
Photo courtesy of Picture This! Photography
Making batteries more sustainable is the mission of Ascend Elements, according to CEO Mike O’Kronley.
The battery recycling company, founded in 2015 and headquartered in Westborough, Massachusetts, has been busy for the last several years building out its capacity to close the battery supply chain loop while perfecting its patented Hydro-to-Cathode precursor synthesis process to manufacture NMC (nickel, manganese, cobalt) precursor cathode active material (pCAM) and cathode active material (CAM) recovered from spent lithium-ion batteries (LIBs) and battery manufacturing scrap.
RELATED: Ascend Elements, Call2Recycle to offer customized EV battery services
In March 2023, Ascend officially opened its first commercial-scale LIB recycling facility, a $50 million project dubbed Base 1, in Covington, Georgia. The facility, which converts end-of-life batteries into black mass, began partial operations in August 2022 and has an annual capacity to process 30,000 metric tons of end-of-life LIBs and manufacturing scrap per year. In late-2022, the company began construction of its $1 billion Apex 1 campus in Hopkinsville, Kentucky, where, upon completion, it will produce pCAM and other engineered battery materials for an estimated 750,000 electric vehicles (EVs) per year.
Since September 2023, the company has raised more than $700 million from numerous investors to aid in the development of its facilities, and in October 2022 was awarded $480 million in grants from the U.S. Department of Energy through the Bipartisan Infrastructure Law Battery Materials Processing and Battery Manufacturing Initiative.
And O’Kronley, who was named the company’s CEO in March 2020, says making sure those batteries are reused and recycled in a clean and efficient manner is what is fueling Ascend’s growth.
Speaking during the opening keynote session of the 2024 Battery and Critical Metals Recycling Conference, hosted by Recycling Today in mid-June in Atlanta, he noted that batteries are fueling the energy transition in the United States, though the way they currently are made is relatively dirty from a CO2 perspective.
“It’s very energy intensive to mine all these minerals form the ground and concentrate and refine them and transport them all across the world to the battery manufacturers,” he said. “There’s a lot of energy that’s needed and required for that, and so the embedded carbon that is there in all of these battery materials is very high.
“When you are able to recycle batteries, you’re essentially able to produce new battery materials at a very low CO2 footprint,” he continued. “You’re able to reuse some of these critical metals that are in them—nickel, cobalt and lithium—and reuse them over and over again. You’re essentially making batteries much more sustainable, lowering that CO2 footprint dramatically. … They will need to be reused and recycled, so having a very efficient way of doing that, a very clean way of doing that, that’s really helping battery manufacturers and, really, the entire industry become more sustainable and it’s something that the market will overall need. And that’s what we’re on a mission to do, is to help battery manufacturing become more sustainable.”
Keeping resources at home
O’Kronley noted that the battery industry in general is highly concentrated in Asia and, more specifically, China, where it is considered an “encouraged industry” more than a decade ago.
“It’s all things battery,” O’Kronley said, “whether it’s battery assembly, whether it’s battery materials, whether it’s battery recycling, it’s already there in place on that scale in China.”
And that same industry encouragement is starting to take hold around the world, including in the U.S.
“Yes, [the battery industry] is encouraged in the U.S.,” he said. “We see a market here in the U.S., and the U.S. government sees us as being an encouraged industry.”
RELATED: Ascend Elements, Koura to explore graphite recycling in US
The U.S. doesn’t necessarily want to buy batteries and battery materials from China, O’Kronley added, especially when those materials are fueling the U.S.’ energy transition. He pointed to the Bipartisan Infrastructure Law and the Inflation Reduction Act as two key drivers in the building of battery infrastructure in the country, along with investments from other sources for battery manufacturing, recycling and more.
“We’ve received about half a billion dollars from the Department of Energy to build some of that key critical infrastructure that can take a recycled battery and convert it back into critical battery metals and battery materials that will go right back into the supply chain in the United States,” O’Kronley said. “This is all part of that key infrastructure and it’s really part of that infrastructure that ultimately needs to move away from Asia and China and be more local. And that’s part of a national security initiative.”
Though the U.S. is playing catch-up with China when it comes to battery manufacturing and recycling capacity and capability, O’Kronley said one thing the U.S. is “fantastic” at is innovation.
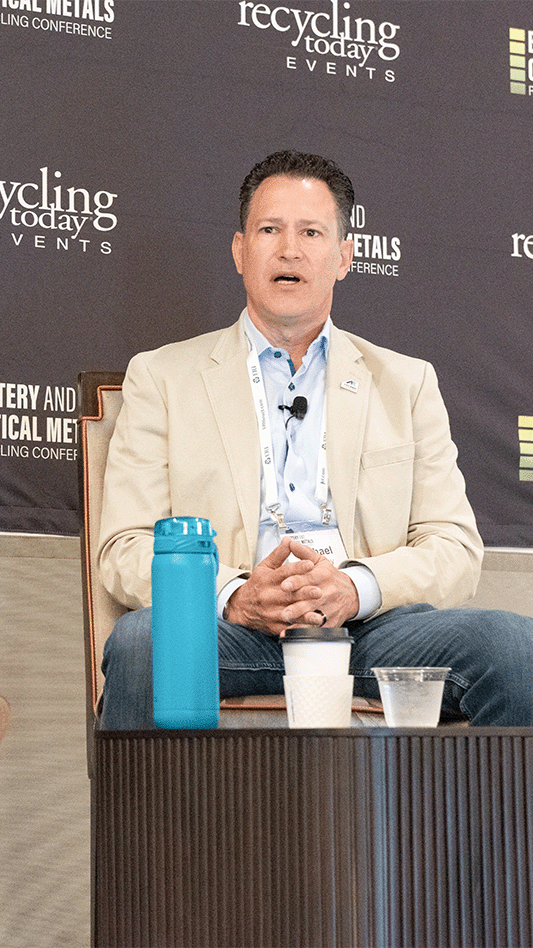
He pointed to Ascend’s patented Hydro-to-Cathode technology, which was developed and piloted about 12 years ago out of a university located outside of Boston, as one example of domestic innovation.
“It was a new and innovative way to recycle batteries very efficiently, more efficient than anything they do in China,” he said.
Ascend’s specialty is transforming end-of-life batteries back into cathode materials, but the company needed some help in its early stages because it was competing with more established players that already had some capacity and capability globally.
“If we want that to be in the United States, you need a certain amount of help, and that’s certainly what the DOE has done, not only with us, but a lot of other technologies and a lot of other U.S. innovators,” O’Kronley said. “We need to put that in the United States, and that’s really helped us. It’s helped us with getting further investment, and so we’re now building the first active precursor plant in all of North America in Hopkinsville, Kentucky, that will be operational [in 2025].”
The Apex 1 facility in Kentucky is being paid for in part by DOE funding, and O’Kronley described it as “the pinnacle of bringing batteries in and transforming them into something much more valuable.”
Cathode material, he noted, is the most expensive material that goes into a battery, and there is a huge value difference if that material can be made from recycled batteries.
“We’re about capturing that value,” he said.
The facility plan
Ascend began operations at its Base 1 facility in Georgia near the end of 2022, bringing in battery cells, manufacturing scrap, end-of-life battery packs and more for processing. “That’s why we call it a ‘base,’” O’Kronley said. “There’s really some of that preprocessing [taking place], which, in our terminology, it’s transforming a battery into black mass.”
Batteries brought into the Base 1 facility are discharged and shredded and turned into black mass. Additional products recovered in the process such as aluminum, copper and plastics, are segregated and sold to other recycling companies.
“We’re really after that black mass, because that’s where all the valuable critical metals are in a battery,” O’Kronley said. “The lithium, nickel, cobalt, manganese, that’s what we’re after and that’s what we ultimately use to make our cathode materials.”
RELATED: Ascend Elements to relocate its headquarters, R&D Tech Center
The Georgia facility features two shredding lines, and O’Kronley said within the next several months the site will be capable of extracting lithium out of black mass and turning it into lithium carbonate, which Ascend plans to sell primarily to cathode manufacturers. The nickel, manganese and cobalt found in the black mass will be sent to Ascend’s Apex 1 facility in Kentucky for processing into CAM and pCAM. O’Kronley noted that the Apex plant, which will boast 32 Hydro-to-Cathode processing lines, will be able to process black mass regardless of lithium’s presence.
O’Kronley said the company already has a North American customer for the pCAM that will be produced at the facility once it begins operating in the first half of 2025. In the meantime, the company is fine-tuning Apex procedures and training employees for what’s to come.
“It’s really the first facility [of its type] in the world,” O’Kronley said of the 65-acre Apex campus. “There are lots of precursor facilities; there’s extraction facilities; there are shredding facilities. But nobody in the world is doing this hydro-to-cathode process, this unique process of converting black mass to pCAM. There’s been a lot of development work that’s been done, but once you do it at scale, things will be a little different.
"We have to make sure we’re ramping up efficiently, because we have customers who have a lot of demand for the material, and we can’t miss our milestones or deliveries. That’s why we’re putting all our effort into getting ramped up.”
Looking ahead
When considering what Ascend’s U.S. footprint might look like a decade from now, O’Kronley envisioned there being a “massive amount” of batteries on the market that will eventually need to go somewhere for recycling.
“They will not accidentally be thrown away,” he said. “EV batteries are one thousand-plus pounds, and so you’re not going to just place that into a dumpster somewhere.”
RELATED: Ascend Elements to cut carbon emissions for EV battery material by 2030
He also pointed out the high value of metal found in batteries, measured in thousands of dollars.
“Because there’s that economic value that’s sitting there, they will not accidentally go into a landfill,” he said. “There will be channels that will be developed, and, over time, those channels will be more efficient.”
With so much battery material available and a need for critical battery metals in the U.S., O’Kronley predicted the increased use of recycled content in batteries going forward.
“If you look at more metals in more mature industries—steel, aluminum, copper—they’re highly recyclable across the industry. We’re going to see the same with batteries and battery materials,” he said. “You’re going to see, in 15 or 20 years, half of all battery material is going to come from recycled sources.”
He said that to meet that future demand, Ascend has its Base 1 plant in Georgia that will process about 30,000 tons of black mass annually, “which is the tip of the iceberg of what’s going to be needed.”
He added that the need will arise for similar facilities to be built across the country—whether owned by Ascend or a different company—to receive and preprocess batteries and prepare them for chemical processing or refining facilities similar to Apex 1.
“We’ve invested a lot into the infrastructure in that facility, so we’re going to concentrate for a while on the Kentucky area and in that campus,” he said. “But it may also become advantageous for us to move and have a second Apex or a third Apex plant in the United States. That is where the program will be. We’ll have many more Base facilities, but fewer Apex-type facilities in the U.S.”
Additionally, O’Kronley said the company already is expanding to Europe, having established a joint venture agreement with Polish firm Elemental Strategic Metals for a Base-type facility that will be located in Zawiercie, Poland. In the future, he said he expects Apex facilities to be built throughout Europe, as well.
He added that partnerships will help drive the industry forward.
“We are open to partnerships,” O’Kronley said. “I think in this industry, to achieve the things that we want to achieve, we’re going to be seeing a lot more partnerships. It won’t just be one company standing alone. It takes a lot of capital and it’s hard to do that all on your own.”
Latest from Recycling Today
- New recycling grant program launches in Massachusetts
- Tire Recycling Foundation names executive director
- Dock 7 named 2025 Exporter of the Year at New Jersey International Trade Awards
- Waste Connections reports ‘better than expected’ Q1 results
- Commentary: How EPR is transforming the packaging industry
- Acerinox names new North American Stainless CEO
- Greenwave closes 2024 books with red ink
- Steel Dynamics nets $217M on record shipments