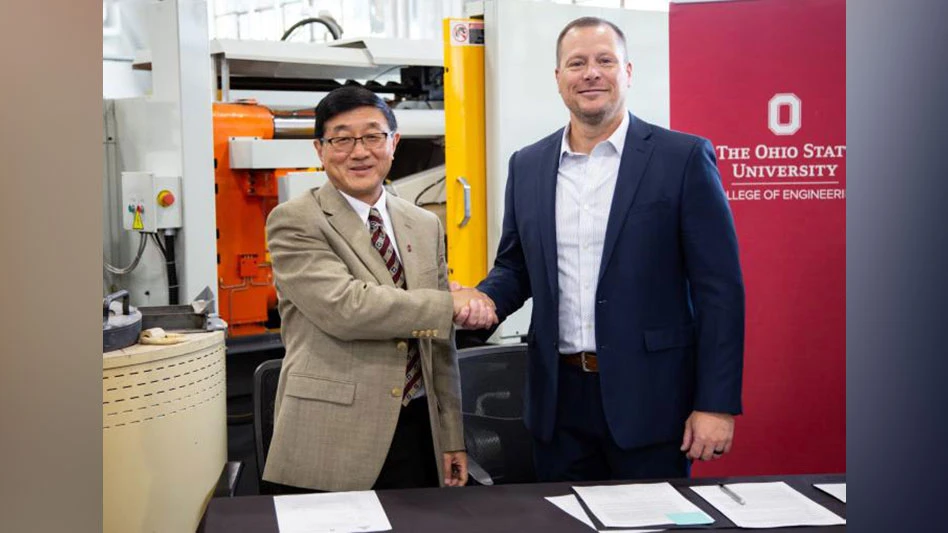
Photo courtesy of The Ohio State University
The Ohio State University and Audubon Metals have entered into a licensing agreement intended to advance the commercialization of technology that has the potential to increase the use of recycled aluminum alloys.
Audubon Metals, with locations in Henderson, Kentucky, and Corsicana, Texas, is owned by an affiliate of Koch Enterprises Inc., headquartered in Evansville, Indiana. The company operates heavy media plants and produces secondary aluminum alloys. It processes zorba, which is primarily aluminum scrap that is produced by shredding end-of-life automobiles, to produce secondary aluminum alloys that are delivered to domestic and international die casters.
Led by Alan Luo, professor of materials science and engineering and integrated systems engineering, a research team that includes graduate students and postdoctoral researchers has developed a way to produce secondary aluminum alloys for use in structural die-casting applications.
According to a news release from The Ohio State University, the automotive industry uses primary aluminum produced from mining and smelting for structural applications because secondary aluminum alloys can include contaminants such as iron that can result in inferior mechanical properties. But secondary aluminum alloys are up to 50 percent less expensive to produce and use a fraction of the energy compared with mined aluminum.
Ohio State says its technology neutralizes iron contamination common in typical aluminum scrap, enabling the alloys produced for the material to exhibit mechanical properties such as those of primary alloys used in die casting, a high-pressure manufacturing process that forces molten metal into a mold to produce large thin-wall components.
“This technology that we developed will have a positive impact on the manufacturing industry and our environment, so we call it a green alloy,” Luo says. “It is exciting to see the technology we developed in the lab go to the marketplace.”
“In partnership with Ohio State, we will create new recycled aluminum alloys for lightweight part applications while we also promote sustainability,” Audubon Metals President and CEO Brian Hawkes says. “We have a lot of new opportunities to use this new die-cast equipment, and we are excited to be working with such impressive associates at Ohio State.”
The U.S. Department of Energy’s Reducing EMbodied-Energy And Decreasing Emissions (REMADE) Institute funding much of the research that resulted in the technology. Ohio State is an academic member of the REMADE Institute, and Luo serves on its Technical Leadership Committee as deputy node leader of manufacturing materials optimization, while Audubon Metals is an industry member of REMADE.
REMADE CEO Nabil Nasr says, “This is a great accomplishment. We believe the technology that’s been developed, which is capable of reducing energy consumption by 13.1 [petajoule] per year, will accelerate the nation’s transition to a circular economy and, more specifically, will be incredibly valuable to the U.S. automotive industry as it transitions to electric vehicles over the next few years.”
The university says its Technology Commercialization Office works with thousands of researchers across the university to protect and transfer innovations into the market to advance research, improve lives and benefit society.
“Ohio State’s world-class researchers are always at work solving meaningful problems that are impacting society. The Technology Commercialization Office is fortunate to collaborate with researchers like Dr. Luo and companies like Audubon Metals to help these important innovations turn into products and services that positively impact the citizens of Ohio and the world,” says Kevin Taylor, senior associate vice president of technology commercialization at The Ohio State University.
Recycling Today has reached out for additional information on the technology and the commercialization plans.
This innovation is the most recent in attempts to get more value out of aluminum scrap.
Sortera Alloys, Markle, Indiana, is a scrap metal sorting and recycling company that was spun out from the Advanced Research Projects Agency – Energy (ARPA-E) project in the U.S. Department of Energy, which seeks to advance high-potential, high-impact energy technologies that are too early for private-sector investment. The company has developed and patented sorting technology that uses artificial intelligence- (AI-) based sensor sorters to upgrade shredded aluminum scrap. Last year, Sortera announced that it had formed a long-term commercial agreement with aluminum producer Novelis to separate mixed automotive scrap from manufacturers into individual alloys and recycle them back into the same product, allowing the aluminum producer to meet automotive manufacturers' needs for performance, durability, safety and design. The partners also have plans to process shredded scrap from end-of-life automobiles.
Earlier this year, the Department of Energy (DOE) Pacific Northwest National Laboratory in Richland, Washington, said it worked with Canada-based automotive components maker Magna International on a new manufacturing process through which aluminum scrap can be collected and “transformed directly into new vehicle parts using an innovative process being developed by the automotive industry, in particular for electric vehicles.”
The patented Shear Assisted Processing and Extrusion (ShAPE) process collects factory-generated scrap trimmings from automotive and supplier plants and transforms it directly into suitable material for new vehicle parts, the DOE says. The technology now is being scaled to make lightweight aluminum parts for electric vehicles.
Latest from Recycling Today
- Enfinite forms Hazardous & Specialty Waste Management Council
- Combined DRS, EPR legislation introduced in Rhode Island
- Eureka Recycling starts up newly upgraded MRF
- Reconomy Close the Gap campaign highlights need for circularity
- Nickel carbonate added to Aqua Metals’ portfolio
- EuRIC, FEAD say End-Of-Life Vehicle Regulation presents opportunity for recyclers
- Recyclers likely to feel effects of US-China trade war
- BCMRC 2025 session preview: Navigating battery recycling legislation and regulations