S.,” says Denise Melville, head of Sustainability, BMW of North America. “We have said before that the future of BMW was electric, digital and circular, and this agreement brings us a step closer to meeting that goal.”
“The transition to electric mobility presents a tremendous opportunity to rethink how we manage the batteries that power our clean energy future,” says Cal Lankton, chief commercial officer at Redwood Materials. “Our partnership with BMW of North America ensures responsible end-of-life battery management that will improve the environmental footprint of lithium-ion batteries, help decrease cost and, in turn, increase access and adoption of electric vehicles.”
Redwood’s processes have a significantly smaller environmental impact than conventional mining, reducing energy by 80 percent, CO2 emissions by 70 percent and water by 80 percent, according to the company, which also has touted that its process results in 40 percent less emissions than other recyclers, according to a Stanford study.
Redwood Materials operates a campus in Reno where battery components are recycled, refined and manufactured, with a second Redwood Materials campus under construction in Charleston, South Carolina, not far from BMW Group Plant Spartanburg and Plant Woodruff. At these plants, BMW will assemble at least six fully electric models and the high-voltage battery packs for those vehicles before the end of the decade. The company’s battery cell manufacturing partner, AESC also is nearby in Florence, South Carolina.
Plant Spartanburg is the largest single BMW plant in the world. Since it was established 30 years ago, the plant has expanded several times to its current size of 8 million square feet and can produce up to 450,000 vehicles annually.
Sponsored Content
Labor that Works
With 25 years of experience, Leadpoint delivers cost-effective workforce solutions tailored to your needs. We handle the recruiting, hiring, training, and onboarding to deliver stable, productive, and safety-focused teams. Our commitment to safety and quality ensures peace of mind with a reliable workforce that helps you achieve your goals.
Redwood is building a 600-acre campus at Camp Hall in Berkeley County, South Carolina, that he company says will create more than 1,500 jobs. It is a $3.5 billion investment in the local community, according to the company. At its initial planned capacity, the South Carolina operation will be able to produce 100 gigawatt hours (GWh) of cathode and anode metals per year, or enough to power more than 1 million EVs.
Get curated news on YOUR industry.
Enter your email to receive our newsletters.
Latest from Recycling Today
- EPA plans to revisit numerous environmental, climate regulations
- Scientists use air, inexpensive catalyst to break down plastic
- Miami-Dade Innovation Authority launches fifth Public Innovation Challenge
- EVSX installation supported by Call2Recycle Canada
- Wendt commissions shredding plant, nonferrous system at Island Recycling
- Fornnax wins Green Innovation of the Year award
- Recyclers opening doors to the public through APR program
- CMI comments on Trump’s Section 232 tariffs