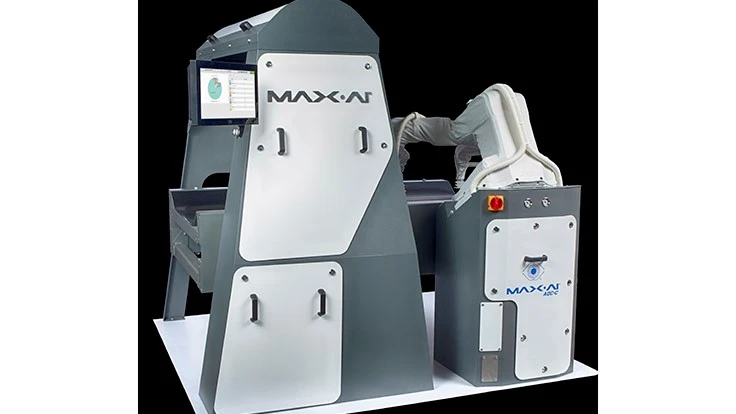
Bulk Handling Systems (BHS), Eugene, Oregon, has launched the Max-AI AQC-C, which is a recycling sorting solution comprised of the Max-AI VIS (Visual Identification System) and at least one collaborative robot (CoBot). CoBots are designed to work safely alongside people on the line, which allows the AQC-C to be quickly and easily placed into existing material recovery facilities (MRFs), the company says.
BHS launched the original Max-AI AQC (Autonomous Quality Control) at WasteExpo in 2017. At this year’s show in Las Vegas, the company’s next-generation AQC will be on display along with the AQC-C.
Unlike the AQC, which needs more structure to support the robot and guard employees, the AQC-C can be installed in sort cabins, on narrow walkways and in other tight locations. It is also scalable—up to four robotic sorters can be added behind each Max-VIS system, BHS says. Each sorter can sort up to 40 picks per minute and handle up to three different material types.
“The AQC-1 and AQC-2 are fantastic solutions in the right system, but in our business, footprint and installation modifications are always a major factor,” BHS Vice President of Sales and Marketing Rich Reardon says. “The AQC-C is the perfect complement to our Max-AI family of sorters; it’s a fast and easy installation and can work essentially any place a manual sorter can. Unlike a manual sorter, the AQC-C won’t get tired, sick, injured or no-show—and it will sort all day without a break. The flexibility is tremendous. Customers are able to add one, two, three or four units per VIS and adapt with their processing needs. We’re really excited about our newest Max offering and can’t wait to show it off at WasteExpo.”
Max-AI VIS is a standalone piece of equipment used to analyze and report material composition data to operators. The Max-AI product line includes VIS in its standard design with all equipment, rather than incorporated into the equipment structure. This makes possible the installation of VIS independent from a robotic or optical sorter, which the company says benefits Max-AI customers in several ways. The neural network artificial intelligence (AI) is trained for each installation, which takes place after VIS gathers data from the material stream. When VIS is installed beforehand, the robotic or optical sorters can be installed when the AI is trained and optimized. It also allows for detailed material composition data to verify that either the purchased equipment is the correct solution or that a modification should be made. Finally, a standard VIS design provides the future flexibility to add equipment to VIS units or move equipment as processing needs change.
Watch the video of the Max-AI AQC-C in operation below.
Latest from Recycling Today
- ReMA opposes European efforts seeking export restrictions for recyclables
- Fresh Perspective: Raj Bagaria
- Saica announces plans for second US site
- Update: Novelis produces first aluminum coil made fully from recycled end-of-life automotive scrap
- Aimplas doubles online course offerings
- Radius to be acquired by Toyota subsidiary
- Algoma EAF to start in April
- Erema sees strong demand for high-volume PET systems