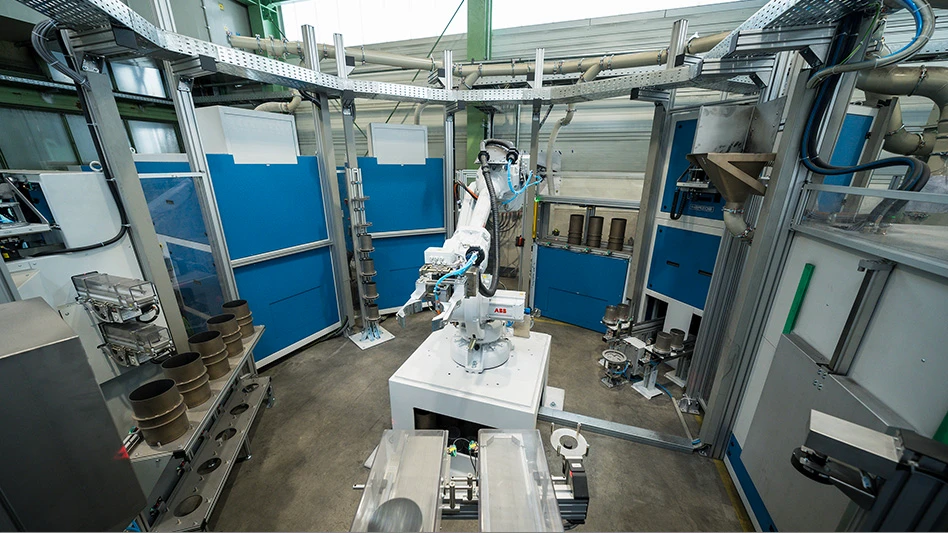
Photo courtesy of Aurubis AG
Germany-based recycled-content metals producer Aurubis AG says it has successfully commissioned an automated system to assay inbound scrap shipments at its Lünen, Germany, copper production plant.
“Sample preparation of feed materials, such as e-scrap, is now fully automated with the help of cutting-edge robotics,” Aurubis says, adding that its system “efficiently delivers reliable samples to the laboratory in just an hour for a sample preparation process that used to be carried out manually in up to 12 stages and could take five days.”
Aurubis has invested up to $6 million (“a mid-single-digit-million-euro amount”) in the new system, which was developed about three years ago as part of a companywide automation and digitalization strategy.
“The new system is absolutely state-of-the-art and, with up to 10,000 samples per year, the most powerful of its kind in our industry,” says Lünen Plant Manager Verena von Weiss. “It’s a flagship project: for both the Lünen site and the entire Aurubis Group.
“With a dedicated team, we moved ahead with the planning, construction and commissioning in less than a year. We gathered crucial experience to make the process even more secure, which all Aurubis sites will now profit from.”
The metals producer says the installation at the Lünen site is “just the beginning,” adding that automated sampling at additional sites and of a wider variety of input materials will follow soon.
The new system also provides anti-theft internal controls upgrades. Earlier this year, a German court sentenced a group of people, including at least one Aurubis employee, to prison sentences for their roles in perpetuating a system that entailed large-volume purchases of metallic inputs with misrepresented metals content.
The company lists “process security” as one of three areas in which the new system provides a boost, along with occupational safety and environmental protection.
“The self-contained process leaves practically no room for manipulation,” Aurubis says. “Every assessment is fully documented, including a photo record, and can be verified via analysis software on an ongoing basis. The automation therefore significantly enhances the quality and reliability of the entire process.”
“We process about 1.1 million tons of recycling material in the group each year [and] our suppliers’ trust is our most important currency in the global competition for recycling material,” Chief Operations Officer of Multimetal Recycling Inge Hofkens says. “With the fully automated system that is now in operation, we are making a targeted investment in strengthening transparency and trust in Aurubis.”
Aurubis calls its new system “a model for other sites and materials” and indicates it already is investing in a similar system for its Hamburg facility. Aurubis plants in Pirdop, Bulgaria, Beerse, Belgium, and Augusta, Georgia, in the United States are scheduled to follow.
In addition to electronic scrap, other materials purchased for the company’s smelter network are being targeted for automated sampling. “The system already enables the continuous mechanical sample preparation of materials like printed circuit boards, shredded materials containing iron and dried slimes,” Aurubis says.
The company says the automated system also will eliminate manual work stages and reduce noise emissions. As a completely enclosed system, Aurubis says the new techniques reduces environmental impacts tied to particulate matter.
Latest from Recycling Today
- Study highlights progress, challenges in meeting PCR goals for packaging
- Washington legislature passes EPR bill
- PureCycle makes progress on use of PureFive resin in film trials
- New copper alloy achieves unprecedented high-temperature performance
- Gränges boosts profits and sales volume in Q1 2025
- RMDAS April figures show recycled steel price setback
- Steer World offers PEX plastic recycling machine
- New recycling grant program launches in Massachusetts