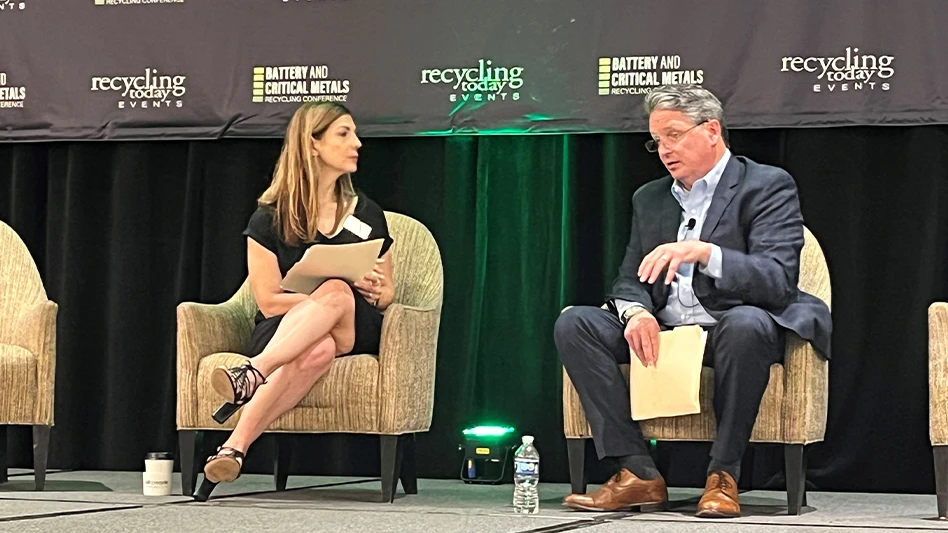
Photo by Chris Voloschuk
In four decades of what he dubbed his “journey through sustainability,” John Kelly said the recycling industry and its markets have changed numerous times.
But shifts he’s seen in the battery recycling sector since becoming the vice president of operations at Charlotte, North Carolina-based Cirba Solutions in 2022 have been much quicker than what he witnessed during his 18 years at WM, where he occupied a wide variety of roles before spending another 10 years at Badger Daylighting Corp. as its vice president of U.S. operations and, later, its chief operating officer.
RELATED: BCMRC23: Recovering value from EV batteries
In the keynote session at the inaugural Battery & Critical Metals Recycling Conference hosted by Recycling Today this June in Atlanta, he elaborated on the growing sector and the need for collaboration as more end-of-life batteries enter the scrap stream.
“When I look back at traditional recycling and how the industry changed and markets changed, this is happening at break-neck speed,” he said. “In the 16 months I’ve been [at Cirba], I’ve seen the industry change three or four times already.”
Kelly pointed to advancements in lithium-ion battery (LIB) recycling technology, including Cirba’s hydrometallurgical process that recovers battery-grade salts for cathode manufacturing. Noting that LIB consumption is set to outpace raw materials supply by the end of 2025, he said the next big change in the industry will be creating a more robust domestic supply chain of the critical minerals needed to power them, such as lithium, cobalt and nickel.
Of the looming supply-demand curve, Kelly said, “It’s imperative that we shift our focus to domestic materials, reducing our overseas competition and increasing our regional battery supply chain.”
He added, “At Cirba Solutions, we’ve developed a network of not only what I call remanufacturing facilities but also storage facilities throughout the United States and North America.”
Cirba was formed in 2022 when established battery recycling companies Retriev Technologies, Battery Solutions and Heritage Battery Recycling merged. The company has seven operational battery recycling facilities across North America, including a $200 million expansion of its processing site in Lancaster, Ohio, and an eighth “flagship” location in Richland County, South Carolina, expected to come online by the end of 2024.
The company has received roughly $82 million in funding from the U.S. Department of Energy to support its operations and expansion, as well as investments of $245 million and $50 million from EQT Infrastructure and Marubeni Corp., respectively.
Partners in recycling
Throughout the session, Kelly spoke of the need for collaboration along all links of the battery supply chain when it comes to recycling.
“As technology advances, we’ll get better, but we’ve got to work together to solve these issues and bring these materials domestically back into the market and supply chain,” he said. “The OEMs [original equipment manufacturers] are out in front, and they’re moving forward, and this is the future when it comes to lithium-ion battery supply.”
Kelly noted that Cirba has partnered with a number of OEMs, such as Honda and General Motors, to collect and recycle end-of-life batteries. In May of this year, the company announced a partnership with Westminster, Colorado-based software and services provider KPA designed to help personnel at numerous automobile dealership brands manage the safe servicing, handling and shipping of electric vehicle (EV) batteries.
RELATED: Circular Solutions | Investing in the future
“We’ve partnered with several OEMs and collaborated with them, working with their engineering groups,” he said. “Coming from the perspective of an operations person, I’m trying to mine these batteries out of the packs and really look at the technology that is going into building the packs safely so they can go into the cars safely, but also meet the expectations of recycling.
“We’ve gotten into several relationships with OEMs to work with them to work on the packs—not so much the design of the packs but how we can engineer or get the materials out of the packs,” he added. “Also, when we look at the collaboration and the technology, I’ve been working with some firms that have been working in the traditional recycling world and bringing them into the new world, as I call it, of recycling. Really, the technology that is out there that is being developed at breakneck speed is unbelievable. We’ve been working with the OEMs but also with the engineering groups and the manufacturing groups to come up with the best way to process this material.”
Safety first
Transporting and processing end-of-life batteries in the safest way possible is a massive challenge, Kelly said.
“What I’ve seen the last 16 months is the magnitude of the batteries that continue to come into the waste stream,” he said. “It’s looking at how we can, one, segregate those out of the waste stream and do it safely. One of the big concerns that I had is just on the safety side. We do a lot of work at Cirba each day to make sure our employees are safe and that we’re doing it correctly, being environmental stewards. That’s one thing.
“Also, as I look at it, technology in batteries is changing so fast,” he added. “Particularly when I look at lithium-ion and different materials that we look at, how they’re coming into us, whether that be in packs or modules or even cell form, and how do we need to recycle those. In the industry, no one OEM, no one competitor or whoever has this figured out yet, even though there’s some that might think they might. This thing is moving so fast, and I think what we need to do is look at the industry and work together to solve some of those problems.”
Kelly said the industry needs to advance its communication and collaboration not just with OEMs on the front end but also on the back end with offtake agreements and where material is shipped. He conceded that this can be tough to accomplish based on the speed with which the industry is moving.
“People want different things, they want different materials coming out a certain way, and this can’t be where we do it 32 different ways,” he said. “We’ve got to find a way to make sure that, one, we can extract precious metals and get the material out of the battery and do it safely, but we can’t change on a dime every 10 days. We’re not vertical by any stretch of the imagination. It’s really important that we get to a certain point where we’re producing material that offtakes can take and put back into the batteries, but even though we’re changing the technology, we’ve got to settle on certain end markets and where those offtakes are going to go.”
A major opportunity, he said, exists in getting the battery material to a certain state on the front end where it can be processed in as large of a quantity and as safely as possible, and collaborating with OEMs to build out vehicles and battery packs in an environmentally friendly way that also allows them to be easily taken apart and processed could be a solution.
“That is the closed loop we need to figure out,” Kelly said. “I would also say that when I look at the industry through my perspective, it’s that no one thing has this figured out. The safety part of it, the transportation part of it, that’s going to be critical to our success in this industry, … how we get materials from point A to point B safely, process them and then get those materials, reduce our carbon footprint and get materials back into the battery. That’s a huge challenge.”
Cirba uses a combination of its own vehicle fleet and third-party assistance to transport material. Safety is at the forefront of how the company manages moving material, Kelly said.
“When I look internally, our drivers are hazmat trained,” he said. “It’s very important. It’s not traditional. What they’re putting on the backs of their trucks they’re trained to carry. That is something that’s paramount. We’re going to continue to invest in that. … It’s expensive to do that, but we feel that the safety outweighs the expense.”
He added that when Cirba partners with a third party, it will train that company’s drivers to transport material safely, as well. “What we’re moving today, that’s going to grow exponentially, and we’ve got to figure out better packaging; we’ve got to figure out safer ways to move it.”
Evolving landscape
When it comes to LIBs, Kelly said Cirba gets about one-third of its material from EVs, with the rest coming from consumers, recycling programs, environmental and waste companies and other agreements Cirba has in place. He noted, though, that the EV battery portion is increasing quickly, largely given their density and weight.
“We’re constantly working with the OEMs on proposals and bringing materials into our facilities,” he said. “I can see that, over time, as we build out these facilities, the need for more material to be able to process. The EV side of the business will increase. When I look at the consumer side of the business and the environmental services side of the business, we’re working with both of them, but the consumer side is going to continue to increase significantly. Again, it’s the adoption rate, getting people to understand these materials, that these batteries are recyclable, is going to be critical.”
Beyond industry partnerships and refined recycling processes, Kelly said consumer education will continue to play an important role in securing a more robust domestic material stream.
“Everybody’s walking around with a cellphone that has a lithium battery in it,” he said. “It’s really about educating the customers on getting those into the correct stream so they can be recycled. That’s critical. The focus is on getting those materials at every level from the consumer to the battery recycling stream so that we can recycle them.”
He suggested battery recycling education could begin at the earliest stages of childhood. “All these kids are running around with cellphones in their hands at 8, 9 years old. They have tablets. I can’t tell you how many unicorns I’ve recycled that have lithium-ion batteries in them.
“It’s everywhere,” he added, “and we’ve got to be stewards of this, champions of getting that material back into the stream so we can meet or exceed the supply and demand that’s coming.”
Latest from Recycling Today
- New recycling grant program launches in Massachusetts
- Tire Recycling Foundation names executive director
- Dock 7 named 2025 Exporter of the Year at New Jersey International Trade Awards
- Waste Connections reports ‘better than expected’ Q1 results
- Commentary: How EPR is transforming the packaging industry
- Acerinox names new North American Stainless CEO
- Greenwave closes 2024 books with red ink
- Steel Dynamics nets $217M on record shipments