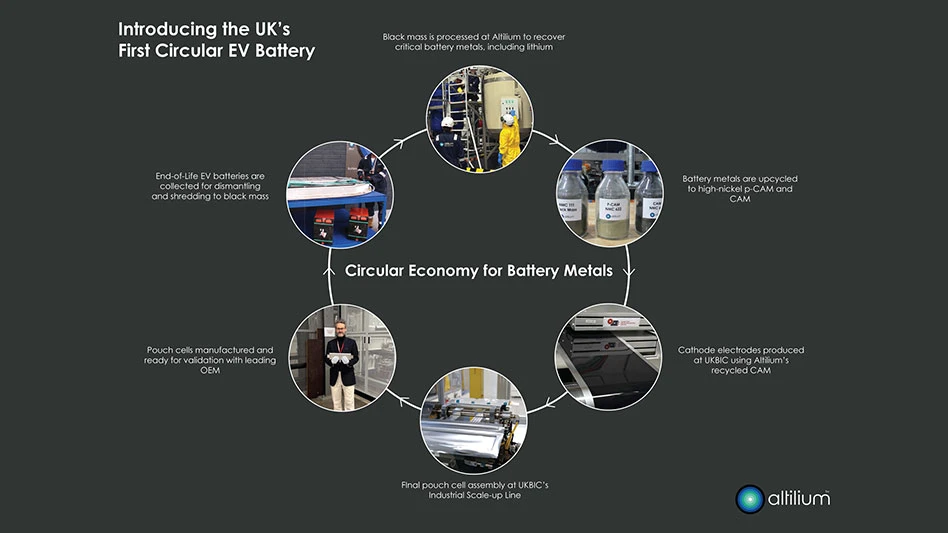
Image courtesy of Altilium
United Kingdom-based lithium-ion battery recycler Altilium has announced the production of electric vehicle (EV) battery cells using recycled cathode active materials (CAM) at the UK Battery Industrialisation Centre (UKBIC), the U.K.’s national battery manufacturing scale-up facility.
According to Altilium, this production milestone marks the first time recycled materials have been used to produce new battery cells in an industrial environment in the U.K.
The pouch cells were manufactured at UKBIC’s facility in Coventry, England, using Altilium’s recycled EcoCathode NMC 811-2036 CAM, produced at its recycling facilities in Devon, England. By recovering these critical metals from end-of-life EV batteries and gigafactory waste, Altilium says it is not only reducing the U.K.’s reliance on imported raw materials but also cutting the carbon footprint of battery manufacturing.
RELATED: Altilium recycling LFP EV batteries for global OEM
Altilium says the battery cells will now undergo comprehensive validation studies with an automotive original equipment manufacturer (OEM), supporting its regulatory and sustainability targets. Under the European Union’s Battery Regulations, new EV batteries sold into the EU will need to contain minimum levels of recycled lithium, nickel and cobalt by 2031 with further increases in 2036.
“This milestone marks the first time full battery circularity has been achieved in the U.K., from recovering critical minerals, including lithium, from end-of-life EV batteries and upcycling them into a high-performance cathode, to manufacturing a new battery for validation with a leading U.K. automotive OEM,” Altilium Co-founder and Chief Operating Officer Christian Marston says. “Through this collaboration with UKBIC, we are moving beyond the emerging black mass recycling industry and ensuring that these critical battery materials remain in the domestic supply chain. Having access to a manufacturing facility like this allows us to scale up and develop this innovative work, which is helping to position the U.K. at the forefront of sustainability and decarbonization.”
Altilium’s recycling process starts with dismantling and shredding end-of-life EV batteries to produce black mass, which is then processed using Altilium’s EcoCathode process. The company says its EcoCathode process can recover more than 95 percent of critical battery metals, including lithium. The cathode metals are then upcycled to produce a high-nickel NMC 811 CAM, ready for reuse in a new battery.
“We’re delighted to have been part of the team creating the U.K.’s first battery cells made using CAM containing recycled material,” says Ameir Mahgoub, head of product engineering at UKBIC. “This pioneering project could be just the start of a journey that sees the U.K. becoming less reliant on imported materials and create a new market in recycled EV batteries. We look forward to collaborating with Altilium on this exciting project as they take it forward.”
Latest from Recycling Today
- Acerinox names new North American Stainless CEO
- Greenwave closes 2024 books with red ink
- Steel Dynamics nets $217 million on record shipments
- Massive Chinese steelmaking rebound recorded in March
- LME looks into sustainable metal pricing
- OnePlanet Solar Recycling closes $7M seed financing round
- AMCS launches AMCS Platform Spring 2025 update
- Cyclic Materials to build rare earth recycling facility in Mesa, Arizona