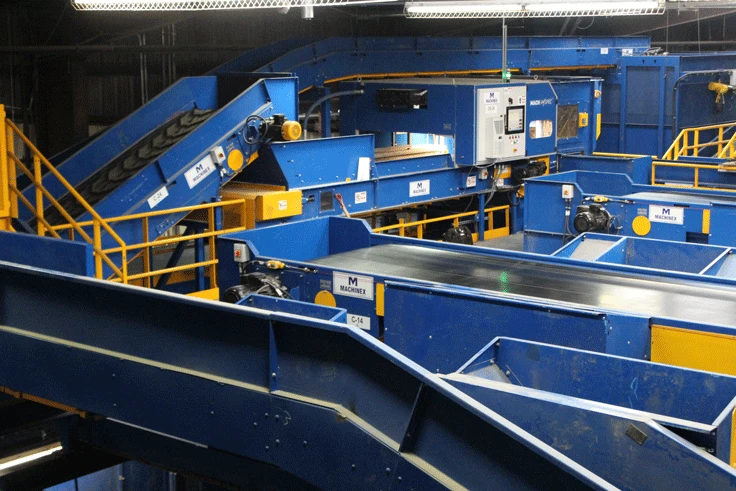
In response to market demand in the Denver area, Alpine Waste & Recycling, Commerce City, Colorado, says it has more than doubled its ability to process single-stream recycled materials, making the company the highest-capacity recycling processor in a contiguous 10-state region.
Alpine Waste & Recycling retooled its Altogether Recycling Plant at 645 West 53rd Place in Denver. The $5 million investment added all new equipment from Machinex, Plessisville, Quebec, with twice as many transfer belts as well as some material-sorting technology that was almost unimaginable when the plant first opened in 2007, Alpine says.
“We have come a long way in the recycling industry, and we’re proud to say that Alpine Waste & Recycling has never wavered in its role as a trendsetter,” says Brent Hildebrand, vice president of recycling at Alpine. “We’re excited to launch upon this next phase in which we will serve the community so effectively in its efforts to preserve our environment. Alpine’s investment in this plant will greatly increase the amount of material that is diverted away from landfills.”
The new plant will be able to handle 30 tons of material per hour at capacity, Alpine says.
Machinex says it designed the system to significantly increase processing capacity while adding flexibility for future needs and market changes.
The plant’s MACH Hyspec optical sorter optically identifies individual pieces of plastic and sorts them with perfectly aimed bursts of air, Alpine says. A ballistic separator, bounces 2D and 3D material for better separation of paper and containers. In addition, cardboard moves across the MACH OCC screen, with features waves of discs that separate the old corrugated containers (OCC) from smaller, unrelated recycling materials.
Alpine also will have the first device within a Colorado single-stream plant that condenses polystyrene foam packaging material (such as Styrofoam®) into recyclable bricks.
Additional improvements to the plant include logistical enhancements and equipment upgrades. The plant includes 26 new skylights; live-floor material bunkers that empty automatically into baler infeed conveyors; multiple bin-fed return conveyors for “missed” materials; a sorting conveyor for large rigid plastics; a debris roll screen for glass and other small materials; and redundant ability to load either of the plant balers automatically from any bunker.
The equipment upgrades include two new, larger balers, split paper screens, a triple-deck cardboard screen, an improved eddy current and vacuum separation system to recover aluminum and a new cross-belt magnet to recover steel cans.
Chris Hawn, Machinex North American sales manager, says, “The Alpine project is a great example of our desire to react to the industry’s current position. Along with our customers, we follow market conditions and recognize that there are current needs for optimization within an existing system while minimizing downtime.”
He adds, “Although Machinex has a proven track record with new turnkey installations, we recognize the need to improve upon existing operations and increase efficiency.”
Alpine Waste & Recycling is the largest privately held commercial waste, recycling and compost collection company in Colorado. With more than 80 trucks and more than 200 employees, Alpine handles 300,000-plus tons of waste, compost and recyclables per year.
Machinex develops sorting, waste management and recycling technology, having installed more than 300 turnkey facilities in partnership with leading material recovery facilities in Canada, the United States and Europe.
Latest from Recycling Today
- Turkish mills sampled wide scrap market in 2024
- GLE Scrap Metal acquires interest in Mallin Cos.
- 2024 marks strong year for Van Dyk
- Recycled metal portrayed as former dictator’s fiefdom
- Aqua Blaster takes aim at dust and fire suppression market
- Commentary: Merger opposition yields opponents of its own
- Textile recycler to open manufacturing facility in Vietnam
- Call2Recycle Canada, Ontario county achieve battery recycling milestone